What does MPI mean in ENGINEERING
MPI (Magnetic Particle Inspection) is a non-destructive testing (NDT) method used to detect surface and near-surface discontinuities in ferromagnetic materials. It is commonly employed in industries such as manufacturing, aerospace, and automotive to ensure the integrity of critical components.
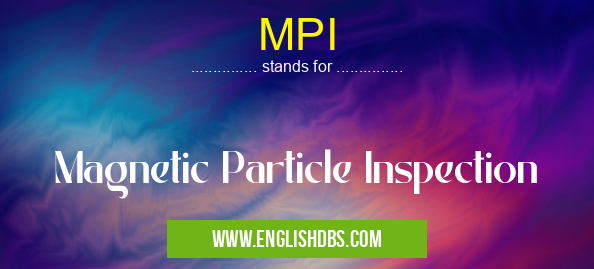
MPI meaning in Engineering in Academic & Science
MPI mostly used in an acronym Engineering in Category Academic & Science that means Magnetic Particle Inspection
Shorthand: MPI,
Full Form: Magnetic Particle Inspection
For more information of "Magnetic Particle Inspection", see the section below.
Principle of Operation
MPI involves magnetizing the test object and applying magnetic particles to its surface. These particles are attracted to areas where there is a discontinuity in the magnetic field, such as cracks, inclusions, or other defects. The accumulation of magnetic particles indicates the presence and location of the discontinuity, enabling its detection and subsequent repair or replacement.
Advantages of MPI
- High sensitivity: MPI can detect even small surface-breaking cracks and other discontinuities.
- Non-destructive: The test does not damage the component, allowing for repeated inspections.
- Fast and portable: MPI can be performed quickly and easily in the field or on-site.
- Cost-effective: MPI is a relatively inexpensive NDT method compared to others.
Applications of MPI
MPI is widely used in various industries to inspect:
- Welds in pipelines, pressure vessels, and other structures
- Forgings and castings for defects such as cracks, voids, and inclusions
- Aerospace components for fatigue cracks and other damage
- Automotive parts for surface defects and manufacturing flaws
Essential Questions and Answers on Magnetic Particle Inspection in "SCIENCE»ENGINEERING"
What is Magnetic Particle Inspection (MPI)?
Magnetic Particle Inspection (MPI) is a non-destructive testing (NDT) method used to detect surface and near-surface cracks, inclusions, and other defects in ferromagnetic materials. It utilizes magnetic particles to reveal the presence of magnetic field disturbances caused by the presence of defects.
How does MPI work?
In MPI, a magnetic field is induced in the test object. Ferromagnetic particles, such as iron oxide or iron powder, are then applied to the surface of the object. These particles are attracted to areas of high magnetic field disturbance, such as the edges of defects. The accumulation of particles forms visible indications of the defects.
What are the advantages of MPI?
MPI offers several advantages over other NDT methods:
- High sensitivity: Can detect very small defects
- Portable and easy to use
- Relatively low cost
- Can be used on a variety of ferromagnetic materials
What types of defects can MPI detect?
MPI is primarily used to detect surface and near-surface cracks and other defects that disrupt the magnetic field, such as:
- Fatigue cracks
- Heat-treating cracks
- Grinding cracks
- Laps and seams
- Inclusions
- Cold shuts
What are the limitations of MPI?
MPI has certain limitations:
- Only works on ferromagnetic materials
- May not detect defects below the surface
- Requires access to both sides of the test object (for certain methods)
- May be affected by material properties and surface conditions
Final Words: MPI is a valuable NDT technique that provides a reliable and efficient means of detecting surface and near-surface discontinuities in ferromagnetic materials. Its simplicity, cost-effectiveness, and high sensitivity make it a widely adopted method in industries that demand high-quality and safety-critical components.
MPI also stands for: |
|
All stands for MPI |