What does MPI mean in TECHNOLOGY
Magnetic Particle Inspection (MPI) is a non-destructive testing (NDT) technique used to detect surface and near-surface discontinuities in ferromagnetic materials. It is widely applied in industries such as manufacturing, automotive, and aerospace to ensure the integrity and safety of critical components.
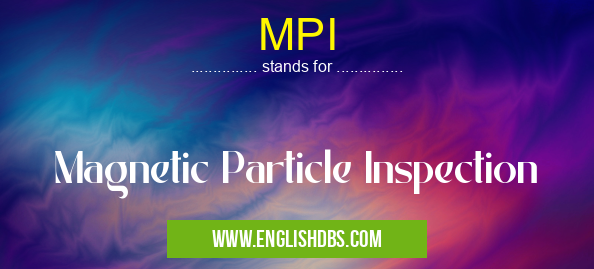
MPI meaning in Technology in Computing
MPI mostly used in an acronym Technology in Category Computing that means Magnetic Particle Inspection
Shorthand: MPI,
Full Form: Magnetic Particle Inspection
For more information of "Magnetic Particle Inspection", see the section below.
» Computing » Technology
MPI Meaning in COMPUTING
In computing, MPI stands for Message Passing Interface. It is a standard library for writing parallel programs that communicate using message passing. MPI allows programmers to create distributed applications that can run on multiple computers or processors, enabling efficient utilization of computational resources.
MPI Full Form
Magnetic Particle Inspection
What does MPI Stand for?
MPI stands for Magnetic Particle Inspection.
Process
MPI involves applying magnetic particles to the surface of the test piece. These particles are typically fine, ferromagnetic powders that align themselves with the magnetic field created by the discontinuity. The presence of these particles is then detected using various methods, such as visual inspection, fluorescent penetrants, or magnetic ink.
Advantages
- MPI is a relatively simple and cost-effective technique.
- It can detect both surface and near-surface discontinuities.
- It is suitable for a wide range of ferromagnetic materials.
- It provides clear visual indications of discontinuities.
Applications
- Inspecting welds for cracks and inclusions
- Detecting fatigue cracks in aircraft components
- Identifying surface defects in castings and forgings
- Examining pressure vessels and pipelines for damage
Essential Questions and Answers on Magnetic Particle Inspection in "COMPUTING»TECHNOLOGY"
What is Magnetic Particle Inspection (MPI)?
MPI is a non-destructive testing (NDT) method that uses magnetic fields and ferromagnetic particles to detect surface and near-surface defects in ferromagnetic materials.
How does MPI work?
MPI involves applying a magnetic field to the test object, which magnetizes the material. Ferromagnetic particles are then applied to the surface of the object. These particles are attracted to areas where the magnetic field is disturbed, indicating the presence of defects.
What types of defects can MPI detect?
MPI is primarily used to detect surface and near-surface defects, such as cracks, porosity, inclusions, and lack of fusion.
What are the advantages of MPI?
MPI offers several advantages, including:
- High sensitivity to surface and near-surface defects
- Non-destructive nature, allowing for repeated testing
- Relatively low cost and easy to perform
- Can be used on a wide range of ferromagnetic materials
What are the limitations of MPI?
MPI has some limitations, such as:
- Cannot detect defects below the surface
- May be affected by the presence of non-ferromagnetic materials
- Requires proper preparation of the test surface
- May not be suitable for all types of ferromagnetic materials
What industries use MPI?
MPI is widely used in various industries, including:
- Aerospace
- Automotive
- Power generation
- Oil and gas
- Manufacturing
Final Words: MPI is a valuable NDT technique that plays a crucial role in ensuring the reliability and safety of ferromagnetic components. It provides a cost-effective and efficient means of detecting surface and near-surface discontinuities, contributing to the overall integrity and quality of industrial products.
MPI also stands for: |
|
All stands for MPI |