What does NDI mean in ACADEMIC & SCIENCE
NDI stands for Nondestructive Inspection. It refers to a wide range of techniques used to evaluate the integrity of materials, components, structures, and systems without causing damage. NDI is essential in various industries, including manufacturing, aerospace, construction, and energy, for ensuring safety, reliability, and cost-effectiveness.
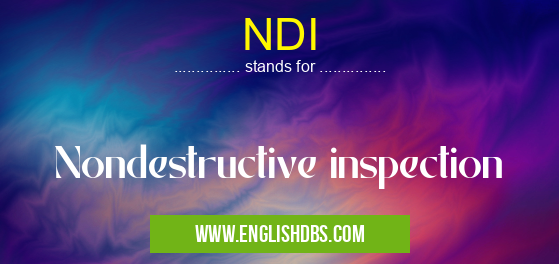
NDI meaning in Academic & Science in Academic & Science
NDI mostly used in an acronym Academic & Science in Category Academic & Science that means Nondestructive inspection
Shorthand: NDI,
Full Form: Nondestructive inspection
For more information of "Nondestructive inspection", see the section below.
Techniques of NDI
NDI comprises several techniques, each utilizing different principles and tools. Some common NDI techniques include:
- Ultrasonic Testing (UT): Uses high-frequency sound waves to detect flaws and measure material thickness.
- Radiographic Testing (RT): Employs X-rays or gamma rays to penetrate materials and reveal internal defects.
- Magnetic Particle Testing (MT): Utilizes a magnetic field to detect surface and subsurface cracks in ferromagnetic materials.
- Liquid Penetrant Testing (PT): Involves applying a penetrating liquid to the surface to identify cracks or porosity.
- Acoustic Emission Testing (AE): Monitors the release of acoustic energy to detect active flaws or stress in materials.
Benefits of NDI
NDI offers numerous benefits, including:
- Early Detection of Defects: NDI enables the detection of flaws and defects at an early stage, preventing catastrophic failures and costly repairs.
- Improved Safety and Reliability: By identifying potential issues before they become critical, NDI enhances the safety and reliability of equipment and structures.
- Reduced Downtime and Maintenance Costs: Early detection of defects allows for timely repairs, minimizing downtime and maintenance expenses.
- Increased Productivity: NDI helps optimize production processes by preventing defective parts from being produced, leading to increased efficiency and productivity.
Applications of NDI
NDI finds applications in a diverse range of industries, including:
- Manufacturing: Inspection of welds, castings, and composite materials for flaws and defects.
- Aerospace: Nondestructive testing of aircraft components, engines, and structures to ensure safety and reliability.
- Construction: Evaluation of concrete structures, bridges, and pipelines for cracks, corrosion, and other defects.
- Energy: Inspection of pipelines, storage tanks, and power plants for defects and corrosion.
Essential Questions and Answers on Nondestructive inspection in "SCIENCE»SCIENCE"
What is Nondestructive Inspection (NDI)?
NDI is a technique used to examine an object, component, or material without causing damage to the item being inspected. It is used to detect and characterize flaws, cracks, or other imperfections that could affect the safety, performance, or integrity of the object.
What are some common NDI techniques?
Common NDI techniques include visual inspection, ultrasonic testing, radiographic testing, eddy current testing, and magnetic particle testing. Each technique uses different principles and equipment to detect specific types of flaws.
Why is NDI important?
NDI is important because it allows for the early detection and characterization of flaws that could lead to catastrophic failures or accidents. By identifying and repairing flaws before they become critical, NDI helps to ensure the safety, reliability, and lifespan of equipment and structures.
Who performs NDI?
NDI is typically performed by trained and certified technicians who have specialized knowledge and experience in the specific NDI techniques being used. These technicians are often employed by inspection companies, manufacturers, or engineering firms.
What are the benefits of using NDI?
The benefits of using NDI include:
- Improved safety and reliability of equipment and structures
- Reduced risk of catastrophic failures or accidents
- Increased lifespan of assets
- Reduced maintenance and repair costs
- Improved quality control and product assurance
Final Words: NDI plays a vital role in ensuring the integrity, safety, and reliability of materials, components, and systems across various industries. By enabling the early detection of flaws and defects without causing damage, NDI contributes to cost-effectiveness, improved safety, and increased productivity. Continual advancements in NDI techniques and technologies drive innovation and enhance the capabilities of this essential inspection method.
NDI also stands for: |
|
All stands for NDI |