What does NDI mean in ENGINEERING
Nondestructive inspection (NDI) refers to a wide range of techniques used to assess the integrity of various materials and components without causing any damage to them. It plays a crucial role in ensuring safety, reliability, and quality control across numerous industries.
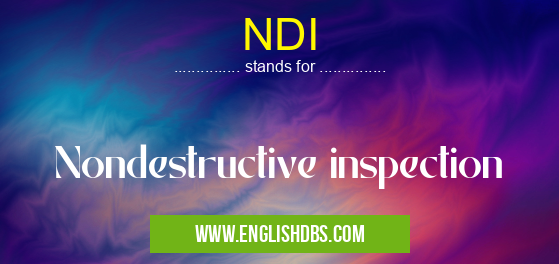
NDI meaning in Engineering in Academic & Science
NDI mostly used in an acronym Engineering in Category Academic & Science that means Nondestructive inspection
Shorthand: NDI,
Full Form: Nondestructive inspection
For more information of "Nondestructive inspection", see the section below.
What is NDI and its Importance?
NDI encompasses various methods that allow engineers and technicians to inspect and evaluate the condition of materials, structures, and components without affecting their functionality or integrity. These techniques are essential for detecting defects, corrosion, and other anomalies that could compromise the safety and performance of critical systems.
Applications of NDI
NDI finds applications in a diverse range of industries, including:
- Aerospace: Inspecting aircraft components for cracks, corrosion, and damage
- Automotive: Evaluating welds and castings for defects
- Construction: Detecting flaws in concrete structures and pipelines
- Energy: Ensuring the integrity of power plants, pipelines, and refineries
- Manufacturing: Identifying defects in raw materials, castings, and finished products
Methods of NDI
NDI encompasses a variety of methods, each with its own advantages and limitations:
- Visual Inspection: Using lighting and optical instruments to visually examine surfaces for defects
- Radiographic Testing (RT): Using X-rays or gamma rays to penetrate materials and reveal internal flaws
- Ultrasonic Testing (UT): Employing sound waves to detect defects and measure material thickness
- Eddy Current Testing (ET): Using electromagnetic fields to detect surface and subsurface defects in conductive materials
- Magnetic Particle Testing (MT): Magnetizing the material and applying magnetic particles to reveal surface-breaking defects
Essential Questions and Answers on Nondestructive inspection in "SCIENCE»ENGINEERING"
What is Nondestructive Inspection (NDI)?
NDI is a method of evaluating the integrity of materials and structures without causing any permanent damage. It is used in various industries to detect defects, such as cracks, corrosion, and other abnormalities, that could compromise safety or performance.
Why is NDI Important?
NDI is essential for ensuring the reliability of critical structures, components, and products. By detecting defects early on, it prevents failures that could lead to accidents, injuries, or financial losses. NDI helps maintain safety, optimize performance, and extend the lifespan of assets.
What are the Common NDI Techniques?
There are various NDI techniques available, including:
- Ultrasonic testing (UT): Uses high-frequency sound waves to detect internal defects.
- Radiographic testing (RT): Uses X-rays or gamma rays to create images of the internal structure.
- Magnetic particle testing (MT): Uses magnetic particles to detect surface cracks.
- Liquid penetrant testing (PT): Uses fluorescent dyes to detect surface defects.
- Visual testing (VT): Involves using the human eye and optical instruments to examine surfaces for defects.
What are the Advantages of Using NDI?
NDI offers several advantages, such as:
- It is a non-destructive method, preserving the integrity of the inspected object.
- It can detect defects that are not visible to the naked eye.
- It can be used on a wide range of materials and structures.
- It can be automated for efficient and repeatable inspections.
What are the Limitations of NDI?
Despite its advantages, NDI has certain limitations, including:
- It may not be able to detect all types of defects.
- It can be time-consuming and expensive for complex inspections.
- It requires skilled inspectors to interpret the results.
Who Performs NDI?
NDI is typically performed by qualified and certified technicians or engineers who have undergone specialized training and meet industry standards. They use advanced equipment and techniques to ensure accurate and reliable inspections.
How Often Should NDI Be Performed?
The frequency of NDI inspections depends on various factors, including:
- The criticality of the asset
- The expected lifespan of the asset
- The environmental conditions
- The inspection history Regular inspections are recommended to maintain asset integrity and prevent unexpected failures.
Final Words: NDI plays a critical role in maintaining safety, ensuring reliability, and enhancing quality control in numerous industries. It enables engineers and technicians to assess the condition of materials and components without damaging them, thereby preventing failures and minimizing downtime. The various methods of NDI provide valuable insights into the integrity of materials, components, and structures, enabling timely intervention and proactive maintenance.
NDI also stands for: |
|
All stands for NDI |