What does LM mean in COMPANIES & FIRMS
Lean Manufacturing (LM) is a comprehensive approach to production that aims to eliminate waste and maximize efficiency. It is an extension of the Toyota Production System, which was developed by Toyota in the mid-20th century. LM has been adopted by many industries worldwide and has proven effective in improving productivity, reducing costs, and enhancing customer satisfaction.
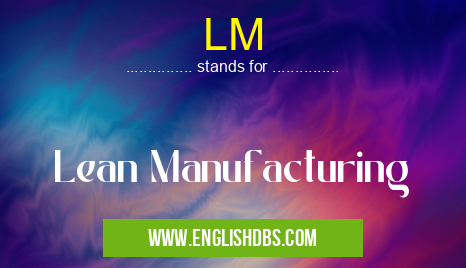
LM meaning in Companies & Firms in Business
LM mostly used in an acronym Companies & Firms in Category Business that means Lean Manufacturing
Shorthand: LM,
Full Form: Lean Manufacturing
For more information of "Lean Manufacturing", see the section below.
Key Principles of LM
LM is based on several key principles, including:
- Value stream mapping: Identifying and analyzing the steps involved in producing a product or service to identify and eliminate waste.
- Continuous improvement (Kaizen): Making incremental changes to processes over time to improve efficiency and eliminate waste.
- Just-in-time (JIT) production: Producing only what is needed, when it is needed, to avoid waste and inventory buildup.
- Total quality management (TQM): Involving all employees in the process of improving quality and eliminating defects.
- Employee empowerment: Providing employees with the authority and responsibility to make decisions and improve processes.
Benefits of LM
Implementing LM can provide numerous benefits for organizations, such as:
- Increased productivity and efficiency
- Reduced costs and inventory levels
- Improved quality and customer satisfaction
- Enhanced employee engagement and motivation
- Reduced lead times and increased responsiveness to customer needs
Essential Questions and Answers on Lean Manufacturing in "BUSINESS»FIRMS"
What is Lean Manufacturing (LM)?
Lean Manufacturing (LM) is a systematic approach to eliminate waste and improve efficiency in manufacturing processes. It focuses on creating a streamlined production system that reduces lead times, improves quality, and reduces costs.
What are the key principles of LM?
The key principles of LM include:
- Identifying and eliminating waste (e.g., overproduction, waiting, defects)
- Continuous improvement (Kaizen)
- Just-in-time (JIT) production
- Employee involvement and empowerment
- Total quality management (TQM)
What are the benefits of LM?
LM offers numerous benefits, such as:
- Reduced production costs
- Improved product quality
- Shorter lead times
- Increased productivity
- Enhanced customer satisfaction
- Improved employee morale
How can I implement LM in my manufacturing organization?
Implementing LM requires a comprehensive approach that involves:
- Developing a clear vision and strategy
- Identifying and mapping waste in the production process
- Implementing lean tools and techniques (e.g., 5S, kaizen events)
- Engaging employees and empowering them to identify and eliminate waste
- Continuously monitoring and improving processes
Is LM suitable for all types of manufacturing organizations?
LM is applicable to a wide range of manufacturing organizations, regardless of size or industry. It can be tailored to meet specific needs and objectives. However, it is essential to consider the organization's readiness and commitment to implementing the principles of LM.
Final Words: Lean Manufacturing is a powerful approach to production that has been proven to improve efficiency, reduce costs, and enhance customer satisfaction. By focusing on waste elimination, continuous improvement, and employee involvement, organizations can achieve significant benefits and gain a competitive advantage.
LM also stands for: |
|
All stands for LM |