What does WLS mean in UNCLASSIFIED
WLS (Wire Lubrication System) is an essential component in the manufacturing and processing industries, particularly in applications involving wire drawing, extrusion, and other wire-related processes. It plays a crucial role in ensuring the smooth operation of machinery and maintaining high-quality standards in the production of various wire products.
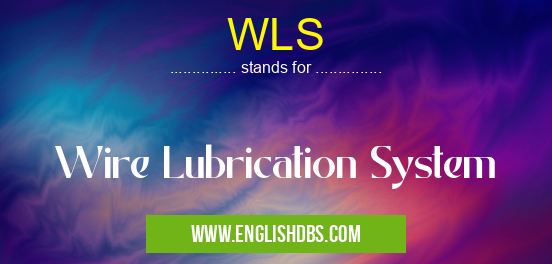
WLS meaning in Unclassified in Miscellaneous
WLS mostly used in an acronym Unclassified in Category Miscellaneous that means Wire Lubrication System
Shorthand: WLS,
Full Form: Wire Lubrication System
For more information of "Wire Lubrication System", see the section below.
What is WLS?
WLS is a specialized system designed to provide lubrication to wires during manufacturing processes. It consists of a reservoir of lubricating fluid, a pump, and a series of nozzles or applicators that distribute the lubricant evenly onto the wire surface. The primary purpose of WLS is to reduce friction between the wire and the machinery components, minimizing wear and tear, and improving the overall efficiency of the process.
Benefits of WLS
- Reduced Friction: Lubrication significantly reduces friction between the wire and the machine parts, minimizing wear and tear on both the wire and the equipment. This leads to extended equipment life, reduced downtime, and lower maintenance costs.
- Improved Wire Quality: WLS ensures that the wire is evenly lubricated, preventing surface damage and improving the overall quality of the finished product. Lubricated wires have a smoother surface, better dimensional accuracy, and enhanced resistance to corrosion and abrasion.
- Increased Productivity: Reduced friction and improved wire quality result in increased productivity. The smooth operation of machinery and the reduced need for rework or scrap minimize production time and increase output.
- Energy Savings: Lubricated wires require less force to draw or extrude, reducing the energy consumption of the machinery. This leads to lower operating costs and improved environmental sustainability.
Applications of WLS
WLS is widely used in diverse industries, including:
- Wire Drawing: Provides lubrication during the drawing process, reducing friction and improving wire quality.
- Extrusion: Lubricates wires during extrusion, facilitating smooth flow and preventing damage to the wire surface.
- Coating: Used to apply lubricating coatings onto wires, enhancing their corrosion resistance and electrical conductivity.
- Cable Manufacturing: Lubricates individual wires before they are bundled into cables, ensuring easy handling and preventing tangling.
Essential Questions and Answers on Wire Lubrication System in "MISCELLANEOUS»UNFILED"
What is a Wire Lubrication System (WLS)?
A WLS is a mechanism designed to apply lubricant to wire ropes or cables during operation, reducing friction and wear. It consists of lubrication units that dispense lubricant onto the wire rope as it passes through, ensuring optimal lubrication for smooth and efficient operation.
What are the benefits of using a WLS?
Implementing a WLS offers several benefits, including:
- Reduced friction, leading to increased efficiency and reduced energy consumption.
- Extended wire rope lifespan by minimizing wear and corrosion.
- Improved safety by ensuring proper lubrication and preventing premature failure.
- Reduced downtime and maintenance costs associated with wire rope replacement.
What types of WLS are available?
There are two main types of WLS:
- Open systems: These systems apply lubricant directly onto the wire rope using brushes or spray nozzles.
- Closed systems: These systems fully enclose the wire rope in a lubricated chamber, providing continuous and consistent lubrication.
What factors should be considered when selecting a WLS?
When choosing a WLS, consider the following factors:
- Wire rope size and type
- Operating conditions (e.g., temperature, humidity, exposure to contaminants)
- Lubricant type and compatibility
- Desired lubrication frequency and coverage
- Ease of installation and maintenance
How can I maintain a WLS effectively?
Effective WLS maintenance involves:
- Regularly inspecting and cleaning the system to remove debris and ensure proper operation.
- Monitoring lubricant levels and refilling as needed.
- Checking for signs of wear or damage and addressing them promptly.
- Following the manufacturer's recommended maintenance schedule.
Final Words: WLS is a critical component in the wire manufacturing and processing industries. By providing effective lubrication, it reduces friction, improves wire quality, increases productivity, and lowers energy consumption. As a result, WLS plays a vital role in maintaining high-quality standards, optimizing production processes, and enhancing the overall efficiency and profitability of manufacturing operations.
WLS also stands for: |
|
All stands for WLs |