What does HDI mean in UNCLASSIFIED
High Density Interconnected (HDI) is a technology used in the manufacturing of printed circuit boards (PCBs). It involves creating PCBs with a higher density of interconnections, meaning more electrical connections can be made within a smaller area. HDI PCBs are typically used in electronic devices where space is limited, such as smartphones, laptops, and medical devices.
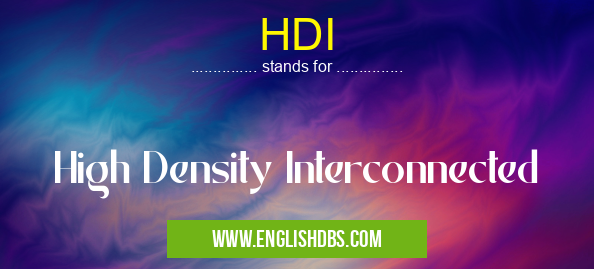
HDI meaning in Unclassified in Miscellaneous
HDI mostly used in an acronym Unclassified in Category Miscellaneous that means High Density Interconnected
Shorthand: HDI,
Full Form: High Density Interconnected
For more information of "High Density Interconnected", see the section below.
Benefits of HDI PCBs
- Increased circuit density: HDI PCBs allow for a higher number of electrical connections within a smaller area, which can reduce the overall size of the device.
- Improved performance: HDI PCBs can improve the performance of electronic devices by reducing signal loss and crosstalk.
- Reduced manufacturing costs: HDI PCBs can be manufactured with lower production costs compared to traditional PCBs due to the use of smaller components and fewer layers.
Essential Questions and Answers on High Density Interconnected in "MISCELLANEOUS»UNFILED"
What is High Density Interconnected (HDI)?
High Density Interconnected (HDI) refers to printed circuit board (PCB) technology that achieves high component density and signal routing capabilities by utilizing advanced fabrication techniques. HDI PCBs are designed to accommodate a large number of components and interconnects within a compact space.
What are the benefits of using HDI PCBs?
HDI PCBs offer several benefits, including:
- Reduced board size: HDI technology allows for smaller PCBs, which can be crucial for space-constrained applications.
- Improved performance: HDI PCBs can improve signal integrity and reduce crosstalk due to their optimized layout and routing techniques.
- Enhanced reliability: The use of advanced manufacturing processes and materials in HDI PCBs ensures higher reliability and durability.
What are the different types of HDI PCBs?
HDI PCBs can be categorized based on their construction and fabrication methods:
- Type 1 HDI: Features at least one layer with microvias (vias with a diameter of 150 microns or less).
- Type 2 HDI: Similar to Type 1, but with multiple layers containing microvias.
- Type 3 HDI: Utilizes sequential lamination and laser drilling to achieve even higher interconnect density.
What industries use HDI PCBs?
HDI PCBs are widely used in various industries, including:
- Telecommunications
- Automotive
- Medical devices
- Aerospace
- Consumer electronics
What are the challenges in designing HDI PCBs?
Designing HDI PCBs requires careful consideration of several factors:
- Component selection: Choosing components with small footprints and high density is essential.
- Routing: Optimizing signal routing to minimize crosstalk and impedance issues is crucial.
- Manufacturing processes: Understanding the capabilities and limitations of available fabrication techniques is essential to ensure design feasibility.
Final Words: HDI PCBs are a valuable technology for the manufacturing of electronic devices, offering benefits such as increased circuit density, improved performance, and reduced manufacturing costs. As electronic devices continue to become smaller and more complex, HDI PCBs will play an increasingly important role in their design and development.
HDI also stands for: |
|
All stands for HDI |