What does HDI mean in UNCLASSIFIED
HDI stands for High Density Interconnector, which is a type of printed circuit board (PCB) that is designed to accommodate a high number of electrical components and connections within a limited space. It is a critical component in various electronic devices, enabling the efficient and reliable transmission of signals and power between components.
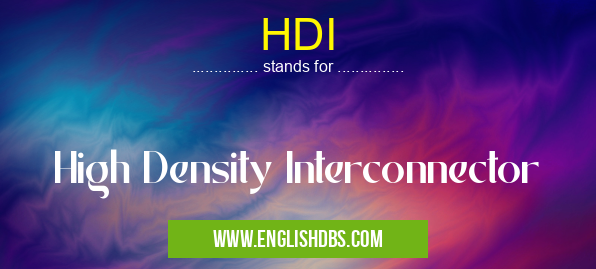
HDI meaning in Unclassified in Miscellaneous
HDI mostly used in an acronym Unclassified in Category Miscellaneous that means High Density Interconnector
Shorthand: HDI,
Full Form: High Density Interconnector
For more information of "High Density Interconnector", see the section below.
Uses of HDI
- Mobile Devices: HDIs are commonly used in smartphones, tablets, and wearables, where space is limited and high component density is essential.
- Laptops and Desktops: HDIs are found in motherboards and other components of laptops and desktops, providing high-speed data transfer and power distribution.
- Automotive Electronics: HDIs are used in automotive applications, such as control modules and infotainment systems, where reliability and durability are crucial.
- Medical Devices: HDIs are employed in medical devices, such as pacemakers and implantable devices, where size and performance are critical.
Advantages of HDI
- High Component Density: HDIs allow for a large number of components to be placed in a small area, maximizing space utilization.
- Reduced Signal Loss: The use of high-quality materials and advanced manufacturing techniques minimizes signal loss, ensuring reliable data transmission.
- Improved Performance: HDIs enable faster signal speeds and lower power consumption, enhancing the overall performance of electronic devices.
- Cost-Effectiveness: Despite their complexity, HDIs can be cost-effective in high-volume applications, as they reduce the need for multiple PCBs and components.
Essential Questions and Answers on High Density Interconnector in "MISCELLANEOUS»UNFILED"
What is High Density Interconnector (HDI)?
High Density Interconnector (HDI) is a type of printed circuit board (PCB) that offers high interconnection density with a reduced board size. It utilizes advanced manufacturing techniques to accommodate a greater number of electrical components and routing layers within a compact space.
What are the benefits of using HDI PCBs?
HDI PCBs provide several advantages, including:
- Increased functionality: By allowing for a higher density of components, HDI PCBs enable the incorporation of more features and capabilities into a smaller device.
- Reduced size: The compact design of HDI PCBs allows for the creation of smaller electronic devices, which is crucial in industries such as consumer electronics and aerospace.
- Improved performance: The optimized routing and reduced signal path lengths in HDI PCBs contribute to enhanced electrical performance and reduced crosstalk.
- Cost-effectiveness: Despite the advanced manufacturing techniques, HDI PCBs can be cost-effective due to their reduced material usage and space requirements.
What are the applications of HDI PCBs?
HDI PCBs are widely used in various industries, including:
- Consumer electronics: Smartphones, tablets, laptops, and wearable devices.
- Medical devices: Implantable devices, diagnostic equipment, and monitoring systems.
- Automotive electronics: Control modules, sensors, and infotainment systems.
- Aerospace and defense: Navigation systems, avionics, and communication equipment.
- Telecommunications: Network infrastructure, servers, and routers.
What are the design considerations for HDI PCBs?
Designing HDI PCBs requires careful attention to several factors:
- Layer count and stackup: Determining the optimal number of layers and their arrangement to accommodate the required routing and component placement.
- Component density: Selecting components that fit within the reduced space constraints and maximizing the number of components accommodated.
- Signal routing: Optimizing the routing to minimize signal path lengths and crosstalk, especially with high-speed signals.
- Thermal management: Designing for adequate heat dissipation to prevent overheating and ensure reliable operation.
What are the manufacturing challenges of HDI PCBs?
Manufacturing HDI PCBs poses certain challenges:
- Fine line and spacing: Producing PCBs with extremely narrow tracks and gaps requires advanced lithography and etching techniques.
- Via formation: Creating reliable vias with small diameters and high aspect ratios is crucial for dense interconnections.
- Layer alignment: Maintaining precise alignment between multiple layers is essential for electrical integrity.
- Component placement: Placing components accurately within tight spaces requires specialized equipment and processes.
Final Words: HDI technology plays a vital role in enabling the development of compact and powerful electronic devices. Its ability to accommodate a high density of components and connections while ensuring high performance and reliability makes it an essential component in various industries. As technology continues to evolve, HDIs will continue to be refined and utilized in even more advanced applications.
HDI also stands for: |
|
All stands for HDI |