What does SPDU mean in MANAGEMENT
SPDU stands for SPARE PARTS DESPATCH UNIT. It is a crucial component within the maintenance and repair operations of various industries, including manufacturing, transportation, and energy. SPDU plays a pivotal role in ensuring the availability and timely delivery of spare parts to maintain the smooth functioning of equipment and systems.
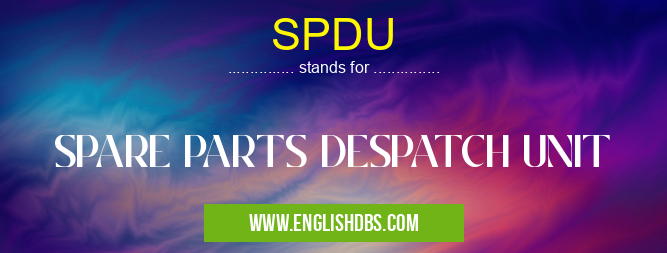
SPDU meaning in Management in Business
SPDU mostly used in an acronym Management in Category Business that means SPARE PARTS DESPATCH UNIT
Shorthand: SPDU,
Full Form: SPARE PARTS DESPATCH UNIT
For more information of "SPARE PARTS DESPATCH UNIT", see the section below.
» Business » Management
SPDU Function
The primary function of a SPDU is to manage the inventory, storage, and distribution of spare parts for specific equipment or machinery. It is responsible for:
- Maintaining an adequate inventory of spare parts based on historical data, usage patterns, and criticality analysis.
- Ensuring the availability of parts for scheduled maintenance, emergency repairs, and unexpected breakdowns.
- Receiving, storing, and issuing spare parts in a secure and efficient manner.
- Coordinating with suppliers to procure parts when necessary.
- Tracking the usage and replenishment of spare parts to optimize inventory levels and prevent shortages.
Importance of SPDU
An efficient SPDU is essential for several reasons:
- Reduced Downtime: By ensuring the availability of spare parts, SPDU minimizes downtime during equipment repairs, preventing production losses and service disruptions.
- Improved Productivity: Timely availability of parts allows maintenance teams to quickly address issues, enhancing equipment performance and overall productivity.
- Cost Savings: Effective inventory management and proactive procurement practices help optimize spare parts spending, reducing unnecessary costs.
- Enhanced Safety: Access to proper spare parts reduces the risk of equipment failures, ensuring a safe working environment.
Essential Questions and Answers on SPARE PARTS DESPATCH UNIT in "BUSINESS»MANAGEMENT"
What is a Spare Parts Despatch Unit (SPDU)?
An SPDU is a dedicated facility within a manufacturing or maintenance organization that is responsible for the storage, management, and distribution of spare parts. It ensures that critical spare parts are readily available to meet unexpected maintenance or repair needs, minimizing equipment downtime and maximizing production efficiency.
What are the key functions of an SPDU?
The primary functions of an SPDU include:
- Receiving and inspecting incoming spare parts
- Storing and managing spare parts inventory
- Monitoring spare parts usage and replenishment levels
- Processing orders and dispatching spare parts to maintenance crews or external customers
- Maintaining accurate records of spare parts availability and transactions
- Collaborating with other departments, such as maintenance, engineering, and procurement, to ensure efficient spare parts management.
What are the benefits of having an SPDU?
Implementing an SPDU offers several advantages, including:
- Reduced equipment downtime: By ensuring that spare parts are readily available, SPDUs minimize the time required for repairs and maintenance, keeping critical equipment operational.
- Improved maintenance planning: SPDUs provide real-time visibility into spare parts inventory, allowing maintenance teams to plan and schedule preventive maintenance activities more effectively.
- Optimized spare parts inventory: SPDUs help organizations optimize their spare parts inventory by identifying slow-moving or obsolete items and ensuring that inventory levels are aligned with actual usage.
- Reduced costs: SPDUs help reduce overall maintenance costs by minimizing the need for emergency spare parts purchases and reducing inventory carrying costs.
What are the best practices for managing an SPDU?
Effective SPDU management involves adhering to certain best practices, such as:
- Establishing clear inventory management procedures
- Implementing inventory control systems to track spare parts usage and replenishment
- Conducting regular inventory audits to ensure accuracy and prevent shortages
- Collaborating with maintenance teams to forecast spare parts demand
- Training maintenance personnel on proper spare parts handling and storage techniques
- Maintaining documentation and records of all spare parts transactions
- Regularly reviewing and updating SPDU processes and procedures to ensure efficiency and alignment with changing needs.
Final Words: In conclusion, SPDU plays a significant role in maintaining equipment uptime, reducing downtime, improving productivity, and ensuring safety in various industries. By managing spare parts inventory and facilitating their timely distribution, SPDU contributes to efficient maintenance operations and overall business success.