What does HBCM mean in CONSTRUCTION
HBCM stands for Hull Block Construction Method. It is a shipbuilding technique that involves constructing the ship's hull in large, pre-fabricated sections called "hull blocks". These blocks are then assembled and welded together to form the complete hull structure.
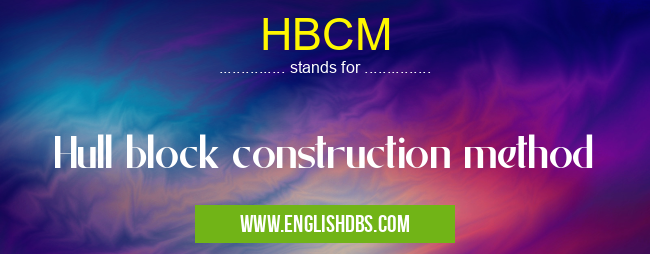
HBCM meaning in Construction in Miscellaneous
HBCM mostly used in an acronym Construction in Category Miscellaneous that means Hull block construction method
Shorthand: HBCM,
Full Form: Hull block construction method
For more information of "Hull block construction method", see the section below.
Benefits of HBCM
- Increased Efficiency: HBCM allows for parallel construction of hull blocks, reducing overall construction time.
- Improved Quality: The controlled environment of the block construction facility enables better quality control and inspection.
- Reduced Waste: Pre-fabrication minimizes material waste and reduces the need for rework.
- Improved Safety: Block construction minimizes the need for workers to operate at great heights or in confined spaces.
- Increased Flexibility: HBCM allows for easier customization and modification to ship designs.
Process of HBCM
- Design and Planning: The ship's design is finalized, and the hull is divided into individual hull blocks.
- Block Construction: The hull blocks are fabricated in specialized facilities using precision cutting, welding, and assembly techniques.
- Assembly and Welding: The pre-fabricated hull blocks are transported to the shipyard and assembled together using cranes and welding equipment.
- Outfitting and Completion: Once the hull is complete, it undergoes outfitting, where machinery, systems, and other components are installed.
Essential Questions and Answers on Hull block construction method in "MISCELLANEOUS»CONSTRUCTION"
What is Hull Block Construction Method (HBCM)?
HBCM is a shipbuilding technique where a ship's hull is divided into discrete, pre-fabricated blocks. These blocks are constructed in a controlled environment, typically in a shipyard or fabrication yard, before being assembled into the complete hull at a dock or slipway.
What are the advantages of using HBCM?
HBCM offers several advantages over traditional shipbuilding methods, including:
- Increased efficiency: Blocks can be constructed simultaneously in multiple locations, reducing overall construction time.
- Improved quality control: Blocks are built in a controlled environment, ensuring high-quality construction.
- Reduced labor costs: Automation and pre-fabrication techniques can reduce labor requirements.
- Enhanced flexibility: Blocks can be easily modified or replaced, allowing for changes in ship design or configuration.
What types of vessels are typically built using HBCM?
HBCM is commonly used for constructing a wide range of vessels, including:
- Naval vessels: Submarines, destroyers, and aircraft carriers.
- Commercial vessels: Cargo ships, tankers, and cruise liners.
- Offshore structures: Rigs, platforms, and floating production storage and offloading (FPSO) units.
How does the assembly process work in HBCM?
Once the hull blocks are fabricated, they are transported to the dock or slipway for assembly. The blocks are carefully aligned and joined together using welding, bolting, or other techniques. Once the hull is complete, it is outfitted with systems and equipment before being launched into the water.
What are the challenges associated with HBCM?
While HBCM offers numerous benefits, it also presents some challenges:
- Coordination: Coordinating the construction and assembly of multiple blocks requires careful planning and communication.
- Transportation: Transporting large blocks to the assembly site can be logistically complex and expensive.
- Integration: Ensuring that the blocks fit together seamlessly during assembly is crucial for the overall structural integrity of the vessel.
Final Words: HBCM is an advanced shipbuilding method that offers numerous benefits, including increased efficiency, improved quality, and enhanced safety. It has become a widely adopted practice in shipyards worldwide, contributing to the production of high-quality and cost-effective vessels.