What does NDE mean in OPTICS
NDE (Nondestructive Evaluation) is a comprehensive testing technique used in various industries to inspect materials, components, and structures for defects, flaws, and other anomalies without causing damage to the specimen. It plays a crucial role in ensuring the integrity, safety, and reliability of numerous systems and components in engineering, manufacturing, and construction.
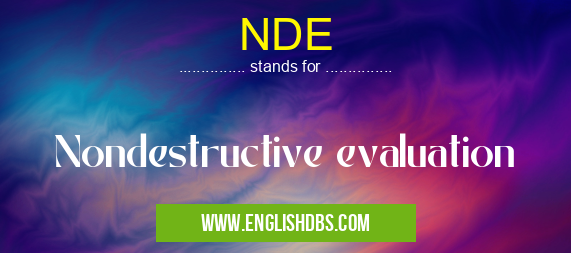
NDE meaning in Optics in Academic & Science
NDE mostly used in an acronym Optics in Category Academic & Science that means Nondestructive evaluation
Shorthand: NDE,
Full Form: Nondestructive evaluation
For more information of "Nondestructive evaluation", see the section below.
NDE Meaning in SCIENCE
In the scientific context, NDE encompasses a wide range of methods and technologies that utilize physical principles and engineering techniques to assess the condition of materials, structures, and components. NDE techniques are non-destructive, meaning they do not alter or harm the tested specimen. By employing various mechanisms such as ultrasonic, radiographic, acoustic emission, magnetic, and thermal methods, NDE allows for the detection, characterization, and quantification of defects and anomalies.
NDE Full Form
Nondestructive Evaluation (NDE)
What does NDE Stand for?
NDE stands for Nondestructive Evaluation, a field of science and engineering that deals with the development and application of techniques to assess the condition of materials, components, and structures without causing damage to the specimen.
Applications of NDE
NDE has numerous applications across various industries, including:
- Aerospace: Inspecting aircraft components for cracks, corrosion, and other defects.
- Automotive: Evaluating engine parts, welds, and other critical components.
- Manufacturing: Verifying the integrity of welds, castings, and other fabricated components.
- Construction: Assessing the condition of bridges, buildings, and other structures.
- Medical: Imaging the human body for medical diagnostics and disease detection.
Benefits of NDE
- Prevents catastrophic failures: NDE helps identify and address defects before they escalate into major failures, minimizing safety risks and costly repairs.
- Improves reliability: By detecting and rectifying flaws, NDE enhances the reliability and longevity of critical components and systems.
- Cost-effective: NDE is often more cost-effective than destructive testing methods while providing valuable insights into the condition of the specimen.
- Versatile: NDE techniques can be tailored to inspect a wide variety of materials, shapes, and sizes.
Essential Questions and Answers on Nondestructive evaluation in "SCIENCE»OPTICS"
What is nondestructive evaluation (NDE)?
Nondestructive evaluation (NDE) is a process used to inspect materials and components without damaging them. NDE methods are used to detect and characterize defects, flaws, and other features that may affect the integrity or performance of a material or component.
What are the different types of NDE methods?
There are various NDE methods, each with its own advantages and limitations. Common methods include:
- Ultrasonic testing: Uses sound waves to detect internal defects and measure material thickness.
- Radiography testing: Uses X-rays or gamma rays to create images of the internal structure of a material.
- Visual inspection: Examines a material's surface for visible defects.
- Magnetic particle testing: Detects surface and near-surface cracks by applying a magnetic field and ferromagnetic particles.
What are the advantages of using NDE methods?
NDE methods offer several advantages:
- Non-destructive: They do not damage the material or component being inspected.
- Quick and efficient: NDE methods can be automated and performed quickly.
- Cost-effective: NDE can help identify defects early, preventing costly repairs or failures.
- Improved safety: NDE can ensure the safety of materials and components used in critical applications.
What industries use NDE methods?
NDE methods are used in various industries, including:
- Aerospace and aviation: Inspecting aircraft components and structures.
- Automotive: Evaluating welds, castings, and other parts.
- Construction: Inspecting bridges, buildings, and pipelines.
- Energy: Examining power plant components, pipelines, and wind turbines.
- Manufacturing: Verifying the integrity of manufactured products.
Final Words: NDE is a vital tool in ensuring the safety, reliability, and cost-effectiveness of various systems and components in engineering, manufacturing, and construction. By utilizing advanced techniques to detect and characterize defects without causing damage, NDE contributes significantly to the integrity and durability of critical infrastructure, machinery, and medical devices.
NDE also stands for: |
|
All stands for NDE |