What does FGI mean in UNCLASSIFIED
Finished Goods Inventory (FGI) is a crucial aspect of inventory management, representing the stock of completed products ready for sale to customers. Understanding FGI is essential for optimizing inventory levels and ensuring efficient supply chain operations.
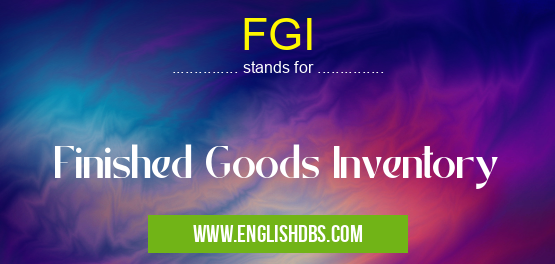
FGI meaning in Unclassified in Miscellaneous
FGI mostly used in an acronym Unclassified in Category Miscellaneous that means Finished Goods Inventory
Shorthand: FGI,
Full Form: Finished Goods Inventory
For more information of "Finished Goods Inventory", see the section below.
Meaning and Significance
FGI refers to the inventory of finished goods that have undergone all necessary production processes and are available for immediate sale. It is distinguished from other types of inventory, such as raw materials or work-in-progress (WIP), which are still in the production pipeline. Maintaining an optimal FGI level is crucial for meeting customer demand while minimizing inventory carrying costs.
Key Features
- Ready for Sale: FGI comprises products that have met quality standards and are ready to be shipped to customers.
- Inventory Value: FGI represents a significant portion of a company's total inventory value.
- Cost of Goods Sold (COGS): As finished goods are sold, their cost is recognized as COGS, reducing the FGI value.
- Inventory Turnover: FGI turnover measures how quickly finished goods are sold and replaced. A high turnover rate indicates efficient inventory management.
Benefits of Optimizing FGI
- Improved Cash Flow: Maintaining optimal FGI levels reduces the risk of overstocking and improves cash flow by ensuring that inventory is not tied up unnecessarily.
- Reduced Storage Costs: Optimizing FGI minimizes the need for storage space, reducing inventory carrying costs.
- Enhanced Customer Satisfaction: Maintaining adequate FGI levels ensures that customer orders can be fulfilled promptly, enhancing customer satisfaction.
- Supply Chain Efficiency: Proper FGI management aligns with production and sales processes, improving overall supply chain efficiency.
Essential Questions and Answers on Finished Goods Inventory in "MISCELLANEOUS»UNFILED"
What is Finished Goods Inventory (FGI)?
Finished Goods Inventory (FGI) refers to the total quantity of completed products that are ready for sale or distribution to customers. It represents the end result of the production process and includes items that have undergone all necessary manufacturing steps.
Why is FGI important?
FGI is important for several reasons:
- Sales fulfillment: Ensures that there is sufficient inventory to meet customer demand.
- Production planning: Helps manufacturers plan production schedules based on expected sales and inventory levels.
- Financial analysis: Provides data for calculating the cost of goods sold (COGS) and evaluating inventory management efficiency.
How is FGI measured?
FGI can be measured in various ways, including:
- Quantity: The total number of units or items in the inventory.
- Value: The total monetary value of the inventory, typically based on the cost of goods manufactured.
- Physical count: A manual or automated count of the actual physical inventory.
How can businesses optimize FGI management?
Businesses can optimize FGI management through strategies such as:
- Just-in-time (JIT) inventory: Minimizing inventory levels by producing only what is needed when it is needed.
- Safety stock: Maintaining a buffer of inventory to mitigate demand fluctuations and supply chain disruptions.
- Warehouse management systems (WMS): Using software to track and manage inventory levels, automate processes, and optimize storage.
What are the potential risks associated with FGI?
Potential risks associated with FGI include:
- Excess inventory: Holding too much inventory can tie up cash, lead to obsolescence, and increase storage costs.
- Stockouts: Running out of inventory can result in lost sales, customer dissatisfaction, and damage to reputation.
- Inventory damage: Physical damage or spoilage of inventory can result in financial losses and supply chain disruptions.
Final Words: FGI is a critical component of inventory management that represents the stock of completed products ready for sale. Optimizing FGI levels is essential for maximizing inventory efficiency, reducing costs, and ensuring customer satisfaction. By effectively managing FGI, businesses can enhance their financial performance and improve their overall supply chain operations.