What does QCI mean in UNCLASSIFIED
QCI stands for Quality Control Incident. It refers to an incident or event that occurs during the manufacturing or production process, resulting in a deviation from established quality standards. QCIs can range from minor issues that do not affect product functionality to major defects that require immediate corrective action.
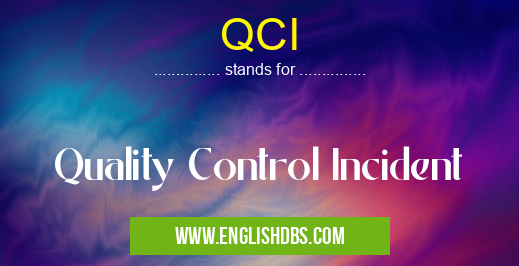
QCI meaning in Unclassified in Miscellaneous
QCI mostly used in an acronym Unclassified in Category Miscellaneous that means Quality Control Incident
Shorthand: QCI,
Full Form: Quality Control Incident
For more information of "Quality Control Incident", see the section below.
Types of QCIs
QCIs can be classified into different types based on their severity and impact:
- Minor QCIs: These are relatively minor issues that do not significantly affect product quality or functionality. They may involve minor cosmetic defects, such as scratches or blemishes.
- Moderate QCIs: These QCIs are more serious than minor ones but still do not pose a major risk to product safety or performance. They may include issues such as component misalignment or improper assembly.
- Major QCIs: These are serious incidents that can significantly affect product quality and safety. They may involve defects that could lead to product failures or even safety hazards.
Causes of QCIs
QCIs can be caused by a variety of factors, including:
- Human error
- Equipment malfunction
- Raw material defects
- Process deviations
- Environmental factors
Consequences of QCIs
QCIs can have significant consequences for manufacturers, including:
- Product recalls: Major QCIs may result in product recalls, which can be costly and damage brand reputation.
- Increased costs: QCIs can lead to increased production costs, as defective products need to be repaired or replaced.
- Delayed shipments: QCIs can cause delays in product shipments, resulting in lost revenue and customer dissatisfaction.
Prevention and Mitigation of QCIs
Manufacturers can implement various measures to prevent and mitigate QCIs, such as:
- Implementing rigorous quality control procedures: Establishing clear quality standards and inspection processes can help identify and address potential defects early on.
- Training and empowering staff: Providing proper training to staff and empowering them to make quality-related decisions can reduce human error.
- Utilizing advanced technology: Employing automated inspection systems and data analytics can improve accuracy and efficiency in quality control.
- Establishing a culture of quality: Fostering a culture of quality within the organization, where all employees are committed to maintaining high standards, can significantly reduce QCIs.
Essential Questions and Answers on Quality Control Incident in "MISCELLANEOUS»UNFILED"
What is a Quality Control Incident (QCI)?
A QCI is an event that may have impacted the quality or integrity of a product or service. It can include incidents such as errors, defects, or non-conformances.
What causes QCIs?
QCIs can be caused by various factors, including human error, equipment malfunctions, or process failures.
What are the consequences of a QCI?
The consequences of a QCI can range from minor inconvenience to significant financial loss or harm to reputation.
What is the process for reporting a QCI?
The process for reporting a QCI will vary depending on the organization and industry. Typically, a QCI should be documented, investigated, and corrective actions taken to prevent recurrence.
How can QCIs be prevented?
QCIs can be prevented through effective quality management practices, such as adhering to established processes, regular inspections, and employee training.
What role do quality control measures play in preventing QCIs?
Quality control measures are implemented to identify and eliminate potential QCIs by inspecting and testing products or services throughout the production process.
What are the benefits of addressing QCIs promptly?
Addressing QCIs promptly minimizes the potential impact on customers, reduces the risk of further incidents, and allows organizations to take corrective actions to improve quality.
How can organizations learn from QCIs?
Organizations can use QCIs as learning opportunities to identify areas for improvement and strengthen their quality management systems. By analyzing the root causes of QCIs, organizations can implement preventive measures and enhance product or service quality.
Final Words: QCI is a crucial aspect of quality management in manufacturing and production. By understanding the causes, consequences, and prevention strategies of QCIs, manufacturers can ensure that they deliver high-quality products that meet customer expectations and regulatory requirements.
QCI also stands for: |
|
All stands for QCI |