What does XMLM mean in MUSIC
XMLM stands for XM Liquid Metal. It is an alloy made up of a combination of metals that are used in the production of various industrial components. This alloy has several advantages over traditional metals and is often used in the manufacture of high-performance parts such as car engine blocks, aircraft landing gear, and medical implants. XMLM is known for its superior strength and ductility compared to other metals, and it is highly resistant to corrosion, heat, and wear.
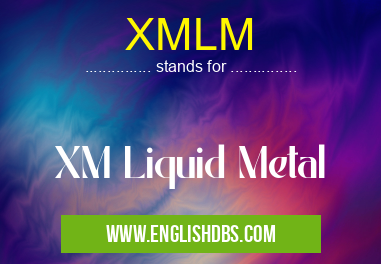
XMLM meaning in Music in Community
XMLM mostly used in an acronym Music in Category Community that means XM Liquid Metal
Shorthand: XMLM,
Full Form: XM Liquid Metal
For more information of "XM Liquid Metal", see the section below.
Advantages of XMLM
XMLM has several advantages over traditional metals including greater strength (yield strength being twice that of 304 stainless steel), increased ductility (ability to bend without breaking), higher levels of pressure resistance due to its uniform grain structure, excellent weldability and corrosion resistance when exposed to extreme conditions (high temperatures or acidic environments). In addition to these attributes, XMLM also has outstanding wear and abrasion properties – making it ideal for applications such as automotive pistons where abrasion can cause parts failure over time. Finally, because it does not contain lead or any other hazardous substances like many other metal alloys – this material does not have any potential health risks associated with it like some other alloys do.
Essential Questions and Answers on XM Liquid Metal in "COMMUNITY»MUSIC"
What is XM Liquid Metal?
XM Liquid Metal is a low-viscosity metal-based material that has undergone special refinement and molding processes to create a highly malleable and shapeable metal. This type of metal can be used for everything from forming welding joints to creating specialized 3D models. It's strong yet flexible, making it ideal for use in a variety of industrial applications.
What are the benefits of using XM Liquid Metal?
XM liquid metal offers many advantages over traditional metals. It can be molded and shaped into intricate and complex shapes with precision accuracy due to its low viscosity, while also being easier to handle than traditional metals. In addition, it is more resistant to corrosion, allows for higher levels of strength, and has superior heat dissipation qualities. These properties make it an ideal choice for various manufacturing processes or custom fabrication projects.
What is the difference between XM Liquid Metal and traditional metal?
The main difference between XM Liquid Metal and traditional metal lies in their physical forms. Traditional metals are typically solid pieces which have been formed into particular shapes, whereas liquid metal has been processed to make it highly malleable and shapeable through special refinements such as molding or welding processes. Additionally, liquid metal usually offers higher thermal resistance compared to solid metals because of its molecular structure which aids better heat transfer through melting and re-solidifying any part when cooled down again.
What types of applications can utilize XM Liquid Metal?
XM liquid metal is commonly used in applications that require complex 3D printing models or customized designs including automotive parts, aerospace components, medical implants or industrial tools; Among other applications, it can be used for soldering joints as well as surface coating on tools or machine parts due to its high refractoriness (heat resistance). Finally, since it eliminates the need for stress relieving steps during production process –such as heat treatment– time savings are often seen when utilizing this type of technology instead of traditional techniques.
Is there any difference in working with liquid metal compared to traditional metals?
Yes; Since its molecular structure allows better heat transmission features -referring better flow properties- there may be several differences when working with liquid metal compared with conventional solid metals suchmetal as steel or aluminum alloys. On one hand; at higher temperatures MC’s melting point might not require an additional external heat source allowing greater time saving during process times while ensuring maximum precision during modeling tasks such us 3D printing jobs; On the other hand fluidity characteristics -due to lower viscosity than regular elements- promotes reduced noise emission while increasing overall strength values regardless deformation factors up to a certain temperature threshold.
How does liquid metal perform under stress conditions?
Generally speaking, due to its lower viscosity than regular elements along with enhanced strength attributes –up until certain temperature thresholds above melting point– liquid metales have been seen improving performance under stressed conditions compared with regular ones enhancing overall product life cycles while dramatically reducing failure risks related either wear out/corrosion issues.
Does liquid metal require special storage conditions?
Yes; To ensure long lasting usage life spanning stored material should always be kept at room temperature far away from direct sunlight exposure preventing negative interaction either contamination sources materials where smoke /fumes may react upon the individual components possibly affecting durability performance build ups over time.
Can I customize my product using XM Liquid Metal?
Yes; With modern CNC machines suited only for this purpose ; Molded artworks such as swords knifes craftsmanship pieces upholstery detailing railings ammo cans among others following desired blue prints may be safely obtained within short lead times span overall satisfying customer needs right out de box fostering good relations regarding repeat business contracts accordingly.
Final Words:
XM Liquid Metal is a versatile alloy that offers a wide array of benefits over traditional materials such as enhanced strength and wear properties along with improved ductility and corrosion resistance while also being safe for use in various industries due to its non-toxic composition. As such, this alloy has become popular among engineers seeking innovative solutions to difficult design problems related to heavy-duty components or parts that must withstand extreme environmental conditions but still remain lightweight enough for easy transport or manipulation by workers onsite or away from the workplace. Despite having been around for nearly four decades now – XMLM continues to perform well in a host of modern applications thanks largely in part to its unique chemical composition which allows it stand out amongst the rest when seeking unparalleled performance from your next project’s components.