What does WFE mean in ELECTRONICS
WFE, or Wafer Fabrication Equipment, pertains to the tools and equipment that are necessary for the manufacturing of wafers in the semiconductor industry. It includes various machines and their components, as well as their function in the process of making semiconductors. This article will discuss in detail what WFE means and its importance in the fabrication of wafers.
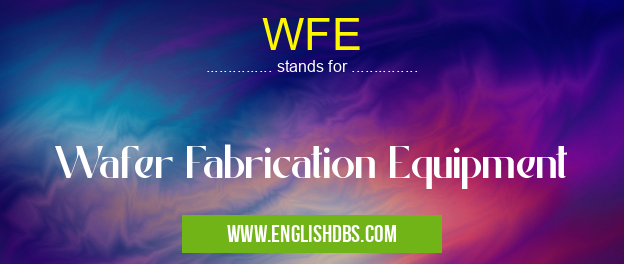
WFE meaning in Electronics in Academic & Science
WFE mostly used in an acronym Electronics in Category Academic & Science that means Wafer Fabrication Equipment
Shorthand: WFE,
Full Form: Wafer Fabrication Equipment
For more information of "Wafer Fabrication Equipment", see the section below.
Definition
WFE stands for Wafer Fabrication Equipment. It is a term used to refer to the machinery and equipment needed for manufacturing wafers used in semiconductors. The equipment mentioned here typically includes lithography systems, electroplating systems, diffusion furnaces, ion implantation systems, metrology systems, and other such technologies which are essential components of any successful process of making semiconductor devices.
Applications
The applications of WFE are vast and far reaching. Wafer fabrication plays an integral role in the development of modern-day electronics. Without this vital step in production, many consumer devices would simply not exist as we know them today – from computers to smartphones to gaming consoles and more all use wafer fabrication during their assembly processes. Additionally, as technology advances at a rapid rate, newer generations of WFE come out on the market each year that help to increase yield and reduce failure rate while producing working products faster than ever before.
Advantages
The advantages associated with using wafer fabrication equipment are numerous. Not only do they provide a more efficient way of producing high-quality products quickly but they also tend to save money on energy costs by consuming less power. In addition to this environmental benefit, manufacturers also enjoy greater yields thanks to increased technological advancements in the area of WFE that allow for higher accuracy when processing various materials used during production – which translates into higher quality output with fewer defects. Finally, these machines often require lesser manpower compared to traditional methods which can lead to a reduction in labor costs as well.
Essential Questions and Answers on Wafer Fabrication Equipment in "SCIENCE»ELECTRONICS"
What does WFE stand for?
WFE stands for Wafer Fabrication Equipment.
What is the purpose of using wafer fabrication equipment?
Wafer fabrication equipment is used to manufacture microscopic electronic components, such as microprocessors, memory chips, and other integrated circuits (ICs). The primary goal of wafer fabrication is to achieve high yield and precise control over production tolerances while maintaining cost-effectiveness.
What type of materials are used in wafer fabrication?
Typically, wafer fabrication requires a variety of materials such as silicon wafers, photoresist polymers, etching chemicals, deposition gases and other dielectric films used in Integrated Circuit (IC) manufacturing processes.
Are all semiconductor products manufactured with the same process?
No. Semiconductor products can be manufactured by either a combination of processes or just one process depending on the complexity of the product’s design and required production rate.
How do different types of ICs affect the types of processing required to fabricate them?
Depending on the desired IC product, there may be more than one type of processing needed. For example, some ICs require deposition processes that add various layers while still others may need etching techniques to remove material from certain areas and add features or components to others. There may also be additional steps involving lithography or photolithography depending on the complexity of the IC design and end result desired.
What are some common tools used in wafer fabrication?
Common tools used in wafer fabrication include exposure systems which use light sources or electron beams for lithography; oxidation furnaces; diffusion ovens; chemical vapor deposition; chemical-mechanical polishing (CMP); spin coaters; dry/wet microscopes; scanning electron microscopes; sputter systems, plasma etch systems; inspection instruments etc.
How long does it take to complete a wafer fabrication cycle?
The length of time for a single cycle depends on many factors but typically ranges from days to weeks depending on the complexity off each step involved and total number steps in the cycle.
What safety precautions should be taken when working with hazardous materials during wafer fabrication?
Safety must remain paramount when working with hazardous materials during wafer fabrication processes. It is essential that all personnel understand and follow safety protocols including wearing personal protective equipment (PPE) such as gloves, masks, eye protection etc., following MSDS guidelines regarding potential health risks associated with specific chemicals being handled and proper ventilation within any space where hazardous chemicals are being processed or stored. Additionally,, it is important that any safety signs or caution notices posted at worksites be observed throughout all stages off any process activity.
What measures should be taken when dealing with widely varying temperatures during a process flow?
Thermal management is key when dealing with extreme temperature differences over short periods of time during a process flow given that some processes may require heating up above 300℃ whereas others will require cooling down below -80℃ without ever reaching room temperature between cycles – this can cause major damage both to machinery parts as well as personnel on site if not properly managed beforehand through efficient temperature control systems.
Final Words:
In conclusion, Wafer Fabrication Equipment (WFE) is an important part of many facets within the electronics industry today. It has revolutionized production by providing faster yields with better quality output while simultaneously lowering energy consumption and labor costs for manufacturers across all industries – leaving customers with more reliable end-products than ever before! With new advances being made every day it’s no wonder why this piece of technology is still so popular even after decades since its inception.