What does VAVE mean in ENGINEERING
VAVE (Value Added Value Engineering) is a holistic approach to improving product or process performance, cost and quality. It is a systematic method of optimizing existing products through the identification and elimination of non-value-added activities and the development of processes that improve the overall customer experience and profitability. The goal of VAVE is to increase efficiency while reducing costs, enabling continued growth in an increasingly competitive market.
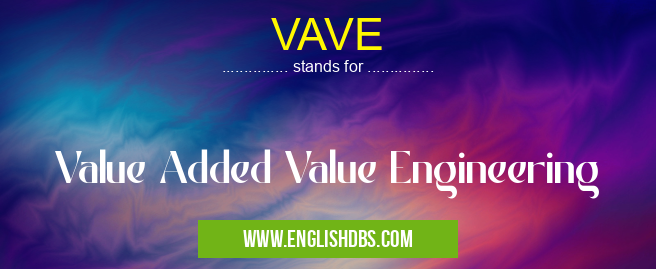
VAVE meaning in Engineering in Academic & Science
VAVE mostly used in an acronym Engineering in Category Academic & Science that means Value Added Value Engineering
Shorthand: VAVE,
Full Form: Value Added Value Engineering
For more information of "Value Added Value Engineering", see the section below.
Benefits Of VAVE
The implementation of this methodology has many benefits for organizations looking to provide better products or services while controlling costs. Firstly it allows companies to identify areas where they may have an inefficient process which adds extra time onto delivery cycles such as manufacturing defects or lack of properly trained staff members leading too longer lead times for orders placed by customers. By identifying these inefficiencies businesses can work on quickly addressing them with minimal disruption resulting in shorter delivery windows leading not only improved customer satisfaction but also reducing additional costs associated with lengthy delays. Additionally because manufacturers are able to identify areas where there are no value added activities taking place they can use this information as leverage when negotiating prices with suppliers allowing them greater control over their profits margins and operating expenses.
Essential Questions and Answers on Value Added Value Engineering in "SCIENCE»ENGINEERING"
What is Value Added Value Engineering (VAVE)?
Value Added Value Engineering (VAVE) is a business process that adds value to a product, service or procedure in order to improve customer satisfaction and maximize profits. It involves identifying the value stream — the stages within a process where value can be added — and reviewing each stage of the product life cycle systematically with the aim of cutting costs, eliminating waste and improving overall quality.
How does VAVE fit into Lean Six Sigma methodology?
Value Added Value Engineering (VAVE) is one of the key components in Lean Six Sigma methodology. The aim of VAVE is to improve efficiency and reduce costs through the application of analytical tools such as Process Mapping, Cost Analysis and Design for Manufacture. VAVE encourages teams to look at both current processes and future possible improvement opportunities so that they are incorporated into designs as early as possible.
What are the benefits of using VAVE?
There are many potential benefits of using VAVE including cost savings, improved customer satisfaction, time savings, improved process performance, reduced lead times and increased sales volumes. By applying lean principles to existing processes or improving upon new products or services before launch, organizations can reduce their operational costs while increasing quality.
How long does it take to implement VAVE?
The amount of time needed for implementing VAVE depends on several factors such as the scope of the project, size of organization/team involved and level of complexity associated with it. Generally speaking however, an effective implementation process could take from two weeks up to three months or more depending on what needs to be achieved within that timeframe.
Who should be involved in the implementation process?
Implementation teams for successful projects should involve members from different departments with various skill sets. This could include senior management executives, product designers/engineers, production team members or supply chain personnel – all who have an understanding on how value is created throughout their respective areas in order for them to identify different opportunities for improvement.
How do you measure success when it comes to using VAVE?
Successful measurement requires having established objectives prior to implementing any processes related to VAVE; these objectives should then be tracked throughout its implementation in order for progress towards achieving these goals and objectives can be monitored accordingly. In addition metrics related directly relevant metrics such as time savings, cost savings etc… should also be tracked against set targets in order understand if desired results have been achieved or not.
What software is most widely used when it comes to implementing a successful VAVE process?
There are a variety of commercially available software packages which are used by companies when embarking on projects related to Value Added Value Engineering (VAVE). Some examples would include Minitab for statistical analysis; Arena simulation software; or Microsoft Project Manager for managing project deliverables & timeline; among others depending on individual needs and preferences.
How important is training during implementation?
Training is essential when it comes down to properly implementing any type of project involving Value Added Value Engineering (VAVE). Not only will it help teams better understand how each component works together but also ensure that best practices such as Lean Six Sigma principles are being followed correctly from beginning until completion.
Are there any industry standards organizations use when applying VAVE concepts?
Yes - Typically organizations that utilize lean manufacturing approaches adopt standards from organizations such as ASQ (American Society for Quality) – among other bodies which recognize professional competencies within certain areas such as manufacturing engineering & design fundamentals.
Final Words:
VAVE (Value Added Value Engineering) provides organizations with an effective way optimize existing products/services without significant disruption by focusing on identifying non-value activities that take up unnecessary time/costs while providing opportunities for creative solutions that yield better results than before from both an operational/customer satisfaction standpoint giving companies leverage when competing within industries against larger rivals.