What does TQCS mean in GENERAL
Total Quality Control Strategies (TQCS) refer to a set of best practices and techniques used by businesses to ensure the quality of their products and services. TQCS focus on a continuous improvement approach which can guarantee the achievement of top-level quality standards throughout the organization. It involves all aspects of business operations, such as product design and development, process management, customer service, etc. In addition, TQCS also covers many other related areas like human resources management, supply chain management and organizational culture.
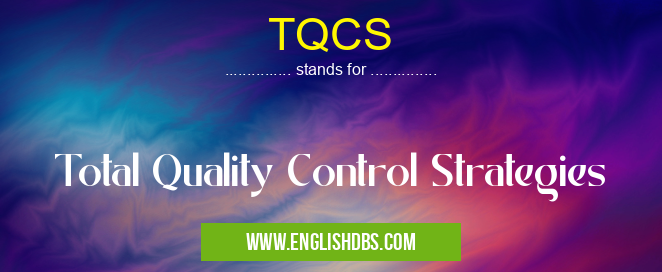
TQCS meaning in General in Business
TQCS mostly used in an acronym General in Category Business that means Total Quality Control Strategies
Shorthand: TQCS,
Full Form: Total Quality Control Strategies
For more information of "Total Quality Control Strategies", see the section below.
Meaning in Business
In today’s competitive business environment, it is imperative for companies to maintain high quality standards in order to stay ahead of their competitors. In this regard, Total Quality Control Strategies provide organizations with an effective framework for managing the different aspects related toquality assurance. This framework encompasses various techniques such as benchmarking processes, root cause analysis, statistical process control (SPC), continual improvement initiatives, etc., so as to ensure that any potential defect or issue can be identified quickly and remedy taken immediately before it affects end user experience adversely.
Essential Questions and Answers on Total Quality Control Strategies in "BUSINESS»GENERALBUS"
What is Total Quality Control?
Total quality control (TQC) is a management approach that seeks to improve the quality of products and services by carefully monitoring all aspects of production. It is based on the principle that “quality can only be assured if each step in the production process is well managed”. With this approach, organizations strive to make sure that their processes lead to consistent high-quality results.
What are the major principles of TQC?
The major principles of TQC are continuous improvement, customer satisfaction, preventive action, teamwork, and total employee involvement. These principles are designed to ensure that quality assurance takes place at every level and in every stage of production. By actively applying these principles in an organization’s day-to-day operations, companies can ensure consistent high-quality performance from its products and services.
What are some elements of total quality control?
Some elements of total quality control include inspection throughout the entire manufacturing process, managing for prevention rather than detection, implementing a process plan or system in order to eliminate variation between processes, reducing setup times between processes, controlling nonconforming materials and disposing or reworking them as needed, measuring customer satisfaction levels with surveys or polls, and striving for continual improvement through lessons learned.
How does TQC help companies improve their products or services?
By implementing TQC strategies such as continuous improvement across all levels of production and involving everyone in the organization in improving the overall system, companies can significantly reduce variation which leads to improved product or service features. This reduces costs associated with scrap and rework while also increasing customer satisfaction by ensuring higher quality standards.
What roles do employees play in total quality control?
Employees play a very important role in TQC as they are responsible for performing inspection throughout different stages of production as well as monitoring customer feedback which provides valuable insights into improving overall quality goals. Employees must also take ownership when it comes to preventing nonconformities rather than just detecting them after they have occurred. Finally they must be involved in setting total quality objectives within their departments and striving for continuous improvement on a regular basis.
How do you measure efficiency in total quality control?
Efficiency is typically measured through metrics such as cycle time reduction per operation, reduction in downtime related activities such as set up times or maintenance activities; average cost per unit produced; percentage defect rate; number of defects detected compared to those not detected; number of customer complaints received; time taken from one process step to another; output rate comparison over similar shifts/days; etc.
Is there any software used for Total Quality Control?
Yes – there are many software programs available on the market today that can help organizations effectively manage their total quality assurance efforts more efficiently including tracking performance metrics over time. Some popular examples include IQS Software (Integrated Quality Solutions), RAMAS Software Solutions (Real Time Assessment Systems Approach), Chetu Business Intelligence Suite (Business Analytics Software), QPR QualityPlus (Cloud-based Quality Management System) among others.
What procedures should be put into place when creating a Total Quality Management system?
When creating a Total Quality Management system there should be procedures put into place such as developing standard operational procedures; auditing specific departments or processes on a regular basis; implementing corrective action plans whenever necessary; creating periodic reports tracking key performance indicators related to product or service levels like yield rates or defect rates over time; training staff members on any new processes introduced within an organization.
Is statistical analysis used when implementing Total Quality Control Strategies?
Yes – statistical analysis plays an important role when implementing TQCS since it allows managers to accurately measure their performances against goals set by recognizing patterns over time which helps identify areas where improvements need to be made. Statistical tools like data sampling techniques allow managers to draw meaningful conclusions about their systems from smaller datasets so they can target areas that need more attention.
How often should organizations evaluate their current Total Quality Control strategies?
Organizations should regularly review their current TQCS at least once every quarter so they can assess whether any changes need to be made based on internal reviews or customer feedback received during this period. Regular assessments will also enable companies to identify areas where improvement needs to occur before potential problems arise.
Final Words:
Total Quality Control Strategies are essential if companies want to stay ahead in the competitive marketplace. By emphasizing on rigorous controls over every stage of production cycle from raw material acquisition till delivery of finished products/services – businesses can not only reap higher profitability but also gain trust & confidence among their customers with superior quality offerings at all times.