What does TPV mean in ELECTRONICS
TPV stands for Thermo-Plastic Versalloy, a versatile and common type of engineering plastic. It is a polymer material composed of thermoplastic resins and various fillers that act as reinforcements or modifiers. TPV materials are widely used in the automotive industry due to their superior physical properties, durability, and excellent resistance to chemicals and temperature changes. They are also ideal in harsh environments such as outdoor applications due to their resistance to UV radiation, moisture, and environmental pollution. This makes TPV an ideal material for many automotive components such as weather stripping, hoses, body panels, bumpers, and more.
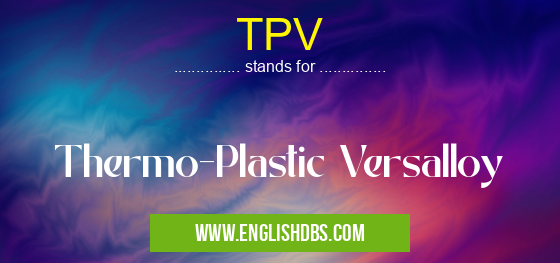
TPV meaning in Electronics in Academic & Science
TPV mostly used in an acronym Electronics in Category Academic & Science that means Thermo-Plastic Versalloy
Shorthand: TPV,
Full Form: Thermo-Plastic Versalloy
For more information of "Thermo-Plastic Versalloy", see the section below.
Properties & Advantages Of Using TPV
TPV materials offer numerous advantages over other types of engineering plastics such as increased strength and flexibility with minimal weight increase. The use of thermoplastic elastomers increases the elongation at break by up to 200%. Additionally, TPV materials have good abrasion resistance which make them perfect for areas exposed to high levels of wear and tear like door jams or car bumpers. TPV also has low thermal conductivity which makes it an excellent choice for insulating electrical cables and wires or other components subject to extreme temperatures or exposure to hot engine parts. The plastic is also resistant against chemical damage from coolants, oils, fuels etc., making it perfect for automotive fuel systems or powertrain components that need protection from corrosive liquids. Lastly, TPV's versatility allows it to be processed with traditional injection molding techniques at relatively low temperatures which can further reduce production costs compared with other thermoplastics such as ABS or TPEs (thermoplastic elastomers).
Essential Questions and Answers on Thermo-Plastic Versalloy in "SCIENCE»ELECTRONICS"
What is TPV?
TPV stands for Thermo-Plastic Versalloy, which is a type of thermoplastic elastomer made through a cross-linking process. It is a rubber-like material commonly used in engineering and automotive applications due to its superior durability and resilience.
What qualities make TPV a desirable material?
TPV is a popular choice because it has excellent heat and chemical resistance, low compression set, high tensile strength, great dimensional stability, superior flame resistance, low smoke emission and good weatherability. Additionally, it can be processed relatively easily using conventional processing techniques.
What types of applications are suitable for TPV?
TPV provides an ideal solution for automotive components such as engine gaskets, suspension systems and exhaust systems; industrial rubber products such as hoses and seals; electrical cable insulation; consumer products such as garden tools; and various applications regarding construction materials.
How does one differentiate between different types of TPV?
The different types of TPVs can be differentiated by their Shore A hardness ratings. The Shore A scale measures the hardness of polymers on a scale from 0 to 100 with soft polymers rating at 0 while harder polymers rate towards the upper end of this scale.
Is there any difference between thermoplastic rubber (TPR) and thermo-plastic versalloy (TPV)?
Yes, there are several distinct differences between TPR and TPV. TPRs are generally softer than their thermo-plastic counterparts so they're better suited for flexible seals or gaskets due to their flexibility. They also possess higher mold shrinkage rates which can cause potential problems when working with precision components. On the other hand, thermoset plastics like TPVs offer more rigidity but have lower mold shrinkage rates making them ideal for structural parts like mountings or housings that require high accuracy and stability
Can I weld/glue PPVs together?
Generally speaking no - welding/gluing would not be an effective joining technique for PPVs since these materials cannot be melted down once they have been processed into shape due to their thermosetting nature. An alternative option would be mechanical fastening methods such as screws bolts etc., or adhesives designed specifically meant for bonding two PPVs together will provide better results.
Does PTI design/produce custom moulded parts made from TPV?
Yes we do! Our team specializes in designing and manufacturing custom molded parts made from both thermoplastic rubbers (TPR) as well as Thermo-Plastic Versalloys (TPVs). We use a range of technologies including injection moulding, rotational moulding and 3D printing depending on our customer’s needs in order to produce quality parts perfectly suited for their application requirements..
Are there any specific safety protocols I need to follow when handling/working with TPSs?
As with any potentially hazardous materials proper precautions should always be taken when working around them regardless whether you’re handling raw compounds or finished products made from any plastic substance—including Thermo Plastic Versalloys (TPVs). Safety goggles should always be worn along with gloves whenever dealing directly with these materials.
Final Words:
In conclusion, TPV stands for Thermo-Plastic Versalloy which is a versatile engineering plastic widely used in the automotive industry due to its superior physical properties, durability and excellent resistance against chemicals and temperature changes. It is also lightweight yet strong with good abrasion resistance making it perfect for parts exposed to wear while offering excellent insulation qualities from electrical cables/wires or hot engine parts that could otherwise be damaged by thermal conductivity or corrosion caused by chemical liquids. Taking all these characteristics into account along with its low production cost associated with traditional injection molding techniques makes TPV an ideal choice when considering what material should be used during the design process of any automotive component.