What does THT mean in ELECTRONICS
Through Hole Technology (THT) is an electronic assembly process that involves mounting and soldering components to printed circuit boards (PCBs). It is one of the oldest and most reliable types of surface mount technology, meaning that it has a proven history of reliability, accuracy, and repeatability in manufacturing. THT is a crucial component in today's electronic industry because it allows for incredibly complex circuit boards to be built with precision and minimal effort.
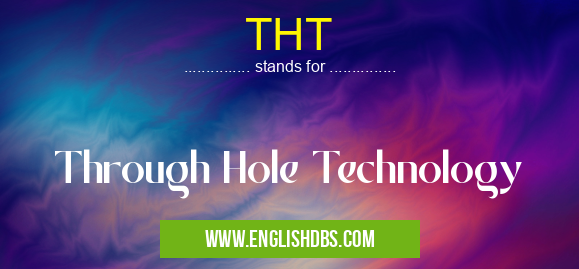
THT meaning in Electronics in Academic & Science
THT mostly used in an acronym Electronics in Category Academic & Science that means Through Hole Technology
Shorthand: THT,
Full Form: Through Hole Technology
For more information of "Through Hole Technology", see the section below.
Description
THT involves drilling holes through printed circuit board layers for component leads to be inserted into in order to create complete electrical connections. This creates an electrical ‘bridge' between components and the PCB layers, allowing electrical signals to flow freely from one component to another as intended. In addition to these fixed components, some THT designs also include mechanical elements such as nuts or brackets for additional support or strain relief. Once the required components have been inserted into their appropriate holes and correctly aligned, soldering can then be employed to ensure strong physical and electrical bonds are formed between each component lead and the PCB layer pads. A flux-core solder paste is usually applied to each joint prior to any soldering being carried out.
Advantages
One of the main advantages of using through hole technology when compared with other types of SMT assembly is that components using this method are easy to install on the circuit board surface with minimal effort due to their precise construction. As well as this, THT offers higher current ratings than most SMT processes due to its stronger soldered joints which improve heat dissipation properties. This makes it particularly useful for manufacturing power supplies or other high-current applications where precise energy distribution is essential for long lasting performance. Moreover, Through Hole Technology usually results in smaller product footprints — meaning that more circuitry can fit into a smaller space without risking product integrity or performance quality.
Disadvantages
The main disadvantage associated with using Through Hole Technology is that it generally takes longer than other SMT processes such as surface mount assembly or pick-and-place technologies due to its labour intensive nature; drilling all those holes by hand will take quite a while! Additionally, although certain components manufactured via THT are able survive extreme temperatures better than conventional SMT processes due its superior heat dissipation qualities, this process can still require added cooling techniques if products need maximum temperature stability for extended periods of time.
Essential Questions and Answers on Through Hole Technology in "SCIENCE»ELECTRONICS"
What is Through Hole Technology?
Through Hole Technology (THT) is an electronic assembly process in which electrical components are placed into holes drilled into printed circuit boards (PCBs) and soldered to create a permanent connection. The components are soldered to the PCB by inserting their leads through the drilled holes in the board and melting solder onto them.
What is the primary benefit of Through Hole Technology?
The primary benefit of Through Hole Technology is that it provides a robust, reliable connection that is able to withstand vibration and other potentially destructive forces. Additionally, it can easily be used for larger components that require more space than SMT technology allows.
How does through hole technology differ from surface mount technology (SMT)?
The main difference between through hole technology (THT) and surface mount technology (SMT) lies in how they attach to the printed circuit board (PCB). While SMT requires components to be attached directly on top of a PCB's surface, THT requires that components be inserted through holes drilled in the board and then soldered on the underside.
Are there any disadvantages associated with using through hole technology?
One potential disadvantage of using through hole technology over surface mount technology is that it requires more complex drilling techniques and higher levels of precision when placing components onto a PCB. Furthermore, due to its requirement for physical space, THT is not as suitable for very dense designs where component count must be kept low.
What type of components are typically used with Through Hole Technology?
Generally speaking, larger components such as resistors, capacitors, connectors, switches and potentiometers are usually attached using through hole technology due to their size and weight. Smaller parts such as integrated circuits or transistors may also use this method if necessary.
Is automated placement possible with Through Hole Technology?
Automated placement systems are capable of placing simple THT components such as resistors or capacitors onto a PCB without human intervention, but other parts require manual insertion due to their shape or size.
Does Through Hole Technology require specialized equipment?
Yes — drilling machines capable of precise placement as well as soldering tools are required for efficient production when using through hole technology.
How long does it take for a part to be assembled using Through-Hole Technology?
It depends on several factors such as component type, lead geometry, and number of solder joints but typically speaking assembly times range from 5-10 seconds per part.
Final Words:
Through Hole Technology is an tried-and-tested method of assembling various different types of electronic components onto printed circuit boards used in today's market - enabling manufacturers and designers alike achieve extraordinary levels accuracy during production with relative ease. Although some drawbacks exist in terms of higher production times compared with other SMT techniques like surface mount assembly, THT offers greater design flexibility making it suitable for many applications across multiple industries including medical, defence & aerospace amongst others whose success lies within accurate and reliable circuitry builds.
THT also stands for: |
|
All stands for THT |