What does THR mean in UNCLASSIFIED
Through hole reflow is a process used for assembling surface mount technology (SMT) components onto printed circuit boards (PCBs). It involves placing components onto the top side of the board and then running them through a reflow oven which melts solder paste deposited onto the boards, allowing the parts to be securely soldered in place. This process is often preferred over other methods such as wave soldering due to its high accuracy and repeatability, resulting in better quality products.
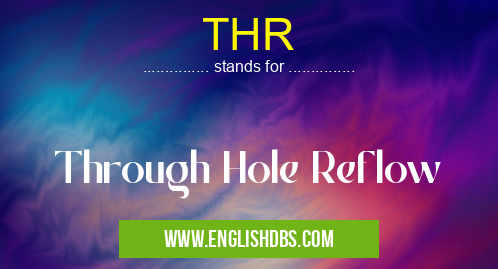
THR meaning in Unclassified in Miscellaneous
THR mostly used in an acronym Unclassified in Category Miscellaneous that means Through Hole Reflow
Shorthand: THR,
Full Form: Through Hole Reflow
For more information of "Through Hole Reflow", see the section below.
Meaning
THR stands for Through Hole Reflow and is a method used in Electronic Manufacturing Services (EMS) to assemble surface mount technology components on printed circuit boards. This process uses heat to melt solder paste that has been applied to the board’s surface, allowing components to be securely attached. Heat is provided by an oven which regulates temperature precisely in order to achieve consistent results with minimal defects.
Process
The THR process begins with operators hand-placing components onto the top side of the board, after ensuring all necessary component pads have paste deposits on them. Then, the populated PCBs are placed into trays and loaded into an oven preheated to a specific temperature according to design specifications. During this stage, temperatures can range from 170°C - 240°C depending on type of component and size of soldering pad area. After reaching peak temperature, it takes several minutes for sufficient heat energy transfer for proper melting of solder paste. Once complete, an operator removes each tray one at a time before quickly cooling them down using forced air cooling or water immersion bath systems depending on company policy or requirements set by industry regulations.
Advantages
The THR process offers many advantages over traditional wave soldering methods due its improved accuracy and repeatability; making it well suited for producing high-density PCB assemblies commonly produced now days in consumer products such as smartphones and tablets computers. It also offers greater control on parts placement by allowing manual adjustments during initial loading stages compared to automated processes such as screen printing; which require correct positioning from start up lest repeated setup is needed later down production line resulting in loss of productivity times. In addition, modern reflow ovens offer great flexibility with heating profiles capable of accommodating even most sensitive electronics currently available today without any risk of damage due fatrlless temperatures ramps up or down throughout entire cycle; thus ensuring perfect connections every time end product leaves factory premises with no need for reworking afterwards.
Essential Questions and Answers on Through Hole Reflow in "MISCELLANEOUS»UNFILED"
What is Through Hole Reflow?
Through Hole Reflow is a technique used to attach components to printed circuit boards. It involves melting pre-tinned leads using Infrared or convection heating technology. The result is a reliable, long-term connection that has the same electrical characteristics as soldered connections.
Are there any advantages of Through Hole Reflow?
Yes. Through Hole Reflow provides several advantages over conventional soldering. It eliminates the need for manual soldering which results in more consistent performance and increased productivity. Additionally, it requires less time, use fewer chemicals, and produces less waste than traditional soldering techniques.
How does Through Hole Reflow work?
Through Hole Reflow utilizes heat to transfer solder from the component leads to the printed circuit board pads. A reflow oven is typically used to control the temperature profile and the rate of cooling with various settings for different types of components and materials.
Is Through Hole Reflow difficult?
No, through hole reflow does not require large amounts of skill or experience - instead it relies on setting specific temperatures according to recommended profiles for each type of component being used in order to achieve a successful outcome.
Does Through Hole Reflow require any specialized equipment?
Yes - in order to perform through hole reflow properly, an infrared (IR) or convection oven must be used along with other proper tools such as flux and solder paste applicators, tweezers and temperature probes/thermocouples so that the process can be monitored and adjusted if necessary.
Is there anything I should avoid when performing Through Hole Reflow?
Yes - it’s important to avoid overheating components as this can create expansion issues and cause them to break free from their pad during cooling resulting in unreliable connections or even complete failure of the board assembly. Additionally, high humidity levels should also be avoided as they can lead to condensation occurring on surfaces which results in shorts between adjacent circuits.
How does quality assurance relate to Through Hole Reflo w?
Quality assurance plays an important role in ensuring that all boards assembled via through hole reflow are electrically sound before they are shipped out from a facility. This includes inspecting all parts prior to assembly, verifying solder deposition, ensuring acceptable thermal profile was achieved during reflow process and checking for any potential defects such as opens or shorts.
What kind of maintenance do I need do on my IR oven?
To ensure optimal performance of your IR oven during through hole reflow operations regular maintenance checks should be made at intervals suggested by its manufacturer including replacing filters, wiping down reflective surfaces inside the chamber etc..
Final Words:
In conclusion, THR or Through Hole Reflow is essential process used extensively nowadays EMS companies worldwide producing complex electronic devices small enough fit your pockets within matter seconds thanks its ability ensure accurate placement each individual component every single time with minimal thermal shock damage possibility compared other traditional methods like wave soldering used past decades but not suitable certain modern types hardware being developed current age rapid technological advancements taking place almost daily base.
THR also stands for: |
|
All stands for THR |