What does SQM mean in GENERAL
Supplier Quality Management (SQM) is a process used by organizations to ensure the highest degree of quality in its products and services by managing and assessing the performance of their suppliers. This management system not only controls the quality of products acquired from suppliers, but also makes sure that all suppliers comply with safety standards and regulations. SQM ensures that organizations receive only products and services that meet their high-quality standards.
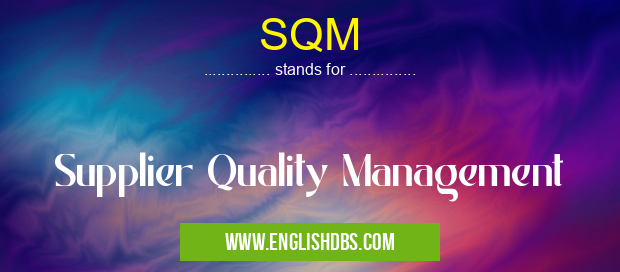
SQM meaning in General in Business
SQM mostly used in an acronym General in Category Business that means Supplier Quality Management
Shorthand: SQM,
Full Form: Supplier Quality Management
For more information of "Supplier Quality Management", see the section below.
Definition
SQM stands for Supplier Quality Management, which is a strategic tool used by organizations to maintain the highest level of quality in their products and services. It involves an organization's assessment of both current supplier performance as well as potential suppliers' ability to meet customer needs. SQM enables organizations to measure, monitor, and improve supplier quality over time. Through this process, organizations can reduce costs associated with defective parts or materials while improving customer satisfaction.
Benefits
The main advantage of using SQM is that it helps organizations maintain high-quality standards across all aspects of production processes. Organizations can assess supplier performance on individual basis instead of relying on industry averages or standard metrics like cost per unit or delivery times awarded by customers or external agencies. SQM also offers greater control in evaluating supplier performance and reducing expenses associated with defective materials or faulty parts that may lead to product recalls or other problems down the line. In addition, SQM helps reduce costs associated with poor quality due to higher reliability, fewer rejects, improved productivity, and a decrease in waste generated from producing low-quality items.
Essential Questions and Answers on Supplier Quality Management in "BUSINESS»GENERALBUS"
What is Supplier Quality Management?
Supplier Quality Management (SQM) is a systematic process for ensuring that the goods and services received from suppliers meet the required industry quality standards. It also involves monitoring supplier performance to ensure on-time and satisfactory delivery of goods.
What are the benefits of Supplier Quality Management?
SQM helps ensure better product quality, safety and compliance to standards, reduced cost, improved supply chain efficiency, better customer experience, and improved supplier relationships.
How can I improve my supplier quality management system?
You can improve your SQM system by implementing preventive measures such as regular training for staff, automated processes to monitor supplier performance, auditing suppliers’ practices regularly, and making sure to effectively communicate expectations with suppliers.
What are the steps involved in SQM?
The typical steps involved in SQM include risk assessment, selection of suppliers/contractors, contract review and negotiation, QC inspection & testing of incoming materials/products, ongoing monitoring & auditing of suppliers’ performance, corrective action when necessary and continous improvement activities.
What type of information should I store in my SQM system?
Your SQM system should store all relevant information about your suppliers such as contact details; service history; quality records including audits; incident reports; performance data; certificates of conformity or other documents confirming compliance; scope of work/ agreement details etc.
What tools can be used for managing supplier quality?
Some common tools used for managing supplier quality include Quality Management Systems (QMS), Enterprise Resource Planning (ERP) systems or “supply chain platforms” such as Ariba or Oracle Supply Chain Cloud Platforms. They allow users to track orders, manage inventory levels and access real-time analytics.
How often should I audit my suppliers?
The frequency of audits will depend on several variables such as products/services you receive from the supplier(s), their industry regulations & guidelines as well as internal policies & procedures. However it is generally advisable to perform an audit at least once every 12 months for most organisations.
How can I determine whether a potential supplier meets my requirements?
To ensure that the potential supplier meets your requirements it is important to thoroughly review all relevant documents related to their products or services such as MSDS (material safety data sheet), customer satisfaction surveys etc., Visit them physically if possible and conduct an audit if appropriate.
Final Words:
In short, Supplier Quality Management (SQM) is an essential part of any organization's strategy for achieving top-notch product and service excellence over time. By leveraging SQM’s methodologies for assessing supplier performance, organizations can significantly reduce costs associated with defective parts and materials while increasing customer satisfaction levels at the same time. Additionally, using SQM tools can help safeguard against product recall risks which would otherwise have serious financial implications for businesses. All in all, SQM is vital for any organization looking to become more efficient while maintaining high standards in terms of product manufacturing quality control and assurance processes.