What does SPRCS mean in ACADEMIC & SCIENCE
SPRCS stands for Singularly Perturbed Relay Control Systems. This type of system is designed to provide feedback into a process control loop, making it possible to modify the behavior of the system in response to changing conditions. It is useful in applications such as temperature control, motor speed control, and other automated control systems.
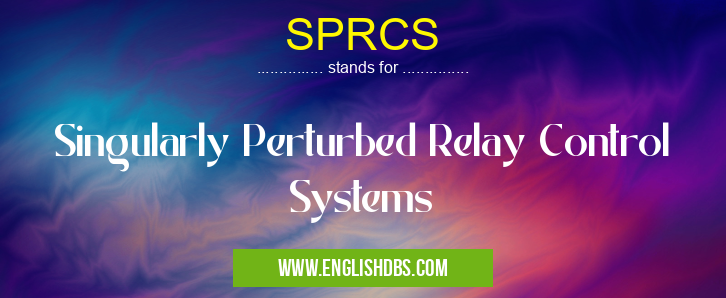
SPRCS meaning in Academic & Science in Academic & Science
SPRCS mostly used in an acronym Academic & Science in Category Academic & Science that means Singularly Perturbed Relay Control Systems
Shorthand: SPRCS,
Full Form: Singularly Perturbed Relay Control Systems
For more information of "Singularly Perturbed Relay Control Systems", see the section below.
Essential Questions and Answers on Singularly Perturbed Relay Control Systems in "SCIENCE»SCIENCE"
What is SPRCS?
SPRCS stands for Singularly Perturbed Relay Control Systems. It is a system designed to provide feedback into a process control loop, allowing for modifications in the system's behavior in response to changes in conditions.
What applications are suitable for an SPRCS?
An SPRCS is commonly utilized for temperature and motor speed control, as well as other automated control systems.
How does an SPRCS improve upon traditional process control loops?
An SPRCS improves upon traditional process control loops by providing extra flexibility and responsiveness, allowing the system to respond quickly and accurately when changes occur during operation.
What are some benefits of using an SPRCS?
Benefits of using an SPRCS include increased accuracy, improved response times, and lower maintenance requirements compared to traditional process control systems.
Are there any drawbacks associated with using an SPRCS?
One drawback of using an SPIECS is that it can be more expensive than traditional process controls due to its complexity. In addition, proper tuning can be difficult if the parameters involved are not properly understood.
Final Words:
Overall, the advantages of an SPIECS outweigh its drawbacks since it offers improved performance in various applications compared to traditional processes controls due to greater flexibility and accuracy when responding to changing conditions. As long as the proper tuning is done correctly and all parameters are understood properly, then this type of system can provide great value while performing at its peak efficiency levels.