What does SPQD mean in DEVELOPMENT
SPQD stands for Supplier Product Quality Development. It focuses on enabling businesses to better understand the quality of their supplier products, and uses that insight to create a roadmap for developing a higher-quality product. This includes identifying areas of improvement, setting goals and objectives, and developing strategies to achieve them. SPQD is essential for organizations looking to stay ahead of the competition and make sure their products are up to industry standards. This comprehensive model can help organizations keep track of supplier performance, identify high-risk areas, and ensure customer satisfaction.
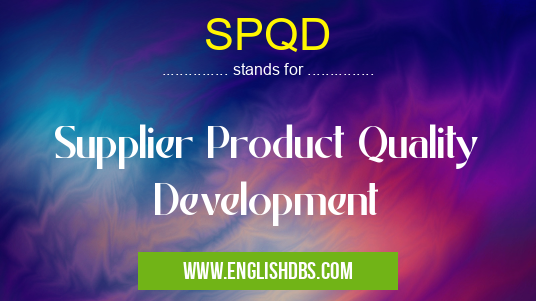
SPQD meaning in Development in Community
SPQD mostly used in an acronym Development in Category Community that means Supplier Product Quality Development
Shorthand: SPQD,
Full Form: Supplier Product Quality Development
For more information of "Supplier Product Quality Development", see the section below.
» Community » Development
What Does SPQD Stand For?
SPQD stands for Supplier Product Quality Development. By examining the quality of a business’s suppliers’ products, this model allows for companies to create a better understanding of what their customers need in order to be satisfied with their purchases. It provides businesses with actionable insights so they can more effectively create a strategy that will improve their own product standards.
How Does SPQD Work?
The SPQD model works by using various measures such as surveys or inspections to evaluate the quality of supplier products. These metrics allow companies to gain an understanding of what needs improvement and work towards achieving these goals by assigning objectives and creating strategies. This system also helps businesses identify potential threats before they occur by keeping track of supplier performance over time.
Benefits Of SPQD
The benefits of implementing SPQD include increased customer satisfaction through improved product quality; cost savings by minimizing waste; strengthened relationships between suppliers due to regular feedback; reduced risk due to better identification of problem areas; increased competitive advantage over other companies due to higher product quality; and improved employee morale due to increased motivation from having attainable goals set out in front of them. Ultimately, these advantages can lead an organization closer towards success.
Essential Questions and Answers on Supplier Product Quality Development in "COMMUNITY»DEVELOPMENT"
What is Supplier Product Quality Development (SPQD)?
SPQD stands for Supplier Product Quality Development. It is a process used to ensure suppliers meet standards of product quality and reliability, while guaranteeing customer satisfaction. It includes activities like supplier audits, sourcing qualified personnel, supplier relations management, and managing design and production processes.
How often should SPQD activities be conducted?
SPQD activities should take place on an ongoing basis to ensure that product quality meets customer expectations. Depending on the industry and type of product or service, this could involve quarterly or biannual reviews, as well as monitoring feedback from customers.
What are some important steps in the SPQD process?
The key steps of the SPQD process include supplier selection/evaluation, implementing performance standards, conducting annual audits/inspections/reviews, developing quality plans with suppliers, monitoring and assessing supplier performance regularly, improving areas of deficiency through corrective action plans or training sessions.
How can organizations benefit from adhering to SPQD guidelines?
Adhering to the principles of Supplier Product Quality Development allows organizations to improve their products in order to achieve higher levels of customer satisfaction and loyalty. Additionally, it helps chain supply operations which leads to cost savings due to better coordination between suppliers and customers alike. Finally, it also maintains safety standards across the organization’s products due to higher-quality components.
What roles do stakeholders play in a successful SPQD program?
Stakeholders such as buyers (procurement officers), owners (executives) end users (customers/clients), suppliers (manufacturers), government agencies (regulators) have an important role to play in a successful implementation of Supplier Product Quality Development Programs by providing support and guidance throughout the process while helping manufacturers identify areas where improvement is needed as well as further training if required.
How is customer feedback incorporated into the Supplies Product Quality Development program?
Customer feedback is crucial component for any Supplies Product Quality Development program since it provides insights into how effective different aspects of development are performing in terms of meeting customer’s expectations with regards to product quality and reliability. Therefore customer feedback should be collected regularly through surveys or questionnaires & properly analyzed before taking corrective action plans accordingly.
What techniques can be used when evaluating a potential supplier?
When evaluating a potential supplier some common techniques include qualitative assessments such as verifying references from previous clients; analyzing pricing structures; examining financial stability; performing background checks; accessing manufacturer certifications; verifying quality control systems; doing onsite inspections; reviewing existing contracts for pricing consistency & inquiring about factory capabilities among other.
How does effective communication help ensure adherence with Supplies Product Quality Development programs?
Effective communication between stakeholders such as buyers/suppliers/endusers at all stages ensures adherence with an effective supplies product quality development program since it gives access to all involved parties over what needs attention & what corrective actions need to be taken immediately in order to keep everything running smoothly & consistently while not compromising on safety standards set out by regulators.
Why is automation beneficial within the SPQD process?
Automation has numerous benefits within the Supplement Product Quality Developments Process such as enabling faster collection & easier analysis of data regarding auditing processes since automated tools provide access over multiple sources at once while reducing wastage generated due human error significantly & trimming down overall costs associated with manual processes.