What does SCADA mean in NETWORKING
SCADA stands for Supervisory Control and Data Acquisition. It is a computer-based system used in industries to monitor and control industrial processes from a remote location. SCADA systems are composed of hardware components like sensors, controllers, communication networks, terminals, as well as software programs. They enable technicians to have access to critical information such as product temperatures, valve positions, motor speeds and other real-time data about industrial processes. SCADA systems provide a reliable way for operators to view the status of their equipments and adjust settings onsite or remotely. They also allow automation of certain tasks with minimal manual intervention while providing improved safety protocols that help reduce risk associated with hazardous operations.
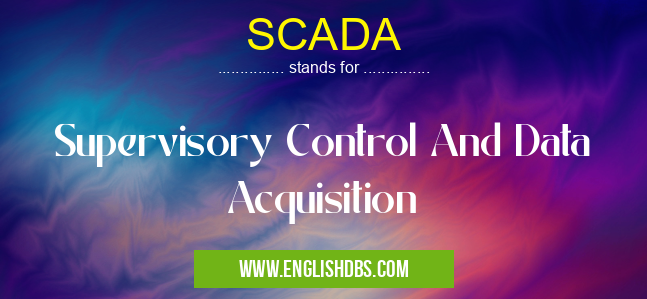
SCADA meaning in Networking in Computing
SCADA mostly used in an acronym Networking in Category Computing that means Supervisory Control And Data Acquisition
Shorthand: SCADA,
Full Form: Supervisory Control And Data Acquisition
For more information of "Supervisory Control And Data Acquisition", see the section below.
» Computing » Networking
Essential Questions and Answers on Supervisory Control And Data Acquisition in "COMPUTING»NETWORKING"
What is SCADA?
SCADA stands for Supervisory Control And Data Acquisition. It is a system used to monitor and control infrastructure processes in industrial sites, such as oil pipelines, water and wastewater networks, electric power transmission systems and manufacturing plants. The system is composed of a computer network that collects data from sensors and instruments in the process environment.
How does SCADA work?
SCADA involves collecting data from various devices located throughout an industrial plant or site. These devices can include valves, pumps, sensors and other instruments that measure different aspects of the process environment. This data is then sent to a control center where it is monitored and interpreted by engineers and operators. This allows them to make decisions about how to control the system in order to achieve optimal performance.
What are some of the advantages of using SCADA?
The use of SCADA systems can provide numerous benefits for industrial operations. These include improved safety by monitoring potential hazardous situations, increased efficiency due to remote monitoring capabilities, cost savings through automated processes and reduced labor costs, improved reliability through redundant systems, improved accuracy of data collection through real-time processing and enhanced analysis tools for identifying trends or problems quickly.
What types of industries benefit most from using SCADA?
Industries that commonly take advantage of SCADA systems are those that need precise monitoring of their processing or production activities such as oil & gas refineries, chemical plants, energy generation (including renewables), water treatment facilities, telecommunications/networks and food & beverage production.
What components make up a typical SCADA system?
A typical SCADA system consists of four main components including hardware (sensors & actuators), software (control & programming applications), communications infrastructure (wired or wireless) and human interface with the system (operator consoles). Together these components allow users to remotely monitor and adjust processes as needed for maximum efficiency.
Is there any special training required for operating a SCADA system?
As with any advanced technology there will be some learning curve involved when working with a new system but typically no special training is required beyond basic understanding of computers/networking technologies plus familiarity with the specific application being used within your organization’s specific setup. Some organizations may also offer direct education programs on their particular implementations.
Final Words:
In conclusion, SCADA provides numerous benefits to organizations through its ability to monitor various industrial processes from a remote location while enabling automation of certain activities. Its integration into cloud computing technologies adds versatility in performance by allowing users access production data from any internet connection with safeguards against network breaches enabled by strong security protocols. As industrial operations become increasingly complex, it is clear that investment in these cutting-edge technologies will pay off immensely due to enhanced accuracy and efficiency throughout the entire production cycle.
SCADA also stands for: |
|
All stands for SCADA |