What does QSD mean in COMPANIES & FIRMS
QSD stands for Quality System Designs. This acronym is often used in business to refer to the standardized process of creating a quality system that meets the requirements laid out by a given industry or regulatory body. Quality systems are designed to ensure that products and services consistently meet the needs of customers through rigorous testing and inspections. Quality systems also help organizations maintain compliance with regulatory standards, as well as provide guidance on how to effectively document their processes and procedures. QSD is an important part of a company's overall quality assurance strategy and helps them ensure that they are producing safe, high-quality products.
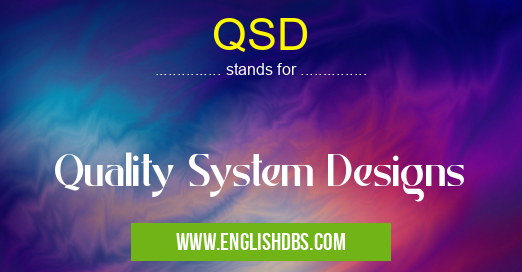
QSD meaning in Companies & Firms in Business
QSD mostly used in an acronym Companies & Firms in Category Business that means Quality System Designs
Shorthand: QSD,
Full Form: Quality System Designs
For more information of "Quality System Designs", see the section below.
What Does QSD Mean in Business?
In business, QSD stands for Quality System Designs. It refers to the systematic approach organizations take when developing a system to ensure that their products meet customer requirements through rigorous quality testing and inspections. Quality system designs must adhere to specific industry standards or regulations set forth by government agencies or other third-party bodies. Organizations use QSDs to develop, implement, audit, and maintain effective quality assurance systems throughout their operations. This includes everything from identifying customer needs and designing processes that meet those needs, to documenting procedures for product inspection and testing.
What Is Included in A Quality System Design?
A quality system design typically includes several elements designed to ensure product safety and quality. These elements can include everything from establishing roles and responsibilities for staff within an organization, devising methods of data collection and analysis for assessing product performance, creating protocols for monitoring supplier performance, designing risk management strategies, developing effective training programs for personnel associated with the production process, conducting internal audits to assess compliance with applicable regulations, defining corrective actions needed if nonconformities are found during inspection or testing, maintaining records of activities related to product development or production processes, preparing reports on progress made against objectives outlined at the outset of any new project or development program ,and overseeing safety measures taken throughout manufacturing operations.
Essential Questions and Answers on Quality System Designs in "BUSINESS»FIRMS"
What is a Quality System Design?
A Quality System Design (QSD) is a suite of documents and tools used to provide a framework for organizational processes and quality assurance. It provides the structure required to ensure that products and services are delivered within the defined requirements of the organization's customers. QSDs can include process flow diagrams, procedures, checklists, recordkeeping/documentation elements, audits, training plans and more.
How do you create a Quality System Design?
The process of creating a QSD begins with identifying all applicable legal and regulatory requirements. Next, an analysis of current customer needs should be conducted to identify areas where changes may be needed in order to meet customer expectations. After that, document what processes will be put in place to satisfy those needs and how they will be monitored for effectiveness. Finally, develop written procedures that detail who is responsible for what activities and any corrective actions that need to be taken if deviations occur.
How often should I review my Quality System Design?
It is recommended that organizations review their QSDs at least annually or after any major change in regulation/requirements or organizational objectives have occurred. This review should include verifying the accuracy of the information contained in each document as well as responding appropriately to any identified non-conformances.
What items should I consider when reviewing my Quality System Design?
As part of your review process you should consider whether or not you need additional documents or updates on existing ones; review any changes made since your last review; validate the system's ability to detect potential errors; evaluate results from previous audits; develop ongoing improvement processes; determine if there are sufficient resources available for implementation; identify any new laws or regulations relevant to your organization; evaluate customer feedback; ensure all employees are aware of changes as well as their responsibilities within the system design.
Why is it important to have an effective Quality System Design?
An effective QSD helps ensure product reliability while also reducing safety risks, cost overruns and service failures associated with low-quality products or services. Additionally, having an effective system design allows organizations to easily identify potential issues before they become problems as well as implement corrective actions quickly in order to prevent further problems from occurring.
Are there guidelines I should follow when creating my Quality System Design?
Yes! There are various best practices and standards out there such as ISO 9001 which provide guidance regarding processes related to quality management systems like document control, internal auditing and corrective action management. These best practices can help ensure that your QSD meets applicable regulatory requirements while also satisfying customer expectations.
What type of roles exist when implementing a Quality System Design?
Depending on the size of your organization there could be several roles associated with implementation including those responsible for developing/updating documents such as Process Flow Diagrams (PFDs), Procedures Manuals (PMs) Records Management (RM); Internal Auditors (IA), Trainers (TR) Staff/Team Leaders (TL); Document Control Coordinators (DCC); Corrective Action Coordinators(CAC)and Accountable Managers/Executives(AM/E).
How many documents must be included in a typical Quality System Design?
While this number can vary depending on factors such as size and scope of operations it generally includes documents such as Process Flow Diagrams (PFD), Procedures Manuals(PM), Records Management Handbooks(RMHB), Internal Audit Checklists(IACL), Training Plans(TP), Change Requests(CR)and Document Control Tools & Templates(DCT&T).
Is it possible make changes during implementation without redoing my entire Quality System Design?
Absolutely! Changes can always be made during implementation however care must be taken not to deviate from existing regulations or performance standards established by customers without prior approval. Additionally, all employees involved must understand how these changes may affect them and their performance.
Final Words:
QSD is an important component of any organization's overall quality assurance strategy. It enables businesses to create effective systems that meet customer requirements while adhering to industry standards or regulatory guidelines. By utilizing a QSD framework when building their operational systems, companies can better monitor their performance over time while minimizing potential risks associated with product defects or noncompliance issues. Companies looking to establish an effective QSD should seek advice from experienced professionals who possess knowledge about best practices within their respective industries.