What does QMPD mean in MANAGEMENT
QMPD stands for Quality Management and Planning Department, an essential business organization. This department is tasked with ensuring the highest quality of product or service produced by a company. It is responsible for setting standards and guidelines that must be met across all departments to maintain quality at expected levels and prevent issues related to poor quality from happening in the first place. QMPD oversees the development, implementation, review, testing and evaluation process in order to make sure the products meet customer requirements. By doing so, it helps to reduce waste and increase efficiency while also improving customer satisfaction.
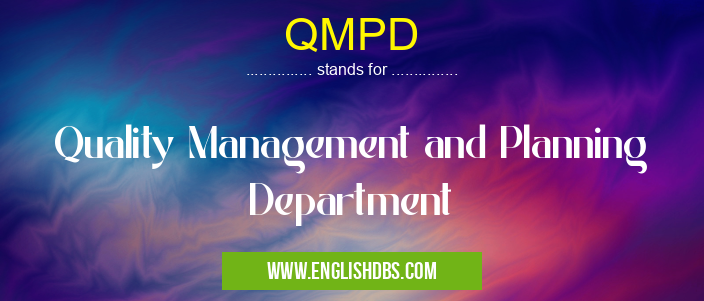
QMPD meaning in Management in Business
QMPD mostly used in an acronym Management in Category Business that means Quality Management and Planning Department
Shorthand: QMPD,
Full Form: Quality Management and Planning Department
For more information of "Quality Management and Planning Department", see the section below.
» Business » Management
Quality Management
Quality management is a system used by organizations to ensure consistency in their products or services. The aim of this system is to guarantee that customers receive goods or services that meet the specified requirements and perform as expected each time they are purchased. Quality management begins with establishing criteria for quality, such as process controls which ensure consistency throughout production; product design which covers both performance needs and safety features; incoming material inspections which check for consistency according to pre-set specifications; inspection during production stages; outgoing product inspections that check against established criteria; further testing enables organizations to create controls that monitor ongoing performance of their products or services; finally customer feedback allows businesses to measure customer satisfaction levels and identify improvement areas. All these steps are monitored by QMPD in order to maintain the desired level of quality in a business’s output.
Planning Department
The planning department is responsible for driving change within an organisation by developing strategies that optimise resources, improve processes, increase efficiency and reduce costs. They are also responsible for carrying out detailed risk assessments before any changes take place within the organisation so any potential problems can be identified early on and dealt with accordingly. By having a dedicated planning department companies can ensure their plans are properly executed resulting in successful projects that have positive outcomes for everyone involved.
Essential Questions and Answers on Quality Management and Planning Department in "BUSINESS»MANAGEMENT"
What are the responsibilities of the Quality Management and Planning Department?
The Quality Management and Planning Department (QMPD) is responsible for ensuring that products or services meet customer requirements in terms of safety, quality, and reliability. QMPD also establishes policies and procedures to ensure quality products or services which meet both internal and external standards. Lastly, it provides a system of feedback to management to enable them to monitor current performance and take corrective action as needed.
What is included in the scope of quality management?
Quality management includes several activities such as design, development, production, testing, inspection, audit, monitoring and maintenance of product/service quality objectives. It also includes analysis of customer feedbacks; identification of potential problems in processes so that corrective actions can be taken before they become costly issues.
How does Quality Management help streamline operations?
Quality management helps organizations streamline their operations by reducing delays caused by re-work or failure to achieve desired goals due to a lack of specific standards. By employing preventive measures like process improvements or risk assessments, companies can save time and resources while achieving better results. Additionally, it encourages employee engagement with an increased focus on continuous improvement which helps to optimize production costs while improving customer satisfaction.
What benefits do organizations gain from using standard Quality Assurance practices?
Adopting standardized Quality Assurance practices offers businesses a number of advantages including increased productivity through repeatable processes; cost savings from fewer errors during production stage; faster turnaround times for new products; improved customer satisfaction resulting in repeat sales; greater conformity between different versions; provision for future modifications without disruptions in operations; improved brand reputation among stakeholders due to assurance on priority given to quality throughout processes; as well as enhanced probability of achieving organizational objectives set out by management through effective compliance with predetermined standards.
Can you explain what Total Quality Management is?
Total Quality Management (TQM) is an approach used by organizations with an aim towards continual improvement in all areas - ranging from service quality & operational efficiency to financial performance & employee loyalty - through implementation & sustained adherence towards explicit standards & guidelines designed based on customer demands & preferences. An effective TQM strategy involves understanding customers’ requirements accurately & integrating them into all aspects throughout the organization’s end-to-end operational cycle via timely communication between departments & introduction of relevant corrective measures wherever applicable, along with staff training & motivation initiatives for maximum effectiveness.
How does Lean Six Sigma support quality improvements?
Lean Six Sigma (LSS) is an iterative approach towards eliminating redundant waste from processes while striving for near perfection through comprehensive data analysis & implementation of evidenced-based solutions that are derived from observed patterns highlighted across internal documents & tools such as flowcharts or visually displayed process maps etc., enabling timely identification & resolution of systematic discrepancies that otherwise may continually affect production yields / outputs.. This method utilizes statistical data collected both prior to any proposed changes being made (in order to compare reflected differences later following successful implementation) coupled with refined critique techniques applied towards process layout designs so as to deliver measurable items regarding cost reduction savings or gains made via optimization efforts undertaken.
Why must we maintain proper documentation and records related to product/service quality?
Proper documentation and records should be kept related to product/service quality for several reasons including identifying non-conformances during operations offered by a company quickly so that immediate interventions can be instituted; enhance traceability when dealing with multiple vendors supplying raw materials/components who need accesses against historical details recorded stored within a centralized system; meet legal compliance requirements set out within industry standards demanded by regulating authorities if applicable e.g., safety considerations when handling hazardous materials under controlled conditions where certain thresholds must not be exceeded beyond accepted levels specified within codes enforced; plus act as evidence when defending claims against liabilities related against unfounded attributes associated outside genuine defects noticed within delivered goods/services.
Final Words:
In conclusion, QMPD plays a vital role in ensuring customer satisfaction through consistent high-quality products or services backed up with effective planning strategies implemented by its dedicated personnel team. Companies benefit greatly from having an effective QMPD as it not only helps them avoid unnecessary costs but also provides them with assurance that their products will meet all expectations set forth by customers.