What does QC OK mean in HARDWARE
QC OK is a term used in computing to indicate that quality control has been completed successfully and the product is approved. Quality control (QC) is a process of regularly checking and verifying the quality of all components, parts, products, and production processes. When done successfully, QC OK indicates that an item has passed the necessary tests or inspections, and it is safe for use or sale.
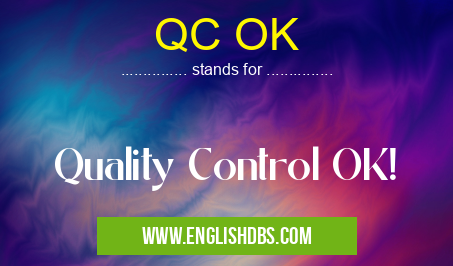
QC OK meaning in Hardware in Computing
QC OK mostly used in an acronym Hardware in Category Computing that means Quality Control OK!
Shorthand: QC OK,
Full Form: Quality Control OK!
For more information of "Quality Control OK!", see the section below.
Quality Control
Quality control (QC) is an essential step in any manufacturing process, from ensuring a safe work environment to guaranteeing product effectiveness and reliability. It involves verifying the quality of all components, parts, products, and production processes through regular inspections. QC also includes testing for accuracy in design specifications and preventing errors before they occur. By verifying that each component meets design requirements and adheres to safety regulations, QC helps ensure that only top-quality products are released into the marketplace.
Essential Questions and Answers on Quality Control OK! in "COMPUTING»HARDWARE"
What is QC OK?
QC OK stands for Quality Control OK. It is a confirmation that the quality of a product or service has been checked and found to be satisfactory.
How can I ensure Quality Control for my products?
Quality Control involves analyzing your process and procedures to identify weaknesses or potential areas of improvement. Implementing controls such as inspections, tests, validation processes, and documentation will help you ensure the quality of your products or services.
How often should I conduct Quality Control checks?
The frequency of QC checks should depend on the nature and complexity of your business operations. Generally speaking, it’s recommended to review your quality control measures at least once every quarter, but more frequent checks may be necessary depending on the specific needs of your business.
What are the benefits of having effective Quality Control in place?
Effective quality control helps to ensure customer satisfaction by providing consistently high-quality products or services. Additionally, it can help to minimize expenses by reducing waste and rework costs associated with poor Quality Control processes.
What is a Quality Manager responsible for?
A Quality Manager typically oversees all aspects of an organization’s quality assurance program including setting standards, establishing policies, monitoring performance metrics, and developing internal procedures. They also play a key role in developing improvement plans when issues arise during the QA process.
What kind of tools do I need to implement an effective Quality Control program?
Setting up an effective QC program requires several different tools including inspection forms/checklists, test equipment (e.g., thermometers), statistical analysis software (e.g., Six Sigma), validation procedures (e.g., FMEAs), document control systems (e.g., electronic records), and data collection systems (e.g., barcodes).
Do I need specialized training for implementing a QC system?
Yes, most organizations require their personnel to be trained in various aspects of quality control before they can begin implementation activities such as inspecting materials or products during production runs or completing detailed reviews after production is complete.
What documents do I need to maintain my Quality Management System (QMS)?
You should maintain documents such as operational procedures, work instructions, training records, audit reports, inspection results etc which provide evidence that your QMS meets specific criteria set out by ISO 9000 standards or other appropriate industry standards.