What does QA/QC mean in GENERAL
Quality assurance/quality control (QA/QC) is an essential part of any business or process. QA/QC is a system of measures and procedures that ensure that quality standards are met in order to produce a product or service that meets customer expectations. With quality control and assurance, companies can identify opportunities for improvement, reduce costs, and improve customer satisfaction. Quality assurance/quality control activities aim to reduce defects, prevent problems, and maintain consistency in products and services.
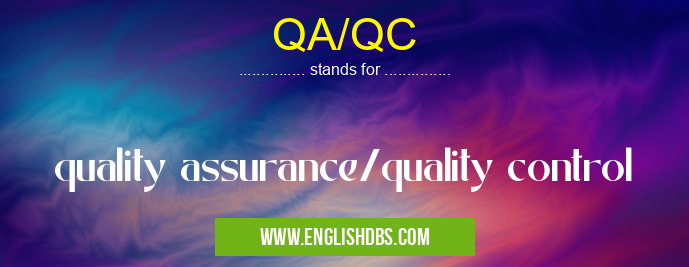
QA/QC meaning in General in Business
QA/QC mostly used in an acronym General in Category Business that means quality assurance/quality control
Shorthand: QA/QC,
Full Form: quality assurance/quality control
For more information of "quality assurance/quality control", see the section below.
Quality Assurance
Quality assurance focuses on preventing errors before they occur. It involves planning ahead to understand the risks associated with quality issues and then implementing preventive measures that help keep those issues from occurring. Quality assurance also means regularly assessing processes and systems to make sure they're producing the intended results — qualitatively speaking — and making adjustments accordingly. This includes examining how efficiently each process works as well as how well it meets all applicable quality standards.
Quality Control
Quality control, on the other hand, involves testing products created during the manufacturing process to make sure they meet customer specifications. This entails subjecting each item to various tests to identify mistakes or variations from predetermined criteria so they can be corrected immediately if needed. Quality control also means verifying product safety and ensuring compliance with relevant industry regulations so end-users ultimately receive safe and reliable products.
Essential Questions and Answers on quality assurance/quality control in "BUSINESS»GENERALBUS"
What is quality assurance/quality control?
Quality assurance/quality control (QA/QC) is the process of making sure a product or service meets the required specifications and meets the customer's needs. QA/QC includes activities such as inspection, testing, audits, and monitoring production processes to ensure that products and services meet acceptable levels of quality.
What are the benefits of implementing QA/QC?
Implementing QA/QC in an organization can help increase customer satisfaction and reduce costs related to re-work and lost profits due to poor quality products. It also improves efficiency by ensuring that manufacturing processes are running smoothly and efficiently.
What are some steps taken in a QA/QC program?
Steps taken in a QA/QC program include detailed inspections, testing, evaluation of past results and trends, auditing supplier capabilities and performance, controlling production processes, monitoring product performance over time, and responding to customer feedback.
Is it necessary to have a QA/QC program in place?
Yes, having a well-developed QA/QC program is essential for any organization that wants to produce high-quality products or services consistently. Without these measures in place, companies risk delivering inconsistent products with lower levels of quality which can lead to customer dissatisfaction and lost revenue opportunities.
How does one know if their current QA/QC practices are working properly?
To determine whether your current practices are working properly you should evaluate both objective measurements (e.g., nonconformance rates) as well as subjective measurements (e.g., customer surveys). Additionally, you should review previous trends over time to identify any areas needing improvement or potential issues before they become larger problems.
Who is responsible for implementing a successful QA/QC program?
In order for a successful QA/ QC program to be implemented person responsible need to have project management experience with background knowledge of product development processes along with an understanding of organizational policies & procedures related to quality management systems (ISO 9001). The individual should also have good interpersonal skills with experience dealing with different internal departments such as Manufacturing, Purchasing, Sales & Marketing as well external suppliers & vendors in order coordinate all aspects successfully while providing guidance regarding implementation & additional corrective action if needed.
What kind of resources are needed for implementation and maintenance of an effective QA/ QC process?
Resources needed for implementation including personnel training on relevant standards such as ISO 9001 along with investment in equipment used for inspections & tests such as calibration tools for measuring devices used during various stages throughout production process; other materials include templates used written instructions & checklists for staff when performing specific tasks or operations related producing goods & services. For maintenance ensuring all tools correctly calibrated as per standard requirements also important making sure personnel regularly updated on changes within relevant standards policies influencing their roles within organization.
Final Words:
Overall, quality assurance/quality control (QA/QC) is a key component of doing business successfully. It helps you weed out any potential problems before they become major issues while also maintaining consistency in your products or services so customers are satisfied with their orders every time. Implementing robust quality assurance/quality control procedures can help your business stand out from competitors by demonstrating commitment to quality excellence across all aspects of production—from start to finish!