What does PID mean in COMPUTING
PID stands for Proportional-Integral-Derivative, and is a control loop feedback mechanism used in industrial processes. It's a powerful tool capable of rapid and precise control of any process that requires a steady input to output ratio. PID control systems are found in all automated machinery, including robotic systems and other automated systems such as elevators, HVACs, or even ovens. Simply put, PID can provide complex solutions to complex problems quickly by settling on the most efficient combination of components to get the desired result.
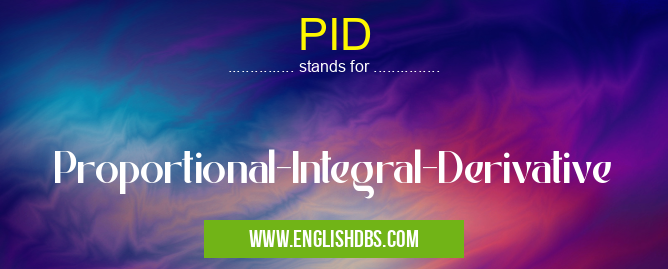
PID meaning in Computing in Computing
PID mostly used in an acronym Computing in Category Computing that means Proportional-Integral-Derivative
Shorthand: PID,
Full Form: Proportional-Integral-Derivative
For more information of "Proportional-Integral-Derivative", see the section below.
How it Works
A PID controller works by using three separate components — proportional (P), integral (I), and derivative (D) — to produce an output response that follows a given setpoint more closely than other controllers would. When a process needs to be regulated or controlled, these three components work together to adjust parameters based on current conditions until the desired level of accuracy has been achieved. The Proportional component is responsible for adjusting the output power according to the difference between the desired value and actual value; think of this as turning up the heat when things are too cold or turning down the lights when it's too bright. The Integral component ensures that minor discrepancies don't get out of hand by adding an additional response if needed; think of this as making sure that your house stays at 70 degrees no matter how hot or cold it gets outside. Finally, the Derivative component detects how quickly things are changing and responds accordingly; think of this as a thermostat that is constantly monitoring temperatures so you never have to worry about getting too hot or cold.
Benefits
PID controllers offer significant advantages over other control systems because they allow precision tuning with minimal effort while providing high levels of robustness and accuracy. This allows users to fine-tune their processes easily without having to adjust large numbers of variables individually like in traditional manual tuning techniques. Additionally, since all three components act independently from each other, minor adjustments can be made in real time which helps reduce oscillations in response time caused by sudden changes in conditions such as temperature or pressure. This ensures smoother transitions which would otherwise cause large fluctuations leading potentially lead to successions failures or other issues due to incorrect values being used for controlling certain processes.
Essential Questions and Answers on Proportional-Integral-Derivative in "COMPUTING»COMPUTING"
What is PID?
PID stands for Proportional-Integral-Derivative. It is a type of feedback control system used to adjust the process of something in order to reach an optimal performance. It relies on three basic principles — proportional, integral and derivative — in order to achieve desired control objectives.
How does PID work?
PID works by adjusting the process based on feedback it receives from the system. This includes applying adjustments or corrections in proportion to current error that have occurred over time. Specifically, proportional, integral and derivative terms each represent different variables which can be adjusted to change the output of the system.
What are the benefits of using PID?
The primary benefit of using PID is its ability to maintain an optimal output level despite any changes or fluctuations in the environment. Additionally, it ensures stability and accuracy while reducing errors, as well as providing good tracking performance without overshooting or oscillation.
What are some common applications of PID?
Common applications of PID include temperature control systems, guidance systems, speed control systems and many other industrial processes that require precise feedback measurements and monitoring.
When should I use a PID controller?
A PID controller should be used whenever you need a high degree of accuracy and precision when controlling various processes. If you're dealing with any nonlinear environmental disturbances or changes this is especially useful as it can help maintain a constant output despite those disturbances or changes.
How do I tune a PID controller?
Tuning a PID controller can be done manually or automatically by adjusting its proportional gain (Kp), integral gain (Ki) and derivative gain (Kd). The best way to tune these settings is through trial-and-error experimentation whilst observing how it interacts with the system being controlled until reaching satisfactory results in terms of performance, accuracy and stability.
What are some drawbacks associated with using a PID controller?
Although efficient under most conditions, some drawbacks associated with using a PID controller include difficulty in tuning parameters correctly and possible instabilities due to large parameter settings such as high gains which result in amplification of noise present in measurement signals. Additionally, they may require frequent manual adjustments depending on the parameters chosen initially when setting up the system.
How can I prevent overshoot when using a PID controller?
Overshoot can be prevented by reducing Kp values while increasing Ki values which will help eliminate any deviations caused by external disturbances such as noise or vibration present within the measured environment where your system is operating at steady state operating conditions.
Final Words:
PID controllers offer tremendous advantages over other forms of control systems by allowing for efficient tuning with minimal effort while still providing robust precision results. By combining proportional, integral and derivative responses into one unified system capable of acting independently from one another, PID controllers are able to regulate many different processes with just minimal input from operators. For situations requiring rapid response times with high levels of accuracy regardless of external conditions, PID stands as an excellent choice for controlling automated machinery and various industrial processes alike.
PID also stands for: |
|
All stands for PID |