What does PFR mean in BUSINESS
Part Feasibility Report (PFR) is a document that provides an overview of the potential usefulness and viability of a proposed project in terms of its economic, operational, environmental and financial feasibility. It consists of data collected both from internal sources as well as from external sources related to the proposed project. This report is generally used by decision makers to gauge the long-term profitability and sustainability of an investment or project. The report focuses on analyzing different aspects such as market situation, demand trends, competitive analysis, strategic positioning, regulatory requirements, technical feasibility and operational risks associated with the proposed project.
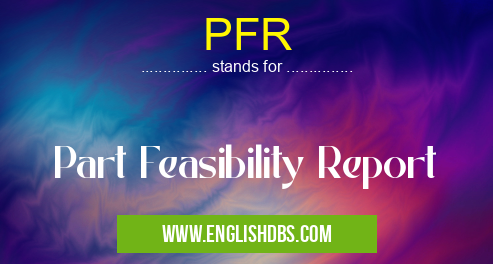
PFR meaning in Business in Business
PFR mostly used in an acronym Business in Category Business that means Part Feasibility Report
Shorthand: PFR,
Full Form: Part Feasibility Report
For more information of "Part Feasibility Report", see the section below.
What does PFR Stand for?
PFR stands for Part Feasibility Report. It is a document prepared by a consultant or hired expert which contains an assessment of the potential benefits and prospects for success of an undertaking before implementation or investments are made in it.
Meaning in Business
PFRs are primarily used by businesses and organizations to evaluate alternative courses of action related to investing in new projects or products. They are particularly useful to determine if particular projects should be undertaken from a resource point of view due to their ability to provide information on cost-benefit ratios as they relate to operating costs, revenues generated, labour demands, market conditions, etc. Additionally, PFRs can help identify any potential risks associated with implementation plans before resources are committed—allowing businesses or organizations time to address them accordingly.
Essential Questions and Answers on Part Feasibility Report in "BUSINESS»BUSINESS"
What is a Part Feasibility Report?
A Part Feasibility Report (PFR) is used to evaluate and analyze the feasibility of manufacturing a part or product. It provides a comprehensive review of all aspects of creating the component, including cost analysis, design considerations, material selection, production requirements, and more.
How is a Part Feasibility Report produced?
The production process of a Part Feasibility Report includes collecting data on the component being evaluated, conducting research into the costs associated with producing it, and analyzing the technical aspects of designing and manufacturing it. Additionally, alternative materials and processes may be considered during the development of the report as well.
What information does a Part Feasibility Report include?
A Part Feasibility Report typically includes an analysis of costs associated with producing the part or product; design considerations; material selection; production requirements such as machinery and labor needed to produce it; environmental factors such as waste management techniques; regulatory compliance issues; safety considerations; quality control measures; and risk mitigation strategies.
Who produces a Part Feasibility Report?
A Part Feasibility Report is often created by engineers or other professionals who are familiar with designing and manufacturing components. Additionally, other professionals may be involved in producing this type of report depending on specific industry requirements.
When is a Part Feasibility Report necessary?
A Part Feasibility Report may be required when bringing new parts or products to market or in order to assess current production methods. It can also provide guidance on how to determine if certain processes or materials should be used for production.
What are some advantages of using a Part Feasibility Report?
Using a Part Feasibility Report can help reduce costs associated with producing parts or products by providing an objective analysis into feasible options for utilizing machine resources, labor resources, materials selection, environmental impact considerations, etc. Additionally it can help identify potential risks that could arise during production before they become an issue in order to minimize their impact.
Are there any disadvantages to using a Part Feasibility Report?
One disadvantage that comes with using a Part Feasibility Report can be that it takes time for all aspects of the process involved in creating one to be thoroughly reviewed. This means that if time is limited for bringing new parts/products to market then this can present an issue in meeting deadlines while ensuring accuracy in results.
What types of organizations use Part Feasibility Reports?
Organizations across many industries utilize Parts Feasibility Reports in order to evaluate their processes for producing components - especially when introducing new parts/products or assessing changes made within existing operations. Some common examples include automotive manufacturers using them for evaluating assembly line efficiency; aerospace companies testing prototype designs; food producers checking ingredient sources; oil producers analyzing pipeline routes etc..
Final Words:
The Part Feasibility Report (PFR) is an important tool in determining whether a particular project should be undertaken by businesses or organizations in order to minimize risk associated with the implementation plan while also maximizing returns on investment (ROI). It provides useful insight into potential areas where strategic changes might need to be made prior to committing resources; thereby ensuring long term sustainability without excessive expenditures.
PFR also stands for: |
|
All stands for PFR |