What does ATC mean in MANUFACTURING
The Automatic Tool Changer (ATC) is a device that allows users to quickly and efficiently change tools on their machines, making it easier to complete tasks with greater accuracy and speed. This technology has become increasingly important for today's manufacturing processes, allowing for more productivity as well as improved quality and efficiency.
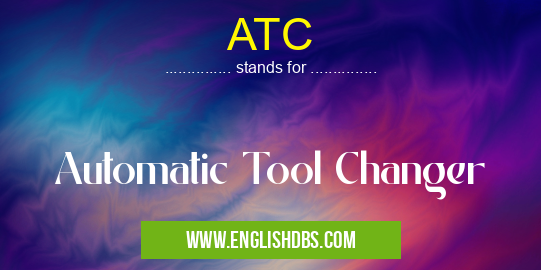
ATC meaning in Manufacturing in Miscellaneous
ATC mostly used in an acronym Manufacturing in Category Miscellaneous that means Automatic Tool Changer
Shorthand: ATC,
Full Form: Automatic Tool Changer
For more information of "Automatic Tool Changer", see the section below.
Benefits of ATC
Using an Automatic Tool Changer (ATC) offers several key benefits for any manufacturing process. Firstly, it reduces setup time for each job significantly since there is no need to manually adjust each tool before starting work; the tool changer will automatically select the desired tool from its available options. Additionally, with shorter set up times comes less downtime which translates directly into higher production rates. Finally, since all of the operations are taken care of by one device, operators can focus on other tasks instead such as monitoring progress or performing quality assurance checks.
Essential Questions and Answers on Automatic Tool Changer in "MISCELLANEOUS»MANUFACTURING"
What is an Automatic Tool Changer (ATC)?
An Automatic Tool Changer (ATC) is a mechanism typically used on a CNC machine that allows for multiple tooling to be picked up and placed on the spindle for use during the cutting process. This eliminates the need for manual tool changes, saving time and increasing efficiency in part production.
How does an Automatic Tool Changer work?
The ATC works by automatically securly gripping, lifting, and depositing the tools at specified locations within the machinng process. This allows the machine operator to move from one operation to another without manually changing out tools each time.
What kinds of operations can an ATC perform?
An ATC can perform a variety of operations including drilling, boring, counterboring, reaming, tapping and more depending on size and capabilities of particular model.
What are some advantages of using an Automatic Tool Changer?
An ATC offers many advantages over manual tool changing including quicker cycle times due to faster tool change over; improved accuracy due to repeatable positionng; fewer errors because of automatic orientation and location confirmation; less fatigue on operators since they no longer have to manually change out tools; as well as overall cost savings due to increased productivity.
Are there any downsides to using an Automatic Tool Change?
The major downside is expense since ATC systems are considerably more expensive than manual tool changers. Some other potential issues include potential wear and tear on moving parts caused by long and frequent shifts or high-speed usage, as well as potentially programming complexity when dealing with complex geometries or difficult materials.
What types of parts are best suited for an Automatic Tool Change system?
Any parts with multiple operations or processes that require frequent tool changes are ideal candidates for use with an ATC system such as automotive components, aerospace components or electronic devices, just to name a few examples. Parts with shallow pockets and small backside plunges can be accomodated with some available models.
Is there any maintenance required with an Automatic Tool Change system?
Regular maintenance should always be performed according to manufacturer guidelines in order ensure optimal performance of your ATC system including periodic checks of ball screws/bearings/rail tracks/fasteners/motor mounts etc., depending on unit type. It is also important to regularly clean all areas of dirt build-up in order ensure optimal operation as well as lubricate moving components such as rails bearings etc., as necessary.
Are there any safety considerations associated when operating an Automatic Tool Change system?
Yes - it is important that operators adhere to proper safety measures when working around automated equipment - know how it operates inside out; take the necessary steps prior machines startup; follow all lockout/tagout procedures; understand emergency stop functions etc., in order stay safe while utilizing these devices. Additionally it's always important wear proper protective gear such protect yourself against potential hazards such flying swarf / dust particles etc., that may be generated during part machining processes.
Does every CNC machine come standard with an Automatic Tool Change unit or do they have be purchased separately?
This depends entirely on what type CNC machine you're purchasing - some units come standard equipped with this feature while others may require additional purchase either right away or down road - however most higher end models tend include built-in compatibility with these mechanisms so it's always worth double checking specifications beforehand if considering this feature.
Final Words:
The Automatic Tool Changer (ATC) is an invaluable piece of hardware for modern manufacturing companies as it helps them save time and resources while increasing production rates without compromising on accuracy and precision. The simplicity combined with effectiveness makes this technology an ideal addition to any factory setting in order to maximize efficiency and output.
ATC also stands for: |
|
All stands for ATC |