What does PDQ mean in MANUFACTURING
PDQ stands for Part Drawing and Quantity. This abbreviation is commonly used in industrial engineering and manufacturing to describe the situation when a company needs to design a new part and determine how many of them will be manufactured. In this context, PDQ is an acronym that provides insight into the various requirements needed for successful product development and production.
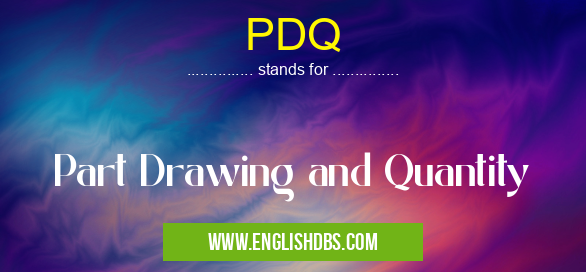
PDQ meaning in Manufacturing in Miscellaneous
PDQ mostly used in an acronym Manufacturing in Category Miscellaneous that means Part Drawing and Quantity
Shorthand: PDQ,
Full Form: Part Drawing and Quantity
For more information of "Part Drawing and Quantity", see the section below.
Description
At its core, PDQ refers to two key components that are necessary when designing and producing a new part or product. The first component involves the drawing of the part — often referred to as a model drawing — which outlines all of the features, dimensions, tolerances, materials, configurations and other details related to the final product design. The second component includes determining the quantity of parts needed for production; this includes forecasts of future demand as well as any special considerations regarding inventory management. Once both pieces are established, manufacturers can then proceed with creating a prototype or ordering enough parts from suppliers for production.
Essential Questions and Answers on Part Drawing and Quantity in "MISCELLANEOUS»MANUFACTURING"
What is PDQ?
PDQ stands for Part Drawing and Quantity. It is a tool used to ensure that all the parts required for an assembly or manufacturing process will be included in the order. The PDQ tool also helps to ensure that no extra parts are ordered, reducing waste and unnecessary costs.
How is a PDQ used?
A PDQ is typically used to create a detailed list of the necessary components, detailing their quantities and drawings which can be used as a reference for when ordering parts. This list can then be referenced during the production process to ensure that all necessary parts have been acquired.
What are the benefits of using a PDQ?
Using a PDQ helps to streamline part order processes, ensuring that only those parts necessary for production are ordered and reducing waste. Additionally, it helps to reduce errors in part order by providing clear specifications on what parts need to be ordered and in what quantity they should arrive in.
What information does a PDQ include?
A typical PDQ includes information such as component name, part number, quantity needed, drawing of each component, surface finish/treatment requirements and possible vendor sources for each component.
Is a PDQ mandatory when ordering components?
It depends - in some cases having a detailed list of components provided by a supplier may suffice when ordering parts without needing to provide a more comprehensive document such as a PDQ. However, if more clarity on the exact details needed when ordering parts is required then using an up-to-date PDQ document can be beneficial both economically (reducing overspending) and efficiency (making sure all necessary materials are available at the factory).
Why is accuracy important with regard to using a PD Q?
Ensuring accuracy with regards to using a PD Q not only helps minimise error but can also improve lead times and reduce waste costs incurred from incorrect or additional orders being made due to inaccurate or out-of-date documentation. It's therefore important that any changes made within an organisation with regards to updates or new product additions are correctly captured within an up-to-date version of the respective company's PD Q document.
How often should I update my company's current version of its Part Drawing & Quantity (PD Q)?
That would depend on how frequently there are changes being implemented with regards to product specification or design; however it's generally recommended that companies update their documents at least twice per year, or more often if there are frequent changes being made. Doing so ensures accuracy throughout their operations; minimising unnecessary mistakes due to outdated documentation which could lead them incurring extra costs down the line.
What type of software should I use if creating my own Part Drawing & Quantity (PD Q)?
Most companies utilise either CAD software or Product Lifecycle Management systems such as PLM (Product Lifecycle Management) software when creating their own internal documents such as Part Drawings & Quantities (PD Q). These types of software offer great advantages compared to traditional spreadsheets with built-in capabilities such as automated calculations based on pre-defined parameters — saving time and making sure data accuracy remains consistent throughout its use.
Final Words:
In summary, PDQ is an acronym used by engineers and manufacturing companies to refer to Part Drawing Quantity — an essential step in product development that requires both detailed drawings and proper planning related to production quantity. Taking these steps before beginning production ensures that everything runs smoothly throughout the process, resulting in cost savings in both time and money.
PDQ also stands for: |
|
All stands for PDQ |