What does PCS mean in MANUFACTURING
Part Coordinate System (PCS) is a system used to accurately measure and locate complex shapes in three-dimensional space. It is used extensively in the manufacturing of parts for machining, as well as in robotics and design engineering. The PCS is a powerful tool that can save time, money, and resources when properly implemented.
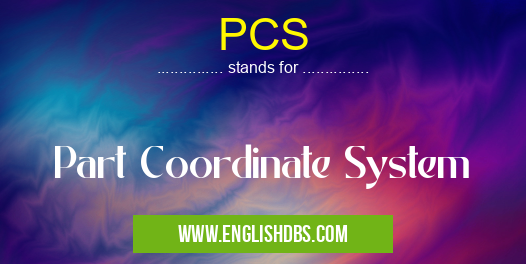
PCS meaning in Manufacturing in Miscellaneous
PCS mostly used in an acronym Manufacturing in Category Miscellaneous that means Part Coordinate System
Shorthand: PCS,
Full Form: Part Coordinate System
For more information of "Part Coordinate System", see the section below.
Explanation
The Part Coordinate System (PCS) utilizes coordinate geometry to orient a part relative to a datum point or line on which it rests. For example, if an object needs to be cut at an angle of 50 degrees according to its center line, the PCS can be used to create a reference plane aligned with the center line that will be used for cutting. This helps ensure accurate machining with minimal distortion of the part's shape. In robotics and automated assembly systems, the PCS can assist with programming different components of an automated production line by providing precise measurements on how each component should interact with one another as well as when it should start and stop functioning. This makes for efficient use of machinery by avoiding overlap or interference between them. Finally, design engineers also rely heavily on the PCS when creating new products from scratch or prototyping existing designs. By using advanced 3D software such as Autodesk Inventor or SolidWorks, they can model an entire product in three-dimensional space down to small details such as threads and angles while ensuring accuracy through the use of the PCS. This way they can quickly test out different designs and find working solutions faster than ever before.
Essential Questions and Answers on Part Coordinate System in "MISCELLANEOUS»MANUFACTURING"
What is a Part Coordinate System (PCS)?
A Part Coordinate System (PCS) is a 3D coordinate system used to specify the position of an object or tool in a manufacturing process. It defines the orientation and location of the workspace relative to a reference point. PCSs are used in robotic and automated manufacturing processes such as cutting, grinding, drilling, and welding.
How does PCS work?
The PCS works by using a set of coordinates that define any point in three-dimensional space. These coordinates can be used to locate a specific machine component or tool in relation to the reference point established for the workspace. The PCS then determines how the component or tool should be moved in order to interact with other parts or surfaces correctly. This ensures that each component is properly positioned and oriented before it is used.
Why do we need to use PCS?
Without using PCS, it would be difficult to accurately position machine parts and tools with precision relative to one another in a production process. This can lead to costly errors and delays because incorrect positioning of tools can cause workpieces to be machined inaccurately, resulting in product defects or rework time being needed. By using a PCS, manufacturers ensure that their components are placed correctly relative to one another within the production process.
What type of information is required for establishing PCS?
To establish a Part Coordinate System, information such as location coordinates (X, Y & Z axis), origin offsets (with respect to origin) and orientation angles must be provided for each part involved in the production process. Additionally, some production processes may require additional parameters such as the size and shape of components being machined or welded. All this information should be clearly communicated across all stakeholders involved in production so everyone has an understanding of where each part needs to go within the process.
Is it easy to switch from one PCS setup/configuration/coordinate system as opposed changing manually?
Yes, switching between different setup configurations on PCS systems is relatively simple due to their user-friendly interface which allows users to quickly modify existing setups without needing highly technical expertise or manual labor input. When different parts need accessing during production cycles this feature makes it easier for operators who don't have advanced engineering knowledge.
Do all PC systems use same reference points?
No, while all Part Coordinate Systems will use three-dimensional X Y Z coordinates they can have completely different origin points depending on what type of manufacturing process they are needed for so two similar looking machines could have very different reference points.
Can two robots share same coordinates if they are doing same job (welding/cutting etc.)?
Yes, two robots can use the same coordinates if they are performing identical tasks because all their axes will move accordingly along their respective paths until both reach their designated endpoints at exactly the same moment.
Can I change my coordinate system after I program my robot?
Yes you can change your coordinate system after programming your robot by editing its axis positions within its programmed path. This requires re-calculating certain movements but if done correctly will result in no interruption of performance.
How important is accuracy when mustering up references on part coordinate systems?
Extremely important; inaccuracies introduced into reference points at any stage of setup configuration may lead not only failed products but also operator safety risks due validating incorrect positions causing unexpected mechancial movements.
:What training do I need before operating on part coordinate systems?
Before using Part Coordinates Systems operators should received proper training covering instruction on safety procedures related with productivity aspects like understanding axis locations & limits along with setting up & calibrating motion parameters according established requirements
Final Words:
In short, Part Coordinate Systems are invaluable tools across many industries that allow for greater efficiency when producing high-precision parts or planning robot automation processes. By accurately measuring and locating objects in three-dimensional space, manufacturers can save resources while still guaranteeing quality results whether they are producing parts for machining or prototyping designs from scratch.
PCS also stands for: |
|
All stands for PCS |