What does OAC mean in BUSINESS
Operation Analysis and Control (OAC) is the systematic examination of operational processes and procedures to determine which ones need improvement. It involves the analysis of production processes and methods, with the aim of increasing efficiency and reducing costs. This type of business analysis can help a company make better decisions about how it conducts its day-to-day operations, leading to improved performance over time. OAC helps companies identify problem areas and provide solutions for them, ensuring that the most effective processes are being used. In addition to improving efficiency, OAC can also improve customer satisfaction by providing better quality products and services in a timely manner.
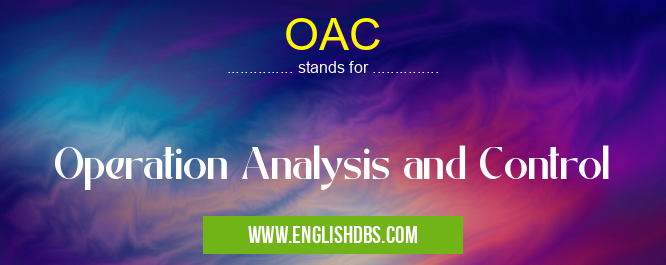
OAC meaning in Business in Business
OAC mostly used in an acronym Business in Category Business that means Operation Analysis and Control
Shorthand: OAC,
Full Form: Operation Analysis and Control
For more information of "Operation Analysis and Control", see the section below.
Process of Operation Analysis & Control
Operation Analysis & Control is an important component of managing modern businesses effectively. It consists of four main steps: planning, analyzing, controlling, and evaluating operations. During the planning stage, managers analyze current operations to gain insights into what must be improved or adjusted. They then develop strategies to achieve desired results and create objectives that will support those strategies. The analysis stage involves identifying trends in current data that could affect operations or cause problems in the future. Controlling involves establishing targets or benchmarks to measure success against; this allows managers to assess progress towards goals over time. Finally, during evaluation phase, managers review performance data to determine whether objectives have been met successfully or if adjustments need to be made in order for objectives to be achieved going forward.
Benefits of Operation Analysis & Control
The use of Operation Analysis & Control offers many advantages for businesses looking for ways to improve their operational performance. By gaining a better understanding of existing operations, management is able to see which areas need improvement or adjustment and make targeted changes accordingly. Furthermore, having clear goals in place helps keep teams motivated while they strive for specific outcomes; this boosts morale within the organization as well as productivity overall. Additionally, having regular reviews means that any potential areas which might require more attention are quickly identified and taken care of before they become major issues – saving both time and money down the line. These immediate gains then compound over time as improved processes become habitual practice among teams working within the organization.
Essential Questions and Answers on Operation Analysis and Control in "BUSINESS»BUSINESS"
What is Operation Analysis and Control?
Operation Analysis and Control (OAC) is a branch of industrial engineering which focuses on analyzing the system performance in order to identify and improve problems, processes, and operations. OAC utilizes mathematical models and statistical analysis to evaluate the production system as a whole. The end goal is to ensure the highest possible efficiency in the production process by using advanced techniques such as automation, simulation, optimization, scheduling, forecasting, etc.
What are the applications of Operation Analysis and Control?
The application of Operation Analysis and Control can be found across multiple industries such as manufacturing, logistics, supply chain management, healthcare services, etc. With this technology being adopted into multiple departments within organizations including marketing, finance, HRM or human resource management it can have an impact on almost all facets of business operations. OAC can also be used for day-to-day activities like project planning & monitoring as well as for long-term goals such as budgeting or forecasting for future demands.
What are some of the benefits provided by Operation Analysis and Control?
Some of the primary benefits associated with employing a OAC approach include enhanced operational efficiency resulting in cost savings; improved workforce productivity; improved customer satisfaction; reduced lead time; better decision making capabilities; identification of potential areas for improvement in processes or workflow; improved capacity utilization; better risk management capabilities; increased accuracy in forecasting costs & demand; etc.
How does Operation Analysis and Control help to cut costs?
By employing sophisticated mathematical models to analyze a company’s current operation flow & processes along with their limitations & capabilities thereof it helps identify where cost savings can be achieved through more efficient use of resources or eliminating duplication in workflows etc. Additionally OAC enables companies to utilize predictive analytics to forecast demand & manage logistics more effectively so that inventory stockpiling can be avoided ultimately leading to further cost savings.
Does Operation Analysis and Control involve any technical expertise?
Yes it does require certain technical knowledge around machine learning algorithms or advanced statistical methods depending upon how complex your requirements are. Additionally having experienced personnel who understand how various systems interact with one another is essential when attempting to accurately model your operational environment within your organization.
Does implementing Operation Analysis and Control require specific technology solutions?
While no specific solution is required there are various software options available that provide features which may aid organizations running OAC programs such as gap analysis tools, data analysis dashboards or risk simulation tools etc depending upon what exactly they need from their program.
Final Words:
In conclusion, Operation Analysis & Control provides organizations with valuable insight into existing operating procedures; this knowledge enables management teams to adjust their internal practices with pinpoint accuracy so that optimum efficiency can be achieved on all levels - from individual employees up through entire departments - helping them reach their goals faster while reducing risk factors long-term. OAC is a powerful tool which should not be overlooked when striving towards better business performance overall – no matter what industry you’re in!
OAC also stands for: |
|
All stands for OAC |