What does NQC mean in BUSINESS
Non Quality Cost (NQC) refers to the costs incurred by an organization due to the failure of its products, services and processes to meet the agreed-upon requirements and expectations. These costs usually occur when there is a problem with product quality, supplier quality or customer service. NQC can be divided into two categories: prevention and appraisal costs. Prevention costs refer to those efforts made by an organization to ensure that their products and services meet the desired quality level; while appraisal costs are incurred when conformance to standards is tested or audited.
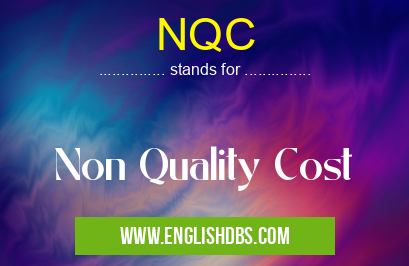
NQC meaning in Business in Business
NQC mostly used in an acronym Business in Category Business that means Non Quality Cost
Shorthand: NQC,
Full Form: Non Quality Cost
For more information of "Non Quality Cost", see the section below.
Essential Questions and Answers on Non Quality Cost in "BUSINESS»BUSINESS"
What is Non-Quality Cost?
Non Quality Cost (NQC) is the cost associated with producing goods and services that do not conform to customers' expectations or the required quality standards. This includes items such as warranty expenses, customer service or rework activities.
What categories does Non-Quality Cost fall under?
Non Quality Cost (NQC) can be divided into two categories; prevention costs and appraisal costs. Prevention costs refer to those efforts taken by an organization in order to ensure that their products and services meet the desired quality level; while appraisal costs are incurred when conformance to standards is tested or audited.
Are there any other type of cost for defective products?
Yes, besides prevention and appraisal cost, scrap cost will also incur from manufacturing defectives products. Scrap cost refers to material wasted due to production processes not meeting specifications or customers' requirements.
How can organizations reduce non-quality cost?
Organizations can reduce NQC through effective planning, organizing resources correctly,' right first time' philosophies in production processes/systems as well as prior inspection of goods prior dispatch etc
Does non-quality cost benefit organizations?
Yes it does, reducing non-quality cost helps organizations remain competitive in today's markets and aids in maintaining long term customer relations while at the same time keeping them ahead of competition. It also ensures that companies save money by eliminating waste from their operations which would otherwise be passed on through higher prices for goods and services.
Final Words:
The key takeaway from non quality cost (NQC) is that it must be properly addressed within an organization so as not to adversely impact its bottom line financial performance. By understanding how each category of NQC operates, companies are better able to create a sound strategy for mitigating these types of losses in order minimize their overall financial impacts on profits and operations.