What does MRP mean in US GOVERNMENT
MRP stands for Manufacturing Resource Planning. It is a system used by manufacturing companies to optimize their production processes and delivery of materials. MRP helps organizations manage their resources more efficiently and track the progress of jobs in the production line. The system makes use of data from production orders, inventory levels, material requirements, customer orders, and bills of materials (BOMs). With this data, companies can plan for material procurement and manufacturing activities, reducing the risk of lost or idle resources. MRP systems have become an essential tool for streamlining production processes and increasing efficiency in manufacturing environments.
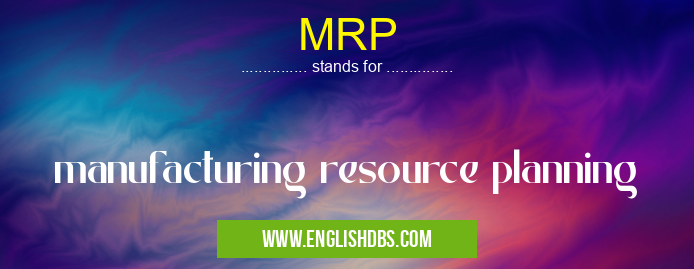
MRP meaning in US Government in Governmental
MRP mostly used in an acronym US Government in Category Governmental that means manufacturing resource planning
Shorthand: MRP,
Full Form: manufacturing resource planning
For more information of "manufacturing resource planning", see the section below.
What Does MRP Mean?
Manufacturing Resource Planning is an integrated process that acts as a bridge between operations planning and execution (executing the plans to get the job done). Through its integration with several systems within an organization, it takes into account all factors that affect production such as capacity constraints, material availability, labor requirements, scheduling priorities, order sequencing and transportation costs. This allows businesses to strategically plan ahead while taking into consideration all relevant aspects of a manufacturing environment. By doing so it optimizes both the time taken to complete a project as well as total costs incurred in its completion. In essence, MRP helps manufacturers fulfill customer needs quickly and accurately while staying cost-effective.
How It Works
MRP works by analyzing data from various sources such as sales forecasts, BOMs (Bill Of Materials) and inventory levels to create detailed production plans (known as master schedules) which form the basis for creating work orders for each product component or sub-component being manufactured. Depending on your company’s internal structure this may include generating purchase orders for raw materials or vendor parts required for day-to-day operations etc., then passing these onto purchasing departments where they can be tracked via other functional departments like accounts payable/receivables to ensure payment processes are running smoothly at all times etc., before sending them out for delivery if required or placing them on backorder until sufficient stock levels are met etc., enabling better control over lead times throughout the entire supply chain process etc.. Once all related information has been gathered it is then up to you to decide how best you can utilize your staffs skills sets & capacities along with specific company policies & procedures from start to finish within each individual operation or job ensuring maximum efficiency throughout every stage of your supply chain process!
Benefits Of Implementing MRP:The implementation of a Manufacturing Resource Planning System will bring numerous benefits including increased visibility across your entire supply chain; improved accuracy in forecasts based on historical demand patterns; reduced lead time through an optimized purchasing system; simplified ordering processes resulting in fewer mistakes; enhanced communication across departments; improved customer service due to decreased waiting period between order receipt & delivery; effective resource utilization resulting in greater operational efficiency & optimized inventory management minimizing potential losses due to overstocks or understocks etc.. All these advantages ensure that companies will not only make better decisions based on accurate data but also experience higher productivity rates leading ultimately towards greater profitability margins!
Essential Questions and Answers on manufacturing resource planning in "GOVERNMENTAL»USGOV"
What is MRP?
Manufacturing resource planning (MRP) is a computer-based production planning and inventory control system used to manage manufacturing processes. It consists of software that uses bill of materials and inventory data to calculate the requirements for production, scheduling orders, and purchasing of materials needed.
What are the Benefits of an MRP System?
An MRP system can help businesses reduce their production costs, eliminate redundancies in production processes, and optimize inventory levels. Additionally, an MRP system facilitates communication between the different departments within an organization as it provides a central platform for exchanging data.
How does an MRP System Work?
An MRP system utilizes input from sales orders and forecasts to create a master schedule that guides the production process. It also tracks demand for raw material demands as well as current stock levels, so that procurement activities can be managed effectively. The system then generates reports on inventory levels and optimization opportunities in order to provide insights into how well the supply chain is performing.
How Can You Implement An MRP System?
Before you start implementing an MRP system, you need to make sure that your business’s internal data is up-to-date and accurate. This includes product information, customer details, item availability, supplier/vendor relations, etc. Once your data is ready, you can select a software package suitable for your business size and industry needs and start setting up the system by defining settings such as user profiles or access rights.
What Is BOM in an MRP System?
A bill of materials (BOM) is a list of all components required for producing a certain product which must be managed by an MRP system. It includes information about each component such as its quantity required per unit produced or total cost per unit including taxes or discounts provided by suppliers. This enables effective management of inventory while ensuring on-time delivery to customers through accurate tracking of available parts.
How Do You Choose an Suitable ERP Solution?
Choosing a suitable Enterprise Resource Planning (ERP) solution requires careful consideration based on factors such as scalability, user experience design, customization options offered by vendors or cloud compatibility with existing IT infrastructure. Additionally, thorough research should be conducted on various solutions available in the market to determine which one fits best with business requirements before making any decision.
MRP also stands for: |
|
All stands for MRP |