What does MRCA mean in GENERAL
MRCA stands for Material Review and Corrective Action, and it is a process used in business to ensure that the quality of materials used in production is up to code. This review process includes both the evaluation and correction of any issues regarding authorized material. It is a preventative measure taken to avoid any potential quality issues further down the production line, which could result in significant financial losses. MRCA ensures that businesses are using only high-quality materials so they can produce products with high standards. In this article, we will discuss what MRCA is, how it helps businesses maintain quality control over their production processes, and the importance of implementing this system in organizations.
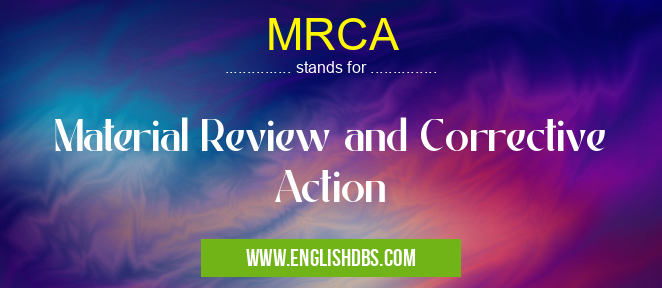
MRCA meaning in General in Business
MRCA mostly used in an acronym General in Category Business that means Material Review and Corrective Action
Shorthand: MRCA,
Full Form: Material Review and Corrective Action
For more information of "Material Review and Corrective Action", see the section below.
Importance of an MRCA System
Having a properly implemented Material Review and Corrective Action system in place ensures that businesses use only high-grade materials during their production processes without compromising on quality standards. Companies can also benefit from increased efficiency due to improved detection times resulting from early visibility into potential problems with components or parts from suppliers – meaning quicker corrections without sacrificing uptime or efficiency levels on other projects. Furthermore, with real-time feedback from customers using these products companies can track trends easier while providing greater customer satisfaction through improved product quality assurance overall – resulting in higher loyalty rates among customers.
Essential Questions and Answers on Material Review and Corrective Action in "BUSINESS»GENERALBUS"
What is MRCA?
MRCA stands for Material Review and Corrective Action. It is a process of evaluating a product or material to ensure it meets customer quality standards and specifications. The process helps identify potential issues, prevent reoccurring problems, and maintain or improve customer satisfaction.
How often should MRCA take place?
The frequency of an MRCA review depends on the type of material being evaluated and any applicable industry standards. An MRCA should be conducted as needed or recommended by the customer to ensure quality standards are consistently met.
Who is responsible for initiating an MRCA?
Typically, the supplier initiates an MRCA when there are potentially nonconforming parts or materials that need to be assessed and resolved before continuing with production.
What information should be included in an MRCA?
An MRCA should include all relevant details related to the product or material being inspected including supplier data, part/material numbers, drawings, photos and other pertinent documents. Additionally, it should include a description of the issue identified, corrective action taken and verification of corrective actions effectiveness.
What types products typically require an MRCA?
Any products that may not meet certain quality requirements or have defects can benefit from an MRCA review for further assessment and improvement plan recommendations. Commonly used materials such as plastics, metals, rubber products and electronics items may all require inspection before production can continue.
Who conducts an MRCA review?
Depending on the complexity of the situation and the expertise required to diagnose the issue(s), various personnel may be involved in conducting an MRCA review such as supervisors, engineers, inspectors or analysts with experience in related fields.
Is there a specific methodology used when conducting an MRCAs?
Yes – problem solving tools such as Root Cause Analysis (or 8D) are commonly used during the evaluation process to determine root causes of product issues so effective corrective actions can be implemented accordingly.
How does implementing changes help prevent future problems from occurring?
Implementing changes recommended by an external professional following a thorough investigation into a product’s performance can help identify weak areas in design which may cause re-occurring problems going forward. Making improvements based on this feedback will make sure products meet quality standards each time they are produced efficiently.
Are there any benefits associated with conducting regular MRAs?
Yes – performing regular MRAs ensures minimal rework costs over time due to faulty materials early on in production stages; increases customer satisfaction through reliable delivery times; minimizes disruptions caused by technical defects; improves safety standards by adhering to regulations; and enhances customer relationships through increased trust.
Should MRAs be documented for audit purposes?
Yes - It is important to document every step taken during a Material Review & Corrective Action process so that it can be easily accessed when needed for auditing purposes.
Final Words:
Overall, Material Review and Corrective Action systems are essential for maintaining quality control over any company's production processes while also improving efficiency levels along the way – creating greater customer satisfaction through consistent product reliability as well as reducing costs related to wastage or expensive repairs post-production implementation. From engineering change request management through supplier audits all the way up to nonconforming part replacement – having such a system in place offers various benefits for businesses by ensuring only traceable components are utilized in all stages of development while also allowing for quick issue resolution times if required.