What does MPS mean in MANUFACTURING
MPS stands for Master Production Schedule. It is an important tool in the production process that helps to manage operations, resources, and materials in any production facility. MPS is a system used to create schedules for producing goods and services based on customer orders, forecasts, inventory management objectives, and other factors. By creating an efficient plan of action with MPS, facilities can maximize their utilization of resources while meeting customer demand and other operational goals.
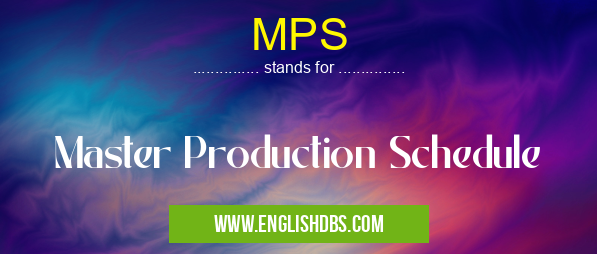
MPS meaning in Manufacturing in Miscellaneous
MPS mostly used in an acronym Manufacturing in Category Miscellaneous that means Master Production Schedule
Shorthand: MPS,
Full Form: Master Production Schedule
For more information of "Master Production Schedule", see the section below.
Definition
MPS (Master Production Schedule) is a planning tool for manufacturing companies that details the production process of goods or services. It outlines the quantity and timing of workflows that need to be completed in order to deliver a product or service according to customer orders and available resources. The MPS also informs the scheduling of materials, labor forces, and equipment so that operations run smoothly without delay or disruption.
Utilization
MPS plays a vital role in optimizing operations in many industries. By allowing organizations to accurately plan their activities, it reduces waste from overproduction as well as underutilized resources. With this system in place, business owners can better manage their supply chain by tracking current inventory levels, knowing when lead times begin for orders that are placed out-of-stock, forecasting future sales demands and allocating enough capacity to keep up with orders received. This allows them to make decisions ahead of time to increase efficiency in meeting deadlines while keeping costs down by avoiding unnecessary deliveries or stockouts.
Benefits
The use of MPS has many benefits including improved on-time delivery rates; cost savings due to increased production efficiencies; decreased inventory levels resulting from improved forecasting; simplified coordination between departments; minimized downtime caused by poor planning decisions; improved relations between customers & suppliers due to accurate ordering & delivery processes; decreased risk related to quality issues arising from inadequate planning & scheduling techniques; increased profitability because of better usage of resources & capabilities; reduced errors & delays associated with unforeseen changes or conditions; and improved employee morale due to increased job satisfaction & recognition through successful accomplishment of objectives.
Essential Questions and Answers on Master Production Schedule in "MISCELLANEOUS»MANUFACTURING"
What is an MPS?
A Master Production Schedule (MPS) is a plan used by production and operations managers to identify and schedule the delivery of finished goods. It contains detailed information on all required products such as production quantities, delivery dates, inventory levels, and any other relevant details. The MPS helps ensure that resources are allocated efficiently to meet customer demand.
What is the purpose of an MPS?
The primary purpose of an MPS is to coordinate and optimize the available resources in order to meet customer demand. By having an accurate view of what materials need to be manufactured based on customer orders, and when they must be delivered, companies can ensure that they don’t have too much or too little inventory stored away at any time.
How often should an MPS be updated?
An MPS should be updated regularly in order to ensure its accuracy. As customer orders come in or change, it’s essential that those changes are reflected in the MPS so that everyone involved in the manufacturing process has up-to-date information about what products need to be made and when they must be delivered.
What happens if an MPS isn’t updated regularly?
If the information contained in an MPS isn’t kept up-to-date, it can lead to confusion throughout the manufacturing process as everyone involved may not have access to accurate information about what needs to be done and when it needs to be done by. This can lead to bottlenecks in production, missed deadlines and frustrated customers.
Who uses an MPS?
An MPS is typically used by multiple departments within a company including production managers, purchasing agents, operations managers, material planners and suppliers. All these parties use the data contained within an MPS for their respective jobs including ordering materials needed for production or managing resources allocated for specific projects.
What systems are commonly used for developing an MPS?
Companies often use specialized software solutions designed specifically for creating master production schedules. Some ERP systems also come with built-in modules for planning purposes which allow users to create accurate projections based on current customer demand trends as well as future order forecasts. Some Excel templates are also available which can provide a basic level of planning capabilities which might suit smaller organizations with simpler operations better than complex software solutions or ERP toolsets.
How does an MRP system fit into using an MPS?
An Material Requirements Planning (MRP) system complements the use of an M PS by providing a way for users to accurately calculate how much material they will need based on expected product demand projected from Master Production Schedules created with this system or other sources like spreadsheets or specialized scheduling software applications. This helps organizations maintain higher levels of inventory while still staying up-to-date with regards to what materials need to be produced at any given time.
Final Words:
MPS is an invaluable tool for any manufacturing business looking to streamline their operations and ensure accurate production schedules while still meeting customer needs. It provides a powerful platform for long-term planning that helps prevent unplanned disruptions throughout the entire production process while promoting resource optimization across multiple departments within an organization’s supply chain network. With all the benefits associated with using this system effectively, it is no wonder why more businesses are turning towards MPS than ever before.
MPS also stands for: |
|
All stands for MPS |