What does AQE mean in OCCUPATION & POSITIONS
Advanced Quality Engineer (AQE) is a specialized role within the quality engineering field. AQEs are responsible for leading initiatives and providing expertise to ensure that products and services meet the highest standards of safety, reliability, and performance. They analyze data, develop testing plans, conduct audits, evaluate test results, document findings, and recommend improvements. The AQE is an integral part of the quality assurance process and often works with other departments such as research and development to ensure product quality.
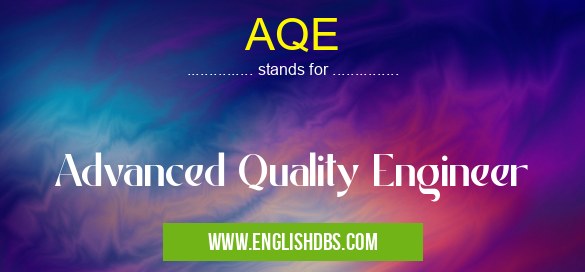
AQE meaning in Occupation & Positions in Business
AQE mostly used in an acronym Occupation & Positions in Category Business that means Advanced Quality Engineer
Shorthand: AQE,
Full Form: Advanced Quality Engineer
For more information of "Advanced Quality Engineer", see the section below.
Role & Responsibilities
Advanced Quality Engineers are responsible for ensuring that products meet industry standards of excellence in terms of safety, functionality, quality, reliability, and performance. They develop test plans to assess the performance of products; analyze data; conduct audits; evaluate test results; report findings; recommend improvements; proactively identify potential risks or issues before they become problems during production; train personnel on proper procedures related to inspections; document best practices for product quality control programs and procedures; maintain records on corrective actions taken from customer feedbacks or complaints; handle customer grievances pertaining to products or services.
Skills & Qualifications
Advanced Quality Engineers should possess excellent organizational skills along with strong analytical skills to be able to interpret complex data sets. An ability to think critically in order to solve problems quickly is essential as well as a proven understanding of good engineering practices. Proficiency in programming languages such as Java or C# is also beneficial. A bachelor’s degree in engineering or related field is typically required along with certifications related to quality standards development such as Six Sigma Green Belt/Black Belt certification from ASQ. Experience in auditing processes involving ISO 9001 and/or ISO 14000 standards would be advantageous too.
Essential Questions and Answers on Advanced Quality Engineer in "BUSINESS»POSITIONS"
What is an Advanced Quality Engineer?
An Advanced Quality Engineer is a specialized role in the field of quality assurance engineering. They are responsible for developing and overseeing processes that ensure products meet customer requirements, standards, and regulations. They work to ensure that all products meet safety and performance standards, as well as ongoing support activities such as inspections and problem resolution.
What qualifications are required to become an Advanced Quality Engineer?
Generally, a bachelor’s degree in engineering or a related field is necessary to become an Advanced Quality Engineer. In addition, some employers may require applicants to have prior experience in quality assurance or experience working with complex systems.
What skills do I need to possess as an Advanced Quality Engineer?
As an Advanced Quality Engineer, you should be highly analytical with strong problem-solving skills; have excellent oral and written communication abilities; be able to develop clear processes; manage various components of projects; and stay up-to-date on industry trends.
What type of environment do Advanced Quality Engineers typically work in?
Advanced Quality Engineers typically work in industrial environments but may also oversee operations in office settings. The job requires long hours spent completing paperwork or analyzing data on computers, as well as time spent interacting with suppliers and customers.
How can I ensure successful quality assurance implementations?
A successful quality assurance implementation relies heavily on teamwork between all stakeholders within the organization such as engineers, production personnel, management personnel etc. It is important to communicate regularly throughout the process to ensure project deadlines are met while still ensuring high levels of product quality are achieved. It is also important that proper documentation and reports are compiled at each stage of the process so issues can be identified quickly and efficiently resolved.
What strategies can I use to improve product quality?
To improve product quality, it’s important that processes are documented thoroughly and followed consistently across all production stages. Regularly assess processes using inspection techniques such as visual inspection or dimensional measurements. Perform root cause analysis for any nonconformances discovered through this process. Additionally, review customer feedback regularly so any changes can be made quickly if needed.
How can I identify potential supply chain problems?
Supply chain problems can arise from a variety of causes which could include material shortages or delays during transportation. To identify these potential problems it’s important to monitor supplier activity closely by performing regular supplier audits or assessments of their performance metrics over time so any potential issues can be identified early.
What methods do I use for statistical process control (SPC)?
Statistical Process Control (SPC) is a method used by many organizations to analyze outputs from production lines in order to identify areas for improvement in terms of production speed, product defects or costs associated with achieving certain outputs. This is done by collecting data on specific processes over time which then allows analysts to detect anomalies which would indicate there are areas needing further investigation.
How do I perform preventative maintenance best practices?
Preventive maintenance best practices involve regularly scheduled inspections on equipment coupled with repairs if needed before they escalate into more serious issues down the line. Establishing preventive maintenance plans along with spare parts inventories will help ensure equipment goes uninterrupted for longer periods of time thus reducing machine downtime.
What tactics should I use when investigating customer complaints?
Investigating customer complaints requires both technical knowledge but also interpersonal skills including empathy while addressing concern raised by customers during inquiries such as reaching out via phone calls or emails promptly after receiving notice about their complaint; listening attentively; having patience when handling queries from customers; providing timely follow up information regarding resolution status etc.[END
Final Words:
The Advanced Quality Engineer plays a critical role in ensuring overall product satisfaction by working closely with other teams like Research & Development (R&D), Production Planning & Control (PPC), Sales Team etc., to ensure that all components adhere strictly to industry accepted norms & standards so that customers receive only top-notch end-products with utmost satisfaction guarantee after its launch into the market. This position requires analytical aptitude coupled with experience in relevant fields so the candidate must possess a genuine interest in learning more about technical subject matters if they wish to pursue this career path successfully.
AQE also stands for: |
|
All stands for AQE |