What does MDA mean in MANUFACTURING
Manufacturers strive to improve the quality of their products and services by monitoring defects to identify potential issues. Manufacturing Defects Analyses (MDA) is a method used by manufacturers to accurately measure and track defects in order to prevent them from occurring in the future. This article will provide an overview about MDA, as well as answer common questions about this process.
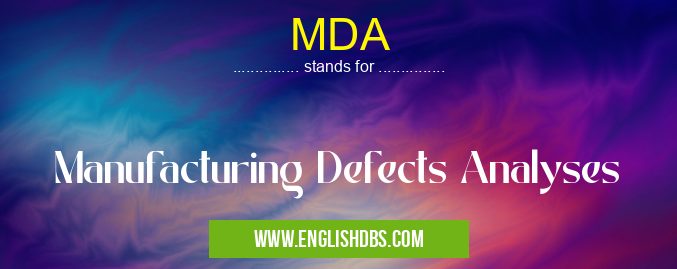
MDA meaning in Manufacturing in Miscellaneous
MDA mostly used in an acronym Manufacturing in Category Miscellaneous that means Manufacturing Defects Analyses
Shorthand: MDA,
Full Form: Manufacturing Defects Analyses
For more information of "Manufacturing Defects Analyses", see the section below.
Essential Questions and Answers on Manufacturing Defects Analyses in "MISCELLANEOUS»MANUFACTURING"
What is Manufacturing Defects Analyses?
Manufacturing Defects Analyses (MDA) is a form of quality control that assesses defects across a manufacturing process in order to prevent them from occurring in the future. The goal of MDA is to identify and quantify any existing problems, then develop strategies for eliminating those problems and preventing their recurrence.
What types of data are considered when conducting MDA?
When performing MDA, manufacturers use data such as customer complaints, product returns, product testing results, production records, and warranty claims. The data collected helps identify areas where improvement can be made, such as defect types and frequencies, root causes of defects, problem components or processes within the manufacturing cycle.
How does MDA improve product quality?
By analyzing the collected data from defects across the entire manufacturing process, manufacturers can pinpoint areas for improvement and make adjustments accordingly. These improvements could include changes in design or processes related to production or assembly line operations that would help ensure better quality products for customers going forward.
Are there any challenges associated with conducting MDA?
Yes, there are several challenges that can arise during an MDA audit. Some of these challenges include inadequate documentation tracking of prior occurrences of similar defects; human errors; inappropriate management decisions; and slow response times to identified issues. Additionally, it can take time and resources to properly research and analyze all data collected correctly before taking corrective action.
What are some best practices for this type of analysis?
Best practices for performing an effective MDA include establishing clear communication between departments; developing protocols for handling claims; documenting processes thoroughly; regularly examining reported complaints; creating a detailed database system; training personnel properly on proper inspection techniques; documenting procedures consistently; actively pushing forward project initiatives quickly once identified problems have been resolved; following up on problems promptly after they have been addressed should they appear again.
Final Words:
In conclusion, manufacturers who utilize Manufacturing Defects Analysis (MDA) are able to find problems within their manufacturing cycles more efficiently than if these investigations were left unguided or inadequately monitored. With careful attention paid towards collecting accurate data from customer feedback surveys along with other forms of customer interaction such as returns/exchanges or warranties/guarantees —— manufacturers can create a quality working environment that ensures a greater level of satisfaction among its customers year after year.
MDA also stands for: |
|
All stands for MDA |