What does LSA mean in MILITARY
Logistics Supportability Analysis (LSA) is a process used by governmental entities to evaluate the ability of its operational logistics assets and networks to meet current and future demands. It helps in the identification of any gaps between current operations and desired objectives, and thus enables allocation of resources in the most efficient way. This ensures that all relevant stakeholders are well informed about the situation before making decisions on resource allocation, personnel assignments, and program objectives. The effectiveness of this process is what makes it so important when it comes to decision-making within governmental organizations.
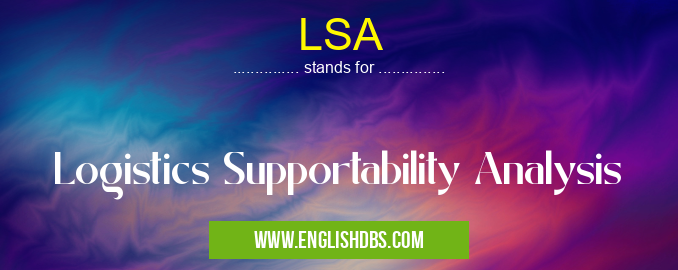
LSA meaning in Military in Governmental
LSA mostly used in an acronym Military in Category Governmental that means Logistics Supportability Analysis
Shorthand: LSA,
Full Form: Logistics Supportability Analysis
For more information of "Logistics Supportability Analysis", see the section below.
» Governmental » Military
Definition
Logistics Supportability Analysis (LSA) is a systematic process which involves gathering data from various sources in order to assess an organization's overall operational logistics capability. This allows comprehensive understanding of existing supply chain structures, capabilities and bottlenecks leading to more informed decision-making regarding resource allocations, personnel deployments, program objectives and other related activities. The LSA approach also facilitates better integration across multiple levels within the organization such as planning & procurement functions. A thorough review of supply chains will help identify risks associated with possible disruptions or failures as well as potential for improvement through refinement or reorganization of resource allocations.
Benefits
The primary benefit of Logistics Supportability Analysis is improved decision making due to better visibility into an organization’s logistic operations. This heightened awareness leads to more informed decisions that can reduce duplication while ensuring efficiency with limited resources. Furthermore, it can also help identify potential weaknesses or redundancies within the system that would otherwise have gone unnoticed until too late. Additionally, it facilitates a better understanding between different branches within an organization allowing for greater collaboration among them; this increases overall responsiveness and requires fewer resources than if each branch operated independently. In this way LSA encourages smarter approaches overall strategies that improve performance outcomes while reducing costs over time.
Essential Questions and Answers on Logistics Supportability Analysis in "GOVERNMENTAL»MILITARY"
What is Logistics Supportability Analysis?
Logistics Supportability Analysis (LSA) is a comprehensive and structured analytical process to ensure that the support system for an item meets operational requirements in an efficient and cost-effective manner. It looks at the ability of the logistics infrastructure to meet performance, availability, maintenance, safety and other customer requirements.
What does Logistics Supportability Analysis involve?
Logistics Supportability Analysis involves the analysis of data such as failure rates, maintenance costs, life cycle costs, spare parts inventory levels and operational availability. The outcome of this analysis then informs decisions regarding the adequacy or required changes to be made in order to ensure that the system will be able to support its intended operations.
Who should perform a Logistics Supportability Analysis?
Logistics engineers who are specifically trained in this field should ideally perform LSA's. They are knowledgeable in the various elements of logistics support systems and can provide a comprehensive assessment using hard data and evidence-based decisions.
When should a Logistics Supportability Analysis be conducted?
LSA's should generally be conducted before a new item is introduced into the system in order to identify potential issues prior to committing resources into manufacturing or procurement activities. It can also be carried out during operation when performance goals are not being met or when new equipment is going to be added on top of existing infrastructure.
How often should a Logistic Supportability Analysis be done?
This depends on how often changes are made to the system or if unexpected issues are encountered which require further investigation into logistics needs. Generally speaking, LSAs should be conducted once initially before an item goes into service plus any additional times if modifications or additions are made throughout its life cycle.
What types of data do you need for a Logistic Supportability Analysis?
The type of data needed depends on what type of analysis needs to be performed but usually includes things like failure rates, operating costs, spare parts inventory levels and other related information about each component in the system. Any information which can give insight into potential problems or areas where more resources might need to be allocated can help inform decisions related to LSA’s.
What factors must we consider when conducting a LSA?
When conducting a LSA some factors that must be considered include performance requirements, availability targets, maintenance operations plan objectives and safety considerations. Additionally it may also cover topics such as cost constraints and training needs depending on what type of system it is being applied too.
How can we ensure that our logistical operations are meeting our performance goals?
Conducting regular LSAs helps identify any areas which may need improvement so that corrective action can be taken in order to better meet performance targets over time. Additionally looking at factors such as supplier performance ratings and customer feedback may also give insight in how well logistical operations are performing.
Final Words:
Logistics Supportability Analysis (LSA) is a critical tool for helping organizations evaluate their readiness for meeting current needs as well as preparing them for future demands; it does this by providing insights into current supply chain lineups, capabilities available at different stages throughout a process as well as weaknesses in resources needed for successful delivery of services or products. By facilitating better collaboration between branches/functions within an organization it improves efficiency while cutting down on costs; these two factors combined make LSA essential when analyzing how best to allocate resources both now and in preparation for future developments.
LSA also stands for: |
|
All stands for LSA |