What does LMO mean in UNCLASSIFIED
LMO stands for Low Metal Operation, which is a type of manufacturing process used to produce parts and products without the use of heavy metals. By using lightweight and non-metallic materials like composite plastics, LMO operations can produce parts in a much more cost effective manner than the traditional method of using heavy metals. This type of operation is becoming increasingly popular due to its ability to reduce overhead costs and promote environmental sustainability.
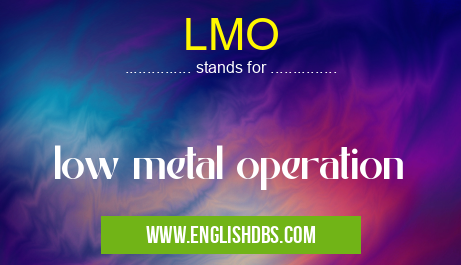
LMO meaning in Unclassified in Miscellaneous
LMO mostly used in an acronym Unclassified in Category Miscellaneous that means low metal operation
Shorthand: LMO,
Full Form: low metal operation
For more information of "low metal operation", see the section below.
What is Low Metal Operation?
Low Metal Operation (LMO) is a type of manufacturing that uses lightweight, non-metallic materials such as composite plastics instead of heavy metals. The process works by combining multiple layers of different materials with properties such as strength, flexibility, insulation or electrical conductivity to create one piece that can be used for a variety of purposes. It eliminates the need for expensive metal parts and reduces overall material costs by significantly decreasing weigh and processing time. This technique has been used for years in the aviation industry but has since become more popular in other industrial sectors thanks to its cost effectiveness, efficiency and potential for reducing overhead expenses.
Advantages
The primary benefit of Low Metal Operations is cost savings due to reduced materials while still meeting product performance requirements. By eliminating metal components from the production line it reduces both the weight and cost associated with producing those components or products. Additionally, many companies are shifting towards this production style in an effort to reduce their environmental impact by lessening their use of resources. LMOs are also beneficial because they often require fewer steps than traditional methods meaning faster production times which leads to quicker returns on your investments.
Essential Questions and Answers on low metal operation in "MISCELLANEOUS»UNFILED"
What is low metal operation?
Low metal operation (LMO) is a process used in manufacturing and engineering to create parts from metal that requires minimal machining and finishing. It involves cutting, grinding, and welding metal components with predetermined tolerances. This process is often utilized in the aerospace industry due to the complex shapes and delicate nature of aircraft components.
What are the benefits of using LMO?
The primary benefit of using LMO is that it allows for a faster turnaround time on projects as fewer steps in the production process are required. Additionally, it can yield greater precision when compared to traditional machining methods while also providing cost savings as less material needs to be processed.
Are there any special considerations I should take into account when performing an LMO operation?
Yes, it's important to ensure that all materials being used in an LMO operation meet quality control standards prior to starting the process. Any deformities or imperfections should be attended to before proceeding, as these can result in faulty parts or incorrect results. Additionally, proper safety precautions should always be taken during any type of welding work.
Can an LMO operation be automated?
Yes, many processes associated with LMO operations can be automated such as cutting and grinding. However, depending on the complexity of the task at hand some manual input may still be required even with automation enabled.
Is there a certain type of machinery necessary for performing an LMO operation?
Yes, specialized machinery such as lathes or CNC machines are typically needed for carrying out complex tasks like grinding and cutting metals into shapes with specific dimensions. These machines must be calibrated correctly prior to use for optimal results.
How often should equipment used for LMO operations be inspected?
Equipment used for LMO operations should undergo regular inspections every 6-12 months depending on usage frequency and intensity levels. Routine maintenance should also be conducted regularly between inspections for optimal performance outcomes.
How do I dispose of waste created from an LMO operation?
Waste products generated from an LMO operation must be handled according to local regulations regarding hazardous materials disposal such as shavings or oils coolants used during machining tasks or alloys you may have welded or cut apart; contact your local government offices for further guidance if needed..
Does experience play a role when performing an LMO procedure?
Yes, having experience with similar procedures will help provide better results by allowing you to anticipate potential problems before they arise while giving you more confident decision making capabilities when working on a project requiring intricate details or highly precise parts.
Are there any special considerations I need to take into account when choosing materials for my project?
Yes, each type of material has its own set of characteristics which means choosing what's best suited for your project requires careful consideration; factors such as corrosion resistance, tensile strength, thermal conductivity all need to weigh into your decision making process based upon your desired outcome.
Final Words:
Low Metal Operations provide businesses with an eco-friendly alternative for producing parts and products at lower costs with improved efficiency. By utilizing lightweight and non-metallic substances like composite plastics it makes it possible to drastically reduce equipment costs while also promoting sustainability which can provide long term benefits for your organization financially and environmentally. With all these advantages it's no surprise why so many companies have started utilizing LMOs in their production lines today.
LMO also stands for: |
|
All stands for LMO |