What does L&E mean in MANUFACTURING
L&E stands for Lean and Efficient. This term is used widely in the business world to describe an organization's attempts to streamline its processes to reduce costs, increase efficiency and work smarter.
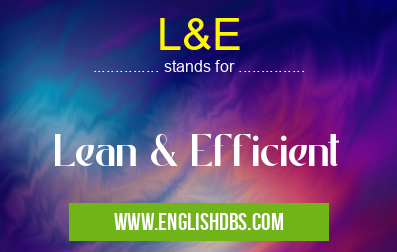
L&E meaning in Manufacturing in Miscellaneous
L&E mostly used in an acronym Manufacturing in Category Miscellaneous that means Lean & Efficient
Shorthand: L&E,
Full Form: Lean & Efficient
For more information of "Lean & Efficient", see the section below.
Essential Questions and Answers on Lean & Efficient in "MISCELLANEOUS»MANUFACTURING"
What does L&E mean?
L&E stands for Lean and Efficient. It is used to describe an organization's attempts to streamline their processes for greater efficiency.
How does L&E help organizations?
Working in a lean and efficient manner helps organizations reduce costs, improve operational efficiencies, optimize resources, and create a better customer experience.
What are some of the benefits of implementing L&E?
Some of the main advantages of implementing L&E include reducing production costs, improving quality control, shortening turnaround times on projects, increasing customer satisfaction through improved service levels, and enhancing employee engagement.
Does any specific framework need to be followed when pursuing L&E initiatives?
While there is no one-size-fits-all framework that must be followed when pursuing lean and efficient initiatives, there are some guidelines that should be considered such as waste reduction strategies, process improvement initiatives, and employee engagement tactics.
Who can benefit from adopting an L&E approach?
Organizations of all sizes can benefit from adopting an L&E approach as it allows them to improve the way they operate while also reducing expenses. Additionally, employees within the organization may notice increased job satisfaction due to improved workflow processes.
Final Words:
Implementing a lean and efficient approach can bring numerous benefits to organizations by helping them operate more smoothly while lowering costs at the same time. However, it's important to keep in mind that there is no single framework that needs to be followed when pursuing this type of initiative; each organization should assess their own needs and develop a plan accordingly.