What does KYK mean in UNCLASSIFIED
KYK is an abbreviation for Kiken Yochi Katsudo, a Japanese term that translates into English as ‘The Implementation of Risk Reduction Measures’. KYK is used in the context of Japanese industrial and safety regulation to describe the process whereby companies must implement measures to prevent disasters or catastrophes from occurring. The regulations state that companies shall put into place high levels of awareness, training, preparation and implementation of preventive measures to minimize risks in their operations. KYK focuses on risk management and provides organizations with a framework to ensure the safety of its employees, customers and other stakeholders.
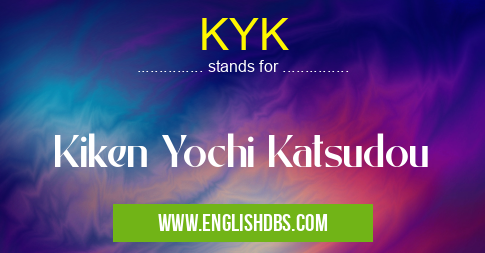
KYK meaning in Unclassified in Miscellaneous
KYK mostly used in an acronym Unclassified in Category Miscellaneous that means Kiken Yochi Katsudou
Shorthand: KYK,
Full Form: Kiken Yochi Katsudou
For more information of "Kiken Yochi Katsudou", see the section below.
Meaning
KYK is an acronym for Kiken Yochi Katsudo which means "Risk Reduction Measures" in Japanese. It is a system of risk assessment and risk reduction guidelines set by the Japanese government that all industrial-level organizations are expected to follow in order to protect both employees and customers from potential risks associated with their operations. This includes the implementation of preventive measures such as safety inspections, proper maintenance, emergency plans, etc., which requires extensive training programs for employees as well as managers. KYK also outlines specific actions that must be taken if an organization fails to comply with these regulations or fails to take necessary precautions before any hazardous event occurs.
Full Form
KYK stands for Kiken Yochi Katsudo, which literally translates into English as "The Implementation of Risk Reduction Measures". KYK is a comprehensive system established by the Japanese government in order to ensure the safety of all industrial activities throughout the nation. It comprises various policies and procedures aimed at reducing potential accidents or disasters related to any industry sector or business activity. The key elements involved in KYK include designing effective organizational systems designed specifically for risk prevention; providing proper information about products and services; implementing appropriate safety management systems; creating strict guidelines regarding hazardous operations; ensuring regular inspections; conducting proper maintenance practices; instituting emergency plans; and establishing effective customer service protocols among many others.
What Does KYK Stand For?
KYK stands for Kiken Yochi Katsudo which translates into English as ‘The Implementation of Risk Reduction Measures’. KYK is a comprehensive system established by the Japanese government in order to ensure the safety of all industrial activities throughout the nation. It comprises various policies and procedures aimed at preventing potential accidents or disasters related to any industry sector or business activity while working towards fostering sound operational relationships between employers, employees, customers, suppliers and other stakeholders.
Essential Questions and Answers on Kiken Yochi Katsudou in "MISCELLANEOUS»UNFILED"
What is Kiken Yochi Katsudou?
Kiken Yochi Katsudou (KYK) is a Japanese risk management system that encourages workers to proactively identify and address potential safety hazards in the workplace. This system is based on the Japanese Safety and Health Act of 1972, which requires employers to promote safe and secure working conditions for their employees. KYK puts an emphasis on employee education, training, and communication to ensure that workers are aware of safety risks.
How does Kiken Yochi Katsudou work?
KYK consists of three steps: identification of hazards, assessment of risks associated with those hazards, and implementation of corrective measures to reduce or eliminate those risks. First, using its own structured approach or methods from other organizations such as Occupational Safety & Health Administration (OSHA), employees identify potential workplace hazards. Next, employers assess the severity of the identified hazard and decide what action should be taken to mitigate it. Finally, employers implement corrective measures to reduce or eliminate any identified safety risks.
What are some common workplace hazards covered by Kiken Yochi Katsudou?
Common workplace hazards covered by KYK include slip/trip/fall injuries due to wet floors; fire and burn injuries caused by malfunctioning electrical appliances; improper lifting techniques resulting in musculoskeletal disorders; exposure to hazardous chemicals; contact with sharp objects; use of defective machinery; and unsafe driving practices while operating company vehicles.
What tools are used for identifying hazards under Kiken Yochi Katsudou?
To identify workplace hazards under KYK, employers can utilize tools such as checklists and worksite assessments to observe how employees interact with their environment and identify any potential dangers within it. Additionally, employees can also submit hazard reports if they see something dangerous or unsafethat they may have missed during the initial observation period. This provides employers with an extra level of assurance that all potential threats are being identified and addressed promptly.
How can businesses ensure compliance with Kiken Yochi Katsudou standards?
Businesses should ensure that their employees are properly trained in KYK guidelines so that they know how to recognize a potential hazard in the workplace before it becomes an issue that requires emergency attention. Additionally, employers should conduct regular worksite assessments as well as upon obtaining worker complaints about safety concerns in order to monitor compliance with this system’s standards proactively. Furthermore, businesses should consider implementing a third-party audit program for additional assessment support.
What kind of training is necessary for compliance with Kiken Yochi Katsudou standards?
Employers must provide staff members responsible for KYK activities suitable training in order to comply with its standards. During this training process, these individuals should become familiarized with risk management principles as well as everyday scenarios where safety incidents could occur in the workplace due to negligence or ignorance concerning such matters.
Who is responsible for enforcing Kiken Yochi Katsudou regulations?
The Japanese government has assigned the responsibility of enforcing KYK regulationsto local labor authorities throughout Japan who can inspect worksites on behalf of employers at any time if they deem there is sufficient cause for doing so.
: How often do workplaces need inspection accordingto KykenYochiKatshudo conventions?
: Accordingto Kyken Yochi Katshudo regulations workplaces must be inspected regularlyand adequately throughout every year depending uponany newlyestablished industrial activityor changein existingoperations.
: Does KkenYoshiKatushuodimplyemployeesmust wearprotectiveequipment whenworkingina hazardousenvironment?
: Yes,employeesare requiredtoprotect themselvesaccordingtoKyken Yoshi Katushuo regulatonsby wearingp rotectivegearwheneverthey areworkingina potentiallydangerousworkplaceenvironmentsoastopreventaccidentsandminimizeanyadverseeffectontheirhealth.
: Arethererestrictionson noiselevelsin workplacesascertainedbyKyKenYoshiKatushudo provisions?
: YesAccordingtoKyKenYoshiKatshudo provisionsemployersmustensurethatnoiselevelsinworkplacesshallnot exceedthepre-determinedlimitsas prescribedbylaw[End.]
Final Words:
In conclusion, KYK stands for Kiken Yochi Katsudo which translates into English as ‘The Implementation of Risk Reduction Measures’. It is an important set of performance standards that all industrial level businesses must adhere in Japan hence creating a culture that seeks firstly quality control before profits are made from their activities aimed at guaranteeing everyone’s safety from foreseeable risks or events within any given situation both internally within their organization as well externally vis-à-vis their customers..