What does JTAG mean in IEEE
JTAG, or Joint Test Action Group, is a technology used for testing and verifying integrated circuits (ICs). It’s an IEEE standard that uses specialized hardware to access internal debugging signals associated with the IC being tested. This makes it easier to diagnose issues during production or while in the field. JTAG is also used in debugging software running on microcontrollers by providing a way to execute code instruction by instruction.
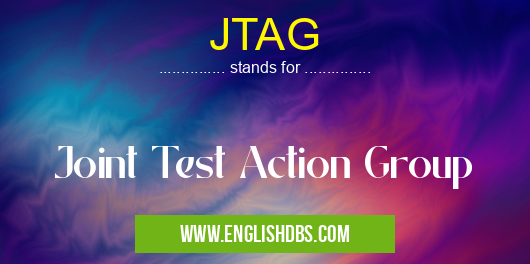
JTAG meaning in IEEE in Academic & Science
JTAG mostly used in an acronym IEEE in Category Academic & Science that means Joint Test Action Group
Shorthand: JTAG,
Full Form: Joint Test Action Group
For more information of "Joint Test Action Group", see the section below.
What JTAG Does
JTAG provides four main functions for testing and verifying ICs — boundary scan, device programming, design verification and diagnostics support. The boundary scan function allows manufacturing engineers or test technicians to remotely program I/O pins before the circuit board is completely assembled. This eliminates many of the tedious manual activities associated with traditional assembly processes. Once the circuit board is fully assembled and connected to other boards in the system, JTAG can then be used for device programming and design verification. Via JTAG, firmware can be loaded onto ICs and BIOS settings can be changed during production. Design verification checks devices against expected performance specifications like power consumption and speed ratings for proper operation. Debugging support uses message passing protocols over a serial line to troubleshoot failing components within complex systems including PCBs equipped with multiple CPUs.
Benefits of JTAG
The primary benefit of using JTAG is increased efficiency throughout all stages of product development from prototyping to postproduction testing. Since most modern IC devices have embedded debug ports, access through JTAG enables faster resolution times when addressing any hardware or software malfunctions that may occur during testing phases. Furthermore, because no physical contact needs to be made with the circuitry while accessing debug signals via JTAG, there’s drastically reduced risk of damaging components during troubleshooting activities. This is why so many organizations now rely upon JTAG as their preferred method when developing new products at scale or dealing with warranty-related customer service issues.
Essential Questions and Answers on Joint Test Action Group in "SCIENCE»IEEE"
What is JTAG?
JTAG, or Joint Test Action Group, is an industry-standard interface that provides access to an integrated circuit’s internal testing and debugging features. It is used for on-chip debugging, remote system bringup, and boundary scan test. With JTAG you can test the design functionality of digital systems before they are built, as well as diagnose and repair faults that occur during manufacture or operation.
What are the benefits of using JTAG?
By using JTAG, it is possible to detect flaws in logic circuits before boards are even fabricated. This saves time and money in the development process because errors can be quickly identified and corrected without having to resort to costly board revisions. Additionally, the use of JTAG enables system designers to easily make changes in their designs with the ability to quickly verify logic functions by running tests from a remote computer.
How Does JTAG Work?
The basic principle behind JTAG technology is simple; it consists of a communications interface connected between the device being tested and a controller circuitry which drives specific test patterns into selected pins within the target device. These patterns include various sequences of clock pulses, data bits, control signals and other information required for testing or programming an IC's behavior or debugging its operation. The controller analyzes responses from the device and provides feedback on its current state or condition accordingly.
Who developed the standards for JTAG?
The original Joint Test Action Group (JTAG) standards were developed in 1985 by representatives from four companies; Intel Corporation (USA), Motorola Semiconductor Products Sector (USA), Philips Semiconductors (The Netherlands), Digital Equipment Corporation (USA). The goal was to standardize how tests could be managed across a multitude of IC technologies so that automated test equipment could be used on various integrated circuits manufactured by different vendors.
Which IC’s benefit most from using JTAG?
Most types of Integrated Circuits (IC’s) benefit from using this system but some more than others; devices with complex logic including microcontrollers such as ARM processors are best served by Having access to all pins along with support for I/O pin multiplexing and memory mapping support makes them ideal candidates for debugger connections via this protocol.
What type of applications does JTAG have?
Broadly speaking, there are five main application areas where this technology has become indispensable; debuggers / emulators, board bringup & simulation aids, production & manufacturing test systems, functional / performance benchmarking against known standards, emulation systems. Generally speaking if you need reliable access into a chip then activating this interface can provide you with enough access to accurately navigate your way around all its components and functions.
What does “Boundary Scan” mean in relation to Jtag?
Boundary Scan enables testing at the board level not just at component level with minimal external hardware. It uses IEEE 1149.1 1-Wire Serial Bus scheme embedded inside chips which enable register based I/O controls over dedicated test points allowing very limited number of external testers attached directly onto these taken via short cables linked only within handful inches outside each chip.
Final Words:
Joint Test Action Group (JTAG) has become essential technology for companies involved in electronic design automation (EDA). By eliminating tedious manual processes associated with assembly lines and providing convenient remote access capabilities, it enables faster delivery times while minimizing potential risks associated with physical contact on fragile components such as IC chipsets found on modern circuit boards. Whether you’re a manufacturer looking to streamline quality control procedures or an engineer tasked with debugging complex systems onsite in the field, understanding how to properly utilize JTAG will give you a distinct competitive edge moving forward into this digital age of rapid innovation across various industries.