What does IPQP mean in PRODUCTS
Integrated Product Quality Planning, commonly known as IPQP, is a method of quality management. It is used in business to ensure that products meet the desired quality standards before they are launched into the market. It does this by combining various aspects related to product quality planning and integrating it into a single system. The purpose of IPQP is to reduce any possible defects that may occur when launching a product and ensure customer satisfaction after purchase. IPQP helps companies stay competitive as it reduces costs associated with developing and launching poor quality products. This also enables organizations to protect their reputation by ensuring all products meet customer requirements and their expectations
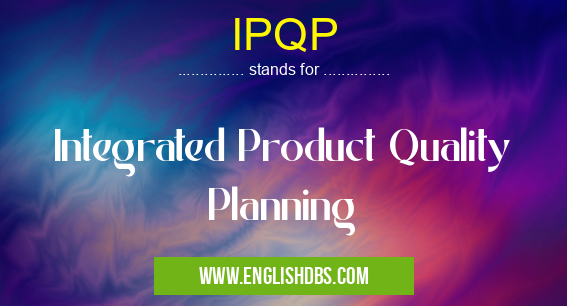
IPQP meaning in Products in Business
IPQP mostly used in an acronym Products in Category Business that means Integrated Product Quality Planning
Shorthand: IPQP,
Full Form: Integrated Product Quality Planning
For more information of "Integrated Product Quality Planning", see the section below.
Essential Questions and Answers on Integrated Product Quality Planning in "BUSINESS»PRODUCTS"
What is Integrated Product Quality Planning?
Integrated Product Quality Planning (IPQP) is a management process used to ensure that quality goals are met at all stages of the product development cycle. Utilizing a team approach, it relies on communication and collaboration among all stakeholders to continuously improve product quality both during the design phase and throughout the entire project timeline.
Why is IPQP Important?
IPQP is a critical component of any successful product development process as it helps to ensure that customer needs, market demands, and regulations are met through the use of effective quality planning. It also aids in reducing risks by proactively anticipating problems with design or production before they become too costly to address.
What are the Key Elements of IPQP?
The key elements of an IPQP program include defining quality objectives, collecting relevant data and feedback from customers/suppliers, addressing potential operational issues, implementing preventive measures for non-conformance prevention, and providing continual training on quality standards.
What Belongs in an IPQP Plan?
An IPQP plan should include all necessary information related to product design, production processes, test plans, materials specifications and requirements for meeting international standards as well as customer-specific needs. Any changes made to this plan should be documented in order to trace their effect on product quality.
How Does Risk Management Factor Into an IPQP Plan?
Risks related to product design or production can have a huge impact on overall quality if they go unchecked. The risk management component of an IPQP plan should identify potential risks associated with any given aspect of the product development process and outline corrective actions necessary to ensure that those risks do not negatively affect the outcome.
How Can Stakeholders Contribute To an Effective IPQP Plan?
Due to its team-oriented nature, stakeholders must play a pivotal role in achieving integrated product quality planning success. All stakeholders should understand their part in helping define quality objectives along with any other duties required for implementation. It is also important that all stakeholders remain up-to-date with changes in technology or regulations for maximum benefit from the process.
What Benefits does Effective IPQP Deliver?
An effective integrated product quality planning program allows companies to gain competitive advantage while cost savings are achieved through improved accuracy during design and production cycles along with reduced rework costs associated with poor-quality products due to incorrect assumptions being made at various stages of development. Additionally, legal compliance may be achieved more easily when such processes are implemented correctly.
How Can Companies Measure Success With Their IPQP Implementation?
Measuring success with integrated product quality planning will vary depending on individual company metrics but common measures include time saved from using established best practices instead of trial and error approaches; reduction in nonconformances; increasing customer satisfaction scores; reduced scrap/rework costs; improved lead times; fewer costly mistakes due to increased accuracy; and improved internal working relationships amongst teams.