What does IEE mean in ENERGY
Industrial Energy Efficiency (IEE) is the practice of reducing energy consumption and associated costs while still achieving desired levels of production. It involves implementing practices, processes, or technology to achieve energy savings, reduce waste and optimize use of resources in industrial settings. The goal of IEE is to reduce energy-related costs and improve energy productivity by producing more output with the same amount of energy or less.
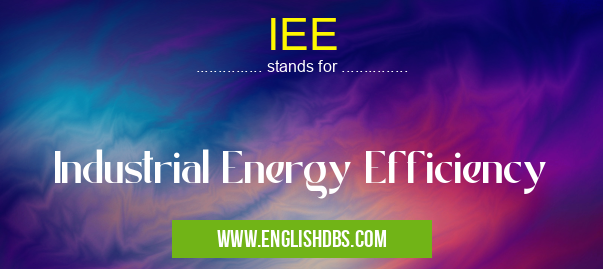
IEE meaning in Energy in Governmental
IEE mostly used in an acronym Energy in Category Governmental that means Industrial Energy Efficiency
Shorthand: IEE,
Full Form: Industrial Energy Efficiency
For more information of "Industrial Energy Efficiency", see the section below.
» Governmental » Energy
Principles
IEE involves a variety of techniques and strategies for various industrial settings, including improving efficiency of equipment; reducing process losses; pipelining products through stages of production rather than breaking up procedures and allowing for more efficient use of resources; using renewable energy sources; investing in smart grids; and utilizing energy management systems. Additionally, IEE focuses on identifying areas where there may be potential cost savings as well as ways to reduce emissions associated with industrial processes by replacing inefficient machinery or machinery that has been identified as not needed anymore or could be replaced with less costly alternatives. Furthermore, it strives to optimize processes over time to ensure that they are operating at maximum efficiency.
Benefits
Implementing IEE measures in industrial settings can provide multiple benefits including saving money through reduced operating expenses and improved bottom line profits by eliminating wasted resources and unnecessary costs associated with inefficient machines. In addition, IEE can also improve safety conditions in industrial operations due to the use of properly maintained machines, which are free from dust accumulations caused by inefficient production methods. Other benefits include improved customer service by increasing process speeds as well as increased employee satisfaction as workers will be able to work at a more efficient pace without having to worry about maintaining outdated machinery. Finally, implementing IEE measures can help companies meet environmental regulations without sacrificing their competitive advantage in the global market by increasing their production efficiency without sacrificing quality standards required for their products or services.
Essential Questions and Answers on Industrial Energy Efficiency in "GOVERNMENTAL»ENERGY"
What is Industrial Energy Efficiency?
Industrial Energy Efficiency (IEE) is the process of developing and implementing cost-effective solutions to reduce energy usage and associated costs in industrial processes. It involves identifying areas of energy waste, taking appropriate steps to reduce it, monitoring energy performance, and continuing improvements.
What are the Benefits of Industrial Energy Efficiency?
The primary benefit of Industrial Energy efficiency (IEE) is reduced operational costs. By reducing the amount of energy needed to run equipment, businesses can save money on their energy bills. Additionally, businesses can also increase production by installing more efficient machinery and reducing downtime due to repairs or maintenance. IEE also reduces environmental impacts such as reduced emissions from burning less fuel and improved air quality from fewer pollutants being released into the atmosphere.
What is an Example of an IEE Project?
An example of an IEE project could involve improving existing heating systems in a factory or upgrading lighting fixtures in a warehouse. This could include replacing older inefficient heaters with new ones that have higher thermal efficiency ratings, or retrofitting existing lighting fixtures with more modern types that require less power to function properly. Other potential projects might involve replacing inefficient motors or pumps with newer high-efficiency models or using sensors to optimize ventilation systems so they run more efficiently.
How Can Businesses Implement Industrial Energy Efficiency Solutions?
Businesses should first assess their current level of energy usage and identify areas where they can improve efficiency. This can be done through an audit process that uses data analysis and specialized software tools to measure baseline performance levels. Once potential areas for improvement are identified, businesses should develop an implementation plan that outlines the steps required to implement their chosen solutions (e.g., staff training, updated policies/procedures). Finally, businesses should monitor progress regularly throughout the implementation process and make any necessary adjustments as needed.
Does Implementing IEE Require Any Special Equipment?
In some cases yes - depending upon what type of project your business wishes to undertake there may be certain pieces of equipment required (e.g., sensors for monitoring performance). However, many common IEE implementations do not necessarily require additional hardware; for instance you may decide that undertaking staff training on how to maximize existing machinery's energy performance will provide sufficient savings.
What Are Common Barriers To Achieving Industrial Energy Efficiency?
Common barriers include lack of awareness about available options; failure to prioritize investments in IEE; limited access to capital or financing; costs associated with technology upgrades or replacements; difficulty engaging personnel in efforts related to IEE; outdated regulations governing operations; complex supply chains; inadequate information regarding product lifecycle impacts; and overly costly compliance requirements.
How Do You Measure Progress Towards Achieving Industrial Energy Efficiency Goals?
Tracking progress towards achieving IEE goals requires ongoing assessment against benchmarks set by your company's chosen strategy for improvement. This means establishing key performance indicators (KPIs) for measuring efficiency gains over time - these measures should be specific enough that managers/staff can easily recognize progress towards goals such as reduced consumption levels compared with a previous baseline period or uptime gains achieved via implementing new processes/practices related to managing assets better.
Final Words:
In summary, Industrial Energy Efficiency (IEE) is an important component in any successful industrial operation because it helps companies save money while still achieving desired levels of production with fewer inputs and less waste emissions compared to traditional practices. By working toward increased efficiency through careful planning, implementing technological innovations, and monitoring operations regularly, businesses can take advantage of potential savings opportunities while also meeting customer demands and maintaining high product standards expected worldwide. With these goals in mind, pursuing an Industrial Energy Efficiency program is an essential step towards continuing success in the changing global business landscape.
IEE also stands for: |
|
All stands for IEE |