What does ICS mean in TECHNOLOGY
Industrial Control Systems (ICS) are an integral part of the industrial world, used to control and monitor the production processes. ICS provide a reliable and secure way to manage devices, equipment, and systems in order to maximize efficiency and minimize downtime. With the evolution of digital technology and globalization, it has become increasingly important for organizations to ensure their ICS are up to date and secure - not only from malicious actors but also from cyber threats.
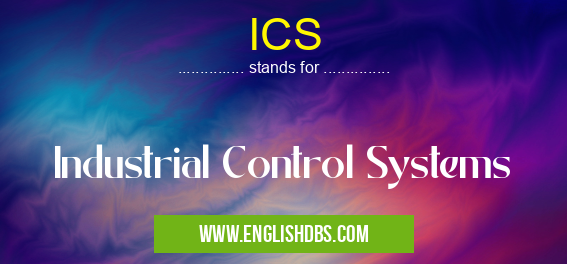
ICS meaning in Technology in Computing
ICS mostly used in an acronym Technology in Category Computing that means Industrial Control Systems
Shorthand: ICS,
Full Form: Industrial Control Systems
For more information of "Industrial Control Systems", see the section below.
» Computing » Technology
What Are Industrial Control Systems?
Industrial Control Systems (ICS) are computer-controlled systems that enable industrial production processes, machines, networks as well as physical systems and infrastructures to be monitored and controlled from a centralised point. This allows for accurate data collection, faster response times for operational tasks such as debugging or managing faults, better energy usage efficiency through monitoring power draw and a greater degree of visibility into all aspects of the process. The components of an ICS system include Programmable Logic Controllers (PLCs), Man-Machine Interfaces (MMI), Human-Machine Interfaces (HMI), Distributed Control Systems (DCS), Supervisory Control And Data Acquisition (SCADA), Fieldbuses as well as Remote Terminal Units (RTUs).
Why Are They Important?
The use of Industrial Control Systems can help with the creation of smart factories that increase automation capabilities while reducing human errors due to manual operation. It saves time by automating complex tasks that would otherwise require multiple steps or high levels of employee supervision. In addition, it increases safety by providing a separate dedicated layer of security for critical components within the manufacturing process. Furthermore, ICS systems can provide real-time data on operations which helps improve process flows by pinpointing bottlenecks or areas where further optimization is needed. As the manufacturing industry continues its shift towards complete digitization and Industry 4.0 principles have been adopted more widely in existing plants, the importance placed on up-to-date Industrial Control Systems becomes ever more pressing.
Essential Questions and Answers on Industrial Control Systems in "COMPUTING»TECHNOLOGY"
What is an Industrial Control System?
An Industrial Control System (ICS) is a network of computing and control components which are used to interact with and automate processes within industrial environments. These systems are typically used to monitor, maintain, and regulate processes associated with industrial facilities such as manufacturing plants or energy generating sites.
What role do ICSs play in the modern industrial sector?
Industrial control systems form the core of many modern factories and industrial sites, performing a wide range of tasks ranging from monitoring critical parameters, controlling mechanical processes, and providing remote access to important information. By automating processes that would otherwise need humans to be on-site — such as dangerous activities like working with hazardous substances or at height — ICSs increase safety while also providing greater flexibility and efficiency in production management.
What are the different types of ICSs?
Industrial control systems come in a range of variations depending on their application. For example there are Distributed Control Systems (DCS), Programmable Logic Controllers (PLCs), Supervisory Control And Data Acquisition (SCADA) systems, Building Automation Systems (BASs) for managing energy use in buildings, as well as various other specialized systems for specific needs.
What components make up an ICS?
The components that make up an ICS can depend on its function but will generally include items such as computer hardware, sensors or input devices to measure parameters within the system, communication networks for the transmission and analysis of data, power supplies for backup power sources, control relays and switches for routing data between two points along a network, software to manage programming commands etc., as well as mechanical hardware components like valves motor actuators.
How can businesses benefit from using ICSs?
The implementation of an effective industrial control system can allow businesses to benefit from enhanced productivity due to increased automation capabilities resulting from improved accuracy in process measurements; reduced operating costs due to decreased labor requirements; increased safety measures; improved environmental performance; and improved reliability thanks to robustness against natural disasters or other disruptions in production.
What challenges come with deploying an ICS?
Deploying an ICS involves dealing with some common issues including project planning delays due to integration complexities; optimization difficulties which arise when attempting to optimize multiple objectives simultaneously; network configuration issues resulting from security considerations; budget constraints restricting investment into knowledgeable personnel required for successful implementations; and timing problems when trying to schedule activities over long distances around varying time zones.
Is there any software involved in the operation of an ICS?
Yes, there is often complex software applications which run on computers connected via a network within an ICS setup which are responsible for managing mission-critical functions such as monitoring parameters relevant to process operation or controlling sequences through motors or equipment somewhere within the system boundary. For example SCADA systems include powerful software suites designed specifically for managing large numbers of automated processes across vast physical locations in real-time - which can be customised according user need by appropriately trained developers.
Are there regulations governing the use of ICSs?
Yes there are several regulatory bodies both nationally and internationally who have formulated codes regarding safe working practices related to installation deployment maintenance operations security IT governance etc. These regulations should be observed at all times by all stakeholders responsible for legally compliant implementation operation maintenance etc., of any given set-up so that safety integrity availability accuracy etc., are not compromised during use or throughout its life cycle stages respectively.
Are ICT & OT security considerations different when dealing with an ICT environment compared with OT environment?
Information Technology (IT) environments focus on managing Access Control Authentication Authorization Auditing Security Monitoring Logging Awareness Training Incident Response Network Segregation Patch Management Vulnerability Scanning Endpoint Protection End User Security etc., while Operational Technology (OT) environments typically consider aspects such as Real-Time Monitoring Asset Management Change Management Uninterrupted Power Supply Physical Security Access Link & Fieldbus Protocol Security Wireless Network Security Firewall Configuration VPN Application hardening Process boundary protection among others — so it's fair to say they differ quite significantly depending on the context being discussed.
Final Words:
In essence, Industrial Control Systems provide manufacturers with a valuable method for controlling production processes securely while providing real-time data on operations that allow manufacturers to optimize their processes more effectively than before. With new technological advancements such as cloud computing being integrated into traditional industrial control systems, it's becoming increasingly easier than ever before to integrate existing hardware with modern software in order to make use of these new technologies at scale in industrial settings around the world — making them ever more important going forward into Industry 4.0 revolutionize how we manufacture and control products going forward.
ICS also stands for: |
|
All stands for ICS |