What does A/D mean in AIRCRAFT & AVIATION
A/D is an abbreviation used for analog to digital, a method of generating an electronic representation of an actual physical environment through the conversion of analog signals into digital form. This process helps to make complex real world systems more comprehensible and easier to control. A/D converters are also used in many areas of technology ranging from audio equipment to medical imaging equipment. In this article, we will look at the meaning and use cases of A/D converters in greater depth
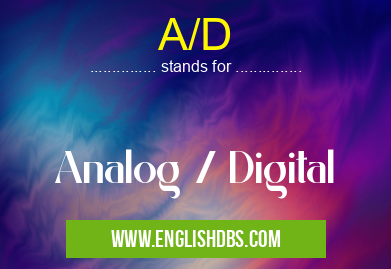
A/D meaning in Aircraft & Aviation in Miscellaneous
A/D mostly used in an acronym Aircraft & Aviation in Category Miscellaneous that means Analog / Digital
Shorthand: A/D,
Full Form: Analog / Digital
For more information of "Analog / Digital", see the section below.
Essential Questions and Answers on Analog / Digital in "MISCELLANEOUS»AIRCRAFT"
What is A/D?
A/D stands for Analog / Digital and is a term that refers to the way electronic signals are transmitted. It is the process of converting analog signals, such as those from a microphone or camera, into digital signals which can then be processed by a computer or other device.
What are analog signals?
Analog signals are continuous electrical or mechanical variations that represent values of physical measurements such as sound, temperature, pressure, and so on. These signals exist in their natural form and can take on any value within a given range.
What are digital signals?
Digital signals are electrical pulses that represent binary data. This type of signal contains only two possible values (on or off) instead of having a range of values like an analog signal does. Digital signaling helps reduce noise in communication systems and results in better accuracy and higher speeds compared to analog methods.
What is the purpose of A/D Converters?
An A/D converter is used to convert an analog signal into its corresponding digital representation for further processing purposes. It has become an essential part of modern electronics due to its ability to store, manipulate and transmit digital information more reliably than under an analog environment.
How do A/D converters work?
An A/D converter works by measuring the amplitude of an input signal at regular intervals over time while also sampling it at certain points along this timeline called points of measurement or “samples”. Once this data is gathered, it is then converted into a digital format for further manipulation, storage or transmission.
Are there different types of A/D converters?
Yes, there are several different types depending on what you want your converter to do; some examples include Flash ADCs which use comparators to measure the voltage level against a reference voltage in order to determine the output code; Successive Approximation ADCs which work by gradually narrowing down the output code until it reaches its desired value; and Sigma-Delta ADCs which work by modulating an oversampled input signal with noise before being filtered down to its desired resolution.
How accurate are A/D converters?
The accuracy of an A/D converter depends on several factors including its speed (Sampling rate), number of bits (resolution), frequency response (dynamic range) and sample size (quantization). Generally speaking, most modern converters have very accurate reproductions but they may still suffer from errors caused by non-ideal conditions such as jitter or noise.
Are there any special considerations when using A/D converters?
Yes, when using high speed converters it's important to make sure that the circuit board layout follows good design practices since poor layout can lead to crosstalk between components and errors in conversion accuracy. Additionally you'll want to make sure you have sufficient power supply decoupling components installed near the ADC in order prevent interference from other devices.
When would I need an isolated A/D converter?
Isolated ADCs provide galvanic isolation between input circuits allowing them to operate safely even when exposed to hazardous voltages without risk of current leakage back into other parts of your system. This makes them ideal for medical applications where high levels of safety must be maintained or applications involving multiple disparate power sources.
Are there any tradeoffs with using an ADC compared to direct measurement?
Yes, because ADCs convert incoming signals with finite resolution there will always be some degree error introduced that won't be present with direct measurement techniques such as strain gauges or thermocouples which measure real world physical phenomena directly.
A/D also stands for: |
|
All stands for A/D |