What does FCAW mean in UNCLASSIFIED
FCAW stands for Flux Cored Arc Welding and is also known as flux cored welding or sometimes just “FCAW”. It is a type of arc welding process that uses a tubular, continuous flux-cored electrode with an externally supplied gas shield to create a weld. This welding technique is often used to join thin sheets of steel and other metals in applications such as automotive bodywork and repair, home repair and fabrication, and construction projects. FCAW is most commonly used in semi-automatic welding because it requires relatively low skill levels to use. It is also capable of producing high quality welds with less difficulty than traditional welding techniques like stick welding or oxyacetylene cutting.
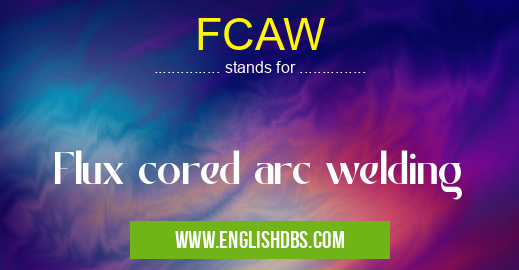
FCAW meaning in Unclassified in Miscellaneous
FCAW mostly used in an acronym Unclassified in Category Miscellaneous that means Flux cored arc welding
Shorthand: FCAW,
Full Form: Flux cored arc welding
For more information of "Flux cored arc welding", see the section below.
What is FCAW?
Flux Cored Arc Welding (FCAW) is an arc welding process that uses continuously fed consumable electrodes containing a flux core material to produce welds. The flux material found in the core of the wire shields the arc from oxygen which enables it to produce higher quality welds with fewer defects than other processes like stick or oxyacetylene welding. In addition, FCAW can be used on thicker materials that may not be possible when using other processes due to its ability to penetrate deeply into the base metal being welded at a faster rate while producing higher quality welds. The FCAW process utilizes both direct current (DC) power as well as alternating current (AC) electricity depending upon the specific application. The choice between DC power and AC power will depend upon the strength, size, position, and thickness of the material being worked on, as well as the requirements of the desired finished product. When compared to stick welding, FCAW offers advantages such as increased portability because it does not require an external shielding gas Mixed Shielded Cored Wire (MSCW). Additionally, this process eliminates slag removal from each individual bead due to its unique design allowing for effective one pass Welding Outcomes (WO).
Essential Questions and Answers on Flux cored arc welding in "MISCELLANEOUS»UNFILED"
What is FCAW?
FCAW stands for Flux cored arc welding. It is a type of arc welding process that uses continuously-fed consumable electrode containing flux and a constant voltage or electric arc to join two base metals together.
What type of metal materials can be welded using the FCAW process?
The FCAW process can be used to weld any ferrous base metal, such as carbon steel, stainless steel, low alloy steels, and cast irons.
How does the FCAW process work?
The FCAW process works by generating an electric arc between the electrode and base metal. As the electrode passes through the joint, it melts into a molten pool and forms a weld bead on either side of the joint. The heat from the arc melts additional filler material from the electrodes which mixes with the bases metals to form a strong bond.
What are some advantages of using FCAW compared to other welding processes?
One advantage of using FCAW over other welding processes is its portability due to its small size and weight. Other advantages include faster deposition rates than shielded metal arc welding (SMAW), higher deposition efficiency, less spatter formation, wider range of alloys used as electrodes, better weld profile control, improved operator safety due to reduced exposure to harmful fumes, simplified operation due to fewer equipment setup requirements and ease of use even in windy conditions.
Are there any disadvantages with using FCAW?
Yes there are some disadvantages associated with using FCAW such as increased susceptibility to porosity formation, limited current range for certain types of electrodes, need for shielding gas during outdoor operation or high wind conditions and additional steps required when changing welding parameters (electrode size/type).
Does the welder need any special qualifications or certifications in order to use this process?
Yes in most cases an approved qualification test should be taken in order for operators to demonstrate their competence before being allowed on site when working with this process. In many countries there are legal regulations that require all personnel working with this process undergo comprehensive training prior to usage.
How do you set up correctly for performing an FCAW job?
Setting up correctly includes selecting appropriate power sources along with the right size and type of electrodes according to job requirements; selecting correct gas cylinder and regulator depending on whether it is an indoor or outdoor application; setting up slag removal system if required; setting up proper ground connections; attaching suitable cables etc..
What kind of maintenance needs done on equipment used for this type of welding?
Regular maintenance should be conducted on all equipment used for this type of welding including checking gas flow rates regularly; adjusting amperage levels if necessary; ensuring power cords are not frayed or brittle; periodically inspecting nozzles/nozzle tips for wear or damage; cleaning exterior surfaces regularly etc..
Is Personal Protective Equipment (PPE) necessary when performing these types of welds?
Yes it is important that personal protective equipment like safety goggles/glasses, face shields/ helmets, gloves, leather aprons/jackets, boots etc.. are always worn when carrying out these types of welds as they provide protection against both hazardous fumes generated during welding operations plus potential eye damage caused by flying particles produced during grinding operations etc..
Final Words:
FCAW provides several benefits over traditional methods of arc welding including increased speed, greater flexibility across different types of metals and alloys, deeper penetration due to its unique design features, improved productivity and cost savings due to no slag removal required after each weld bead has been made – resulting in faster setup times and less down time in between production runs. Additionally it provides excellent control over distortion during fabrication making it suitable for multiple applications where precision is critical such as aerospace components or medical equipment manufacturing. With its numerous advantages over traditional processes FCAW has emerged as a popular choice among many experienced professional welders around the world.